5.1 DEFINTIONS OF PETROCHEMICALS
Petrochemicals are chemicals derived from petroleum products. Examples of petrochemicals are plastics, rubbers, fi bres, paints, solvents, and detergents. In fact, petroleum products are mixtures of hydrocarbons, whereas the raw materials for petrochemicals are pure hydrocarbons separated and converted to desirable products, such as polymers, solvents, and surfactants, usually in several stages and may be grouped as (1) feedstocks (fi rst-generation petrochemicals), (2) intermediates (second-generation petrochemicals), and (3) fi nished products (third-generation petrochemicals). Products similar to petrochemicals derived from non-petroleum sources are not strictly petrochemicals. For example, cellulose, natural rubber, natural resins, nylon 11, and ethanol of plant origin are strictly non-petrochemicals. Coal distillation is also a source of varieties of coal chemicals, e.g., benzene, toluene, xylene, and naphthalene. In fact, before petroleum sources were known, coal chemicals were used to produce a variety of products. Many of the chemicals from non-petroleum sources are co-processed with petrochemicals to the fi nished product. Non-hydrocarbons obtained from petroleum, e.g., hydrogen, carbon monoxide, carbon dioxide, sulfur, and carbon, are also loosely called petrochemicals. Hydrogen, nitrogen and oxides of carbon manufactured from steam reforming and partial oxidation of naphtha are also petrochemicals. These are used for production of ammonia, urea, melamine, fertilizer, etc.
5.1.1 FEEDSTOCKS
Feedstocks are the raw hydrocarbons obtained from crude oil refi ning by distillation and thermal and catalytic processes. For instance, hydrocarbon gases and naphtha are available from atmospheric distillation of crude oil; similarly, benzene, toluene, and xylene, obtained by catalytic reforming and catalytic cracking processes, are the major raw materials for the manufacture of second-generation petrochemicals. Benzene, toluene, xylene, and heavier aromatics are also generated as by-products from petrochemical plants. Thus, the feedstocks for petrochemical plants are either directly obtained from refi neries or are further processed to generate them in the petrochemical plant itself. Natural gas and refi nery products are the major source of feedstocks for petrochemicals. A list of the major petrochemicals is given in Table 5.1.
5.1.2 INTERMEDIATES
Thermal cracking of ethane, propane, butane, and naphtha produces cracked gases or olefi ns (ethylene, propylene, butylenes, acetylene, etc.) and liquids (benzene, toluene,
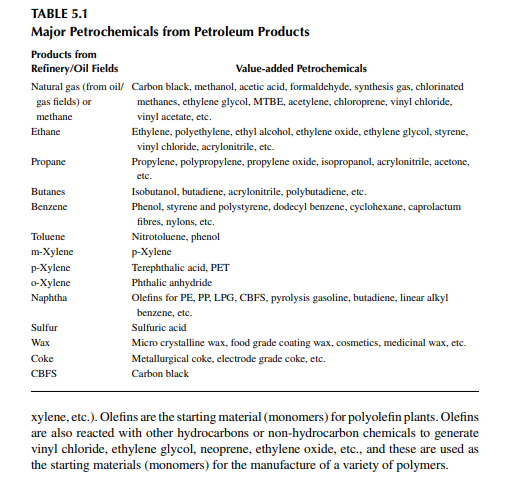
5.1.3 FINISHED PRODUCTS
Using the above intermediates, a variety of plastics, rubber, fi bre, solvent, paint, etc., are manufactured. Polymerisation reactions are carried out for these monomers or intermediates to various polymers, resinous and liquid products. Plastics are available in the form of extrudates, granules, powders, beads, etc., from the manufacturing units as the fi nished products. These are converted into plastic commodities, such as bags, fi lms, furniture, and products of various shapes and sizes by casting, moulding, or blowing machines, as the marketable products. Plastics are classifi ed into two types, namely, thermoplastic (or thermoplast) and thermosetting plastics (or thermoset). Thermoplasts, usually linear in molecular structure, can be melted (or softened) by heating and solidifi ed (or hardened) by cooling. This heating and cooling cycle can be repeated indefi nitely without loss of the original properties. But thermosets will be permanently transformed to a chemically cross linked or non-linear structure and cannot be returned to their original property during a heating and cooling cycle. Plastics
are also known as plastomers with a high modulus of elasticity. Synthetic fi bres are made from polymers that have a high modulus of elasticity as compared to plastics and rubbers. These polymers are also available in the form of extrudates, powders, and beads, which are converted to fi bres in a drawing mechanism and are collected in bales. Rubbers or elastomers are polymers with a low modulus of elasticity. Raw rubber is available from the polymerisation unit in the form of sheets, which are cut and blended with various chemical ingredients along with sulfur (known as vulcanization) to achieve the desired quality for making tyres and other products. A variety of chemical reactions are involved in the petrochemical manufacturing processes. Most of these reactions are catalytic with heat effects. Examples are dissociation, dehydrogenation, hydrogenation, addition, polymerisation, and condensation. Dissociation reactions occur during the thermal and catalytic cracking process. Dehydrogenation also occurs catalytically or thermally during cracking. Additional reactions, such as oxidation, chlorination, fl uorination, and sulfonation of the parent olefi n or aromatic hydrocarbons, are required to make intermediates or monomers. Polymerisation occurs mostly in the presence of initiators or catalysts with heat evolution. Two types of polymerisation reactions occur, i.e., addition polymerisation and condensation polymerisation. Addition polymerisation involves a chain reaction in which monomer molecules join in a chain. For example, olefi ns or diolefi ns are polymerised in the presence of initiators, such as free radicals, ionic compounds, or complexes. Condensation polymerisation involves two monomers, same or different, which combine to form a polymer with the elimination of small molecular weight by-products like water. A large number of unit operations and processes are involved in a petrochemical plant. Since catalysts play a major role in the synthesis of petrochemicals, research and development of new catalysts is a continuous endeavour by the manufacturers. It is also to be noted that in a polymerisation plant, catalysts may not be recovered rather this is entrained in and become a part of the polymer. The presence of catalyst ingredients in the polymer per unit mass may pose a problem as far as quality is concerned. Hence, a catalyst is selected that requires minimum consumption. The reactors used are tubular, stirred tank or kettle type. These may be packed bed or fl uidized bed types, Both single and multiple numbers of reactors are used. The selection of a suitable reactor is a challenging decision in a petrochemical manufacturing unit.
5.2 NAPHTHA CRACKING
Major plastics are manufactured from olefi ns, which are available either by cracking of gases (gas-based petrochemicals), such as methane, ethane, propane and butane, or from naphtha (naphtha-based petrochemicals). Due to the larger availability of naphtha and the low energy requirement for cracking as compared to gases, naphtha cracking is widely accepted for the manufacture of olefi ns. Naphtha is a mixture of hydrocarbons boiling in the range of the lowest boiling component (C5) to 150°C, which contains paraffi ns, naphthenes, and aromatics in various proportions. It is found that paraffi ns, i.e., straight chain hydrocarbons, yield olefi ns when heated at a high temperature. The branched chain and aromatic hydrocarbons, on the other hand, become heavier or decomposed to carbon. It is also a fact that the yield of olefi ns decreases with the increasing molecular weight (hence with boiling point) of the hydrocarbons. For example, if ethane is thermally cracked, it will yield 80% ethylene, while from propane, butane, naphtha, and gas oil as feedstocks, if cracked separately the yields will be 45%, 37%, 30%, and 25%, respectively. Hence, the desirable feedstock naphtha should have a very high content of paraffi ns and be in the lower boiling range. A suitable boiling range for feedstock naphtha for olefi n production is below 100°C and should have a paraffi n content of more than 75%. Usually, naphtha in the boiling range of 90°C−150°C is catalytically reformed (as discussed in Chapter 3) in a refi nery either to produce gasoline or aromatics. Hence, in the refi nery, C5−90°C cut is separated in the naphtha redistillation unit and is sold to the petrochemical industry. Naphtha cracking is carried out in a tube-still furnace at a temperature above 800°C. Due to thermal cracking, the following cracking endothermic reaction takes place,
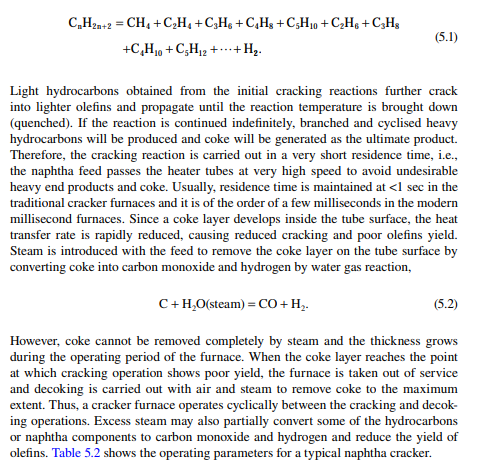
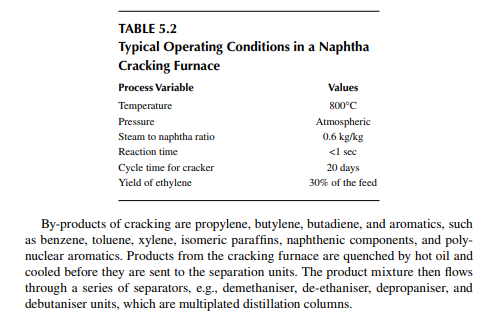
5.2.1 PRIMARY FRACTIONATOR OR STABILISER
Cracked liquids and gases are separated in a fractionating column the bottom product of which is the heavy cracked oil rich in high boiling aromatics. This heavy oil is also partly used as the quenching medium for the products from the furnace and partly sold as the carbon black feedstock (CBFS) due to its heavy aromatic contents. Cracked gases containing hydrocarbons, both saturated and unsaturated, from methane to C7 hydrocarbons emerge from the top of the column, which is then compressed and amine (or caustic) washed to remove hydrogen sulfi de and carbon dioxide gases. This is illustrated in Figure 5.1.
5.2.2 HYDROGEN SEPARATOR
Amine or caustic washed gases are then passed through a fl ash separator vessel, where liquid hydrocarbon gases are separated from hydrogen at high pressure and low temperature. Hydrogen from this vessel is used in the hydrogenating units, such as pyrolysis gasoline and butadiene hydrogenation, or as a fuel. Demethaniser: Liquifi ed gases from a hydrogen separator are then separated from methane in a distillation column where methane (C1) emerges from the top and is used as a fuel for the cracking furnace. The bottom of the column is then passed to a de-ethaniser. De-ethaniser: It is also a distillation column that separates ethane and ethylene mixture (C2 mixture) as the top product from the rest of the liquifi ed gases containing propane, propylene, butane, butylenes, etc.
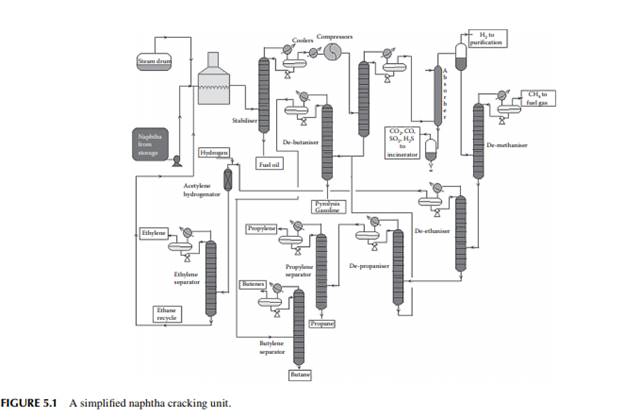
Ethane-ethylene separator: A C2 mixture from the top of the de-ethaniser column is then passed through another distillation column that separates ethylene as the top product and ethane as the bottom product. Ethylene is sent to storage and is used up in the polyethylene (PE) synthesis plant. Ethane from this column is recycled to a small cracking furnace to yield additional ethylene. Depropaniser: The liquifi ed gas mixture from the bottom of the de-ethaniser is separated from propane and propylene (C3 mixture), which leaves from the top of the column and enters the propane–propylene fractionator. The bottom product contains the butanes, butenes, butadiene, and heavier components, which are then separated from the butane–butene mixture (C4 mixture). Propane–propylene separator: In this column, propylene is recovered as the top product and propane as the bottom product. Propylene is stored and used for manufacturing polypropylene, and propane is sold as a domestic fuel—liquifi ed petroleum gas (LPG). Debutaniser: Butane, butenes, and butadiene (C4 mixture) are recovered as the top product and components heavier than the C4 mixture, i.e., C5 and heavier, are recovered as the pyrolysis gasoline (bottom product). Pyrolysis gasoline is catalytically hydrodesulfurised before it is sold or blended as a gasoline component. A gasoline hydrodesulfurisation unit is similar to a naphtha pretreatment unit described in Chapter 3. A simplifi ed fl ow sheet of a naphtha cracking unit (NCU) is shown in Figure 5.1. Typical yields of products from a naphtha cracking unit is presented in Table 5.3.
5.3 CONVERSION PROCESSES FOR SELECTED PETROCHEMICALS
5.3.1 POLYETHYLENE
Polyethylene (PE) has evolved as a major plastic and is obtained by polymerising ethylene. Three main types of PE plastics are obtained—low density polyethylene (LDPE), linear low density polyethylene (LLDPE), and high density polyethylene (HDPE)—depending on the type of polymerising process, which are described in the following sections. PE is the polymer (poly + monomer) of ethylene molecules. This product is used to make a variety of plastics. Polymerisation of ethylene molecules into heavy molecular weight PE is a reaction in which a chain of macromolecule, is produced by the combination of ethylene molecules. Ethylene is a highly reactive monomer that starts combining with other molecules of ethylene in the presence of a catalyst (Ziegler–Nutta catalyst) under a certain pressure and temperature. The reaction steps are in three stages, namely, initiation, propagation, and termination. A radical molecule is formed in the presence of the catalyst in the initiation step. The radical then starts combining with the monomers repeatedly in the propagation stage, which continues indefi nitely as long as the monomer molecules are available during reaction until quenched at the termination stage. The properties of a polymer vary with the operating pressure, temperature, and time of reaction. The reaction is exothermic and hence it is essential to control temperature by a proper heat removal system.
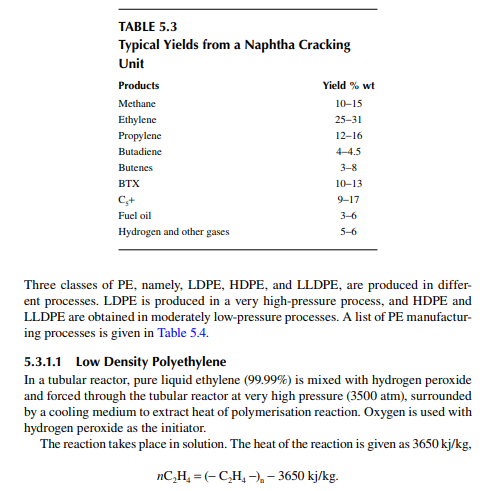
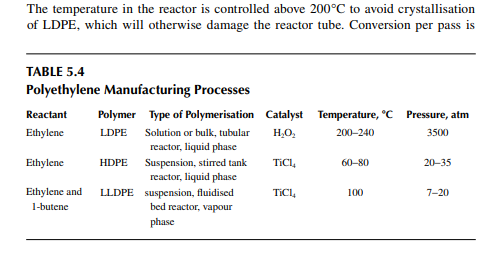
about 20%. Effl uent from the reactor, consisting of the product and the unconverted monomer, is separated by high and low pressure separator vessels. Ethylene is recycled to the reactor. The overall conversion achieved by recycling is about 95%−97%. Finally, the molten LDPE is withdrawn from the low pressure separator and extruded, followed by cooling, drying, and pilling. As tubular reactors are prone to plugging and poor heat transfer problems, a thick-walled, stirred tank vessel reactor is used. High-speed agitation helps in good heat transfer. If the agitator stops, the temperature will rise to such an extent that explosion may takes place because of the presence of oxygen in the reaction mixture. Figure 5.2 is a schematic fl ow diagram of an LDPE manufacturing process. LDPE is used for making fi lms, sheets, tubes, blocks, insulation, hoses etc. But, it cannot be used at temperatures above 80°C because deformation will occur. It has excellent dielectric properties, good elasticity up to −60°C, and it is anti-corrosive. It is soft and waxy and is used to make fi lms.
5.3.1.2 High Density Polyethylene
HDPE is manufactured by the suspension polymerisation method. In this method, high purity ethylene is introduced into the reactor vessel in which a catalyst (Ziegler-Nutta catalyst, TiCl4 in alkyl aluminium) is suspended in benzene at a pressure of 20−35 atm and at a temperature of 60°C−80°C. The ratio of alkyl
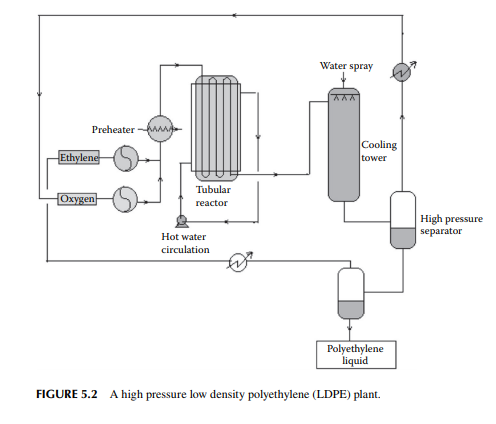
aluminium and titanium chloride determines the size of the polymer. The greater the ratio, the greater the molecular weight of the polymer. After the reaction, the polymer mixture is separated from ethylene and inerts in a fl ash drum. The polymer is water washed and fi ltered to recover the catalyst (water soluble) and reused. However, recovery of the catalyst from the polymer is not complete. Catalyst consumption is about 1 g of titanium (Ti) per 1500 kg of polymer. This is due to the high residual presence of the catalyst within the polymer. The presence of this impurity limits the HDPE’s applications. A modern catalyst has been developed that can yield 6000 kg polymer per gram of Ti, where the contamination of Ti metal in the polymer is a few parts per million. A fl ow diagram of a HDPE plant is shown in Figure 5.3. HDPE has a rigid and translucent property and is suitable for making electrical goods, bottles, ropes, etc. The main economic advantage of HDPE is that it can be manufactured at much lower pressure as compared to LDPE. HDPE has a higher melting temperature than LDPE and has almost the same glass transition temperature.
5.3.1.3 LINEAR LOW-DENSITY POLYETHYLENE LLDPE
is a copolymer of ethylene and 1-butene having linear structure? Today, it is produced by a low pressure fl uidised bed process where the temperature and pressure are 100°C and 7−20 atm (0.7−2 MPa), respectively. Gaseous monomers are
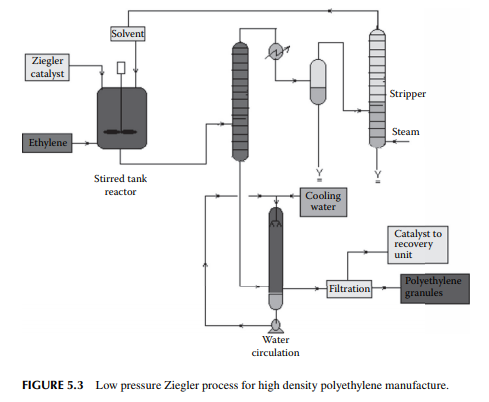
used to fl uidise the polymer granules previously prepared. During polymerisation, additional polymers are produced of specifi c sizes depending on the seed polymers present. Unreacted monomers are separated from the effl uent and recycled to the reactor. A long residence time in the range of 3−5 h is required for a reaction. Such a process is shown in Figure 5.4. HDPE is also produced by a similar fl uidised method in modern plants.
5.3.2 POLYPROPYLENE
After PE, polypropylene is a valuable polymer and is used as plastic for making pipes, ropes, fi bres, etc. It is manufactured by catalytic reaction in a stirred tank reactor, where Ti and aluminium halides are used as catalysts at a temperature of 60°C−70°C and a pressure of 1−2 MPa. An unreacted monomer is recycled after it is separated from the catalyst and polymer mixture in a fl ash chamber under vigorous stirring conditions. The mixture of polymer and catalyst is then passed to a centrifugal separator where a catalyst and polypropylene polymer is recovered. Further processing of the spent catalyst in the presence of alcohol is carried out to recover the active components of the catalyst for its reuse. A polypropylene plant is shown in Figure 5.5.
5.3.3 POLYETHYLENE TEREPHTHALATE
Polyethylene terephthalate (PET) is also known as polyester. This is produced by an esterifi cation reaction between ethylene glycol and terephthalic acid. This is a twostage polymerisation process. In the fi rst stage, monomer-ester is produced and in the second stage, polymerisation takes place. Such a plant is shown in Figure 5.6.
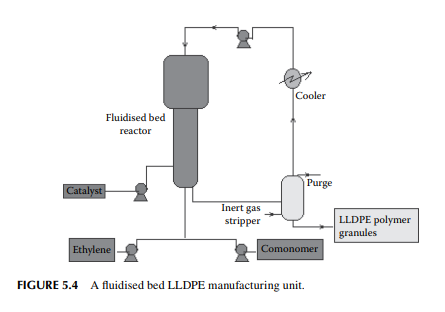
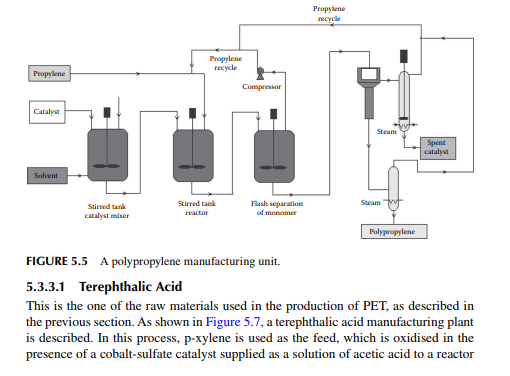
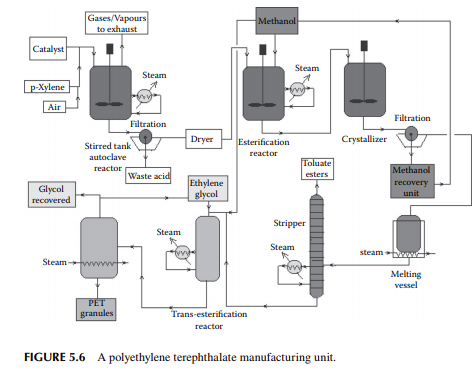
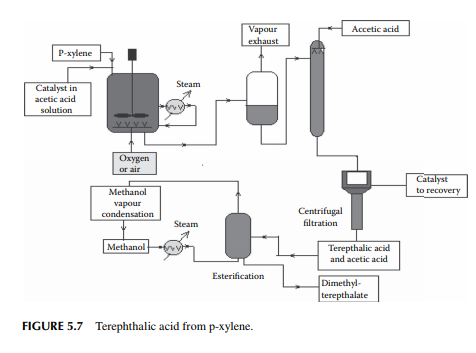
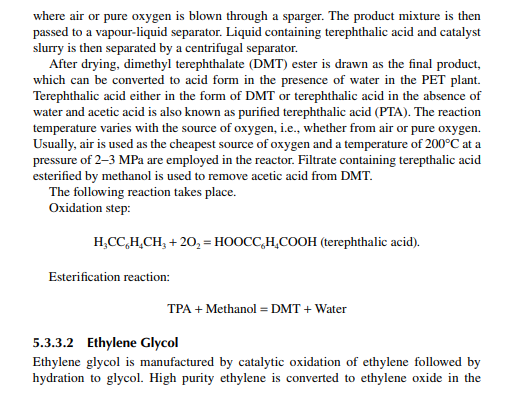
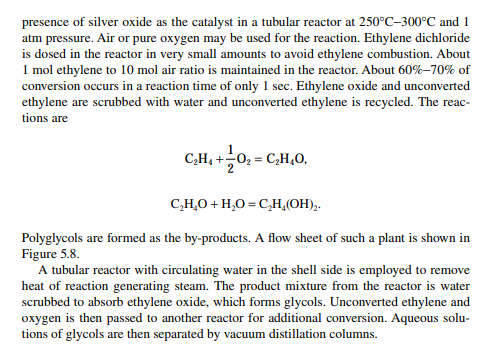
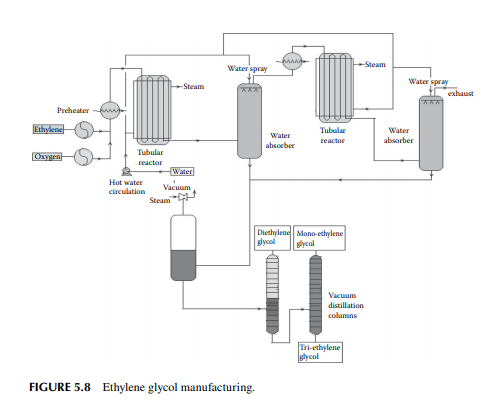
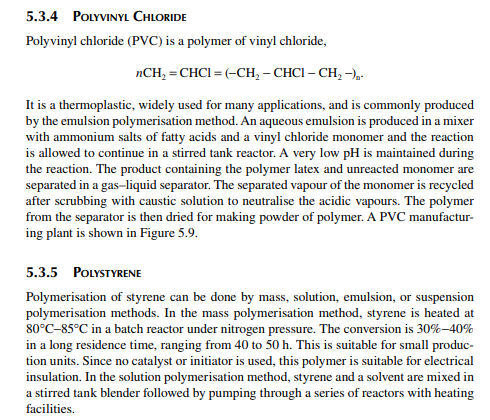
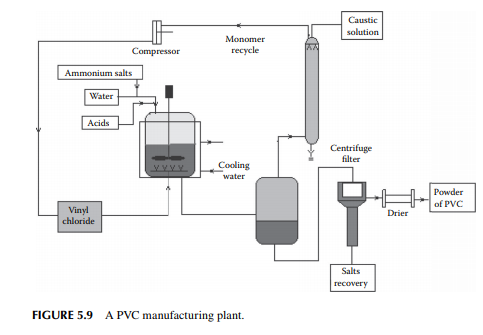
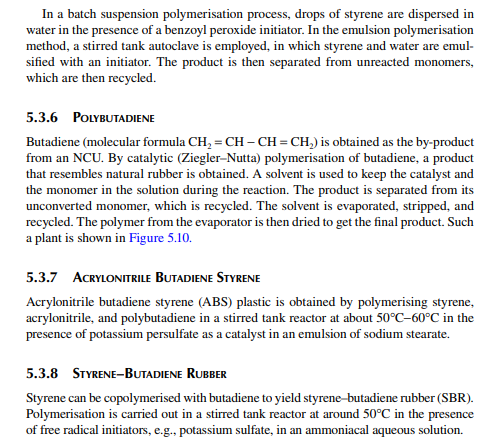
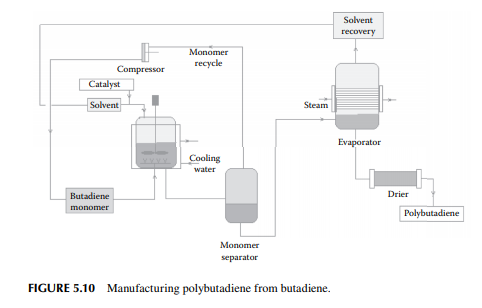
5.3.9 POLY METHYL METHA ACRYLATE
This is a polymer of the methyl metha acrylate monomer, which is produced from acrylonitrile (CH2CHCN) and sulfuric acid at a temperature below 90°C to yield methyl acrylate (CH2CONH2) followed by reacting with methanol to convert methyl acrylate to methyl metha acrylate (CH2CHCOOCH3). This methyl metha acrylate monomer is then polymerised in a stirred tank autoclave under nitrogen pressure. Any of the solution, emulsion, mass or suspension polymerisation methods are used.
5.3.10 POLYTETRAFLUOROETHYLENE
Polytetrafl uoroethylene (PTFE) or tefl on is a polymer of the tetrafl uoroethylene (C2F4) monomer. This monomer is prepared from methanol chlorination followed by fl uorination. The reactions are carried out in three reactors. Trichloromethane produced in the chlorinator is reacted with hydrofl uoric acid in the fi rst reactor at about 65°C in the presence of SbCl5 as the catalyst and is converted to produce mono-chloro-difl uoromethane (CHF2Cl) in the presence of AlCl3 as the catalyst in the second reactor. In the third reactor, CHF2Cl is then converted to C2F4 by catalytic pyrolysis at a temperature of 650°C−800°C in the presence of platinum (Pt) as the catalyst. Polymerisation of C2F4 is then carried out in a batch reactor preferably by the suspension polymerisation method at a temperature of 200°C and at a pressure of 1000 psi. The reaction time is about 1 h.
5.3.11 NYLONS
Polymers of amine or polyamides are excellent for making fi bres. These are well known as nylons. A list of a few nylons and their monomers are presented in Table 5.5. Condensation polymerisation is carried out with the monomer/monomers in autoclaves or stirred tank batch reactors. Nylon 6,6: This is produced by polymerising adipic acid [(CH2)4(COOH)2] and hexamethylene diamine [(CH2)6(NH2)2] in an autoclave in an aqueous solution at about 200°C and a pressure of 250 psi for a reaction time of 1−2 h. Such nylon-making steps are shown in Figure 5.11. Nylon 6: This is obtained from caprolactam [(CH2)5(CO)(NH)], which is polymerised in a water solution at about 250°C under nitrogen pressure in a batch autoclave. The reaction time is about 8−12 h
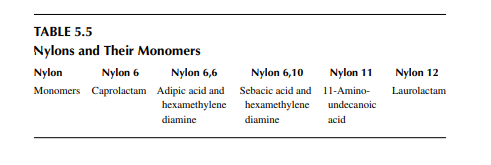
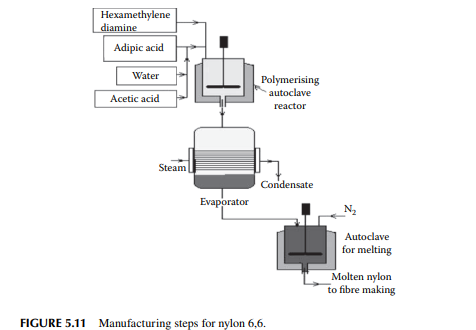
Nylon 6,10: This is produced from sebacic acid [(CH2)8(COOH)2] and hexamethylene diamine [(CH2)6(NH2)2], which are polymerised in a batch reactor where condensation takes place during the reaction. Nylon 11: This is obtained from 11-amino-undecanoic acid [(NH2)(CH2)10(COOH)], which is obtained from castor oil, by polymerising in an aqueous medium at a temperature of 220°C in an autoclave. Nylon 12: This nylon is a product of the polymerisation of laurolactam [(CH2)11(CO) (NH)] at a temperature of about 260°C in an autoclave. Monomers required for the manufacture of different varieties of nylons are either purchased or manufactured in their respective plants. Manufacturing processes for the monomers of nylons: Adipic acid: Commercial adipic acid is made from benzene. Benzene is catalytically hydrogenated to cyclohexane (C6H12) by Raney nickel as the catalyst at a temperature of 200°C−300°C under a hydrogen pressure of 3−4 MPa. The reaction takes place in a stirred tank reactor. Cyclohexane is then oxidised to a mixture of cyclohexanol (C6H11OH) and cyclohexanone (C6H10O) by cobalt naphthenate as the catalyst at a temperature of 145°C−175°C and at a pressure of 0.8−1 MPa in an oxygen atmosphere. Both the cyclohexanol and cyclohexanone are then further oxidised to adipic acid in the presence of copper and ammonium metavandate as the catalyst in the presence of nitric acid. The oxidation is carried out in a stirred tank reactor at a temperature of 60°C−80°C and atmospheric pressure. The reaction time is about
5−7 min. The product adipic acid [(CH2)4(COOH)2] is then further purifi ed by steam distillation.
Hexamethylene diamine: This is obtained from adipic acid in two stages. In the fi rst stage, adipic acid is converted to adiponitrile [(CH2)4(CN)2] by reacting with gaseous ammonia in the presence of the catalyst, boron phosphate, and at a temperature of about 340°C in a fi xed bed reactor. The product adiponitrile is then catalytically hydrogenated to hexamethylene diamine [(CH2)6(NH2)2] by a cobalt catalyst at a temperature of 100°C−135°C and at a hydrogen pressure of 60−65 MPa in a fi xed bed reactor.
Sebacic acid: This acid is commercially produced from castor oil saponifi cation with a caustic solution at about 250°C. In the reactor, the castor oil (glyceride) is split into ricinoleic acid [CH3(CH2)13CHOH(CH)2COOH] and glycerine [(CH2OH)2CHOH].
Ricinoleic acid is separated from glycerine and further heated in a separate reactor to yield sebacic acid [(CH2)8(COOH)2]. 11-Amino-undecanoic acid: This is also produced from castor oil. The oil is fi rst esterifi ed by methanol to yield methyl ester of recinolic acid, followed by pyrolysis at about 500°C. A mixture of products of heptyl alcohol, ester of undecylenic acid, heptaldehyde, etc., is obtained. Hydrolysis yields the undecylenic acid [CH(CH2)9COOH], which is then brominated by hydrobromic acid to bromo-undecanoic acid [CHBr(CH2)10COOH]. Treating bromo-undecanoic acid with ammonia yields 11-amino-undecanoic acid [NH2(CH2)10COOH].
Caprolactam: Benzene is converted to cyclohexane followed by oxidation to cyclohexanol and cyclohexanone, as described in the production of adipic acid. Cyclohexanol from the mixture is further catalytically dehydrogenated to cyclohexanone in the presence of zinc at a temperature of 400°C at 1 atm. The cyclohexanone is then converted to cyclohexanone oxime [C6H10NOH] by reacting with hydroxylamine sulfate [(NH2OH)2H2SO4] at about 18°C−25°C. Cyclohexanone oxime is then further treated with sulfur trioxide in the presence of sulfuric acid to yield caprolactum [(CH2)5(CO)(NH)] by a reaction mechanism known as the Beckmann rearrangement. The temperature of this reaction is maintained near 140°C−150°C. Laurolactam or dodecyl lactam: Butadiene is fi rst catalytically trimerised in a liquid phase reaction by the
Ziegler catalyst (TiCl4) in a stirred tank reactor. The product stream containing the desired trimer, 1,5,9-cyclo-dodecatriene, is separated from the by-products polybutadiene, cyclo-octadiene, and vinyl cyclohexene by distillation. This trimer is then catalytically hydrogenated using a nickel catalyst at 200°C and a hydrogen pressure of 1.4 MPa. The reaction is carried out in the liquid phase in a stirred tank autoclave. The hydrogenated product is cyclododecane [(CH2)12]. Cyclododecane is then oxidised in the liquid phase at about 150°C in jacketed stirred tank reactors in the presence of boric acid as the catalyst. The oxidised product stream, containing cyclododecanol [(CH2)11OH] and cyclododecanone [(CH2)10O], is
separated by distillation. Cyclododecanol is further dehydrogenated to yield cyclododecanone in a separate reactor at 200°C in the liquid phase and in the presence of a copper catalyst supported on alumina. Finally, cyclododecanone is oximated by hydroxylamine hydrogen sulfate [(NH2OH)2H2SO4] at a temperature of 100°C and converted to cyclododecanone oxime [(CH2)10NOH]. Finally, cyclododecanone oxime is converted to laurolactam [(CH2)11(CO)(NH)] ammonium sulfate and concentrated sulfuric acid. The Beckmann rearrangement reaction takes place during the formation of laurolactam. 5.3.12 PHENOL FORMALDEHYDE Phenol (C6H5OH) and formaldehyde (HCHO) in the presence of an aqueous ammoniacal medium condense to a phenol-formaldehyde resin. The reaction is carried out in a kettle-type reactor at a temperature of 160°C and at atmospheric pressure. The reaction time is less than 1 h. The product from the reactor is usually blended with hexamethylene triamine and other fi llers to make fi nished resins ready for moulding processes. Depending on the ratio of phenol to formaldehyde, a variety of grades of this resin may be made. This is a thermosettingtype resin.
5.3.13 UREA FORMALDEHYDE
Urea (CONH2)2 and formaldehyde (HCHO) also readily react to polymerise into urea-formaldehyde resin. Polymerisation is carried out in a glass-lined (or stainless steel) stirred tank reactor in an ammoniacal or weak alkaline medium. The polymerisation reaction takes place at room temperature and atmospheric pressure. This resin is also a thermosetting resin.
5.3.14 MELAMINE FORMALDEHYDE
Melamine [C3N3(NH2)3] and formaldehyde (HCHO) combine readily to form melamine-formaldehyde resin, which is also a thermosetting resin. The temperature of the reaction is 100°C in a neutral medium, i.e., at a pH of 7 in the aqueous medium at atmospheric pressure. Melamine formaldehyde resins are thermosets. Manufacturing steps for the monomers for formaldehyde resins: Formaldehyde: This is produced from methanol by catalytically oxidising over silver at about 620°C and a pressure of 30−70 kPa. Two reactions, oxidation and dehydrogenation, take place simultaneously, yielding formaldehyde in both reactions. In the catalytic oxidation, heat is generated and formaldehyde is formed. Due to heating, an endothermic dehydrogenation reaction takes place. Thus, the reactions become autothermal, both producing formaldehyde. The reactor is a water jacketed stainless steel vessel containing the catalyst. Methanol: Methanol is commercially manufactured from synthesis gas, i.e., from carbon monoxide and hydrogen. Catalytic hydrogenation of carbon monoxide is carried out over a copper-based catalyst at about 300°C and 2000−3000 MPa pressure to get a 50%−60% conversion. Methanol is usually manufactured in a fertiliser plant where synthesis gas is also used for manufacturing ammonia and urea.
Urea: This is manufactured by synthesising carbon dioxide and ammonia in a tubular reactor at a temperature of 180°C and 14 MPa without a catalyst (Stamicarbon process).
Melamine: Commercial melamine is produced from urea by high-pressure synthesis. Urea in the presence of ammonia pressure while undergoing dehydration yields melamine [C3N3(NH2)3]. In fact, methanol, urea, and melamine are available from fertiliser plants. Phenol: Phenol can be manufactured by a variety of methods, such as sulfonating benzene in the presence of caustic soda, chlorination of benzene followed by catalytic conversion to phenol, toluene oxidation, and cumene oxidation. A commercial cumene oxidation method is described in brief below.
Cumene: [C6H5CH(CH3)2] is fi rst manufactured from benzene and propylene in the presence of phosphoric acid in a fi xed bed reactor. The phosphoric acid is deposited on kieselguhr at a temperature of 190°C−200°C and a pressure of 3−4 MPa. Liquid hourly space velocity with respect to benzene is about 1.5. Cumene is then oxidised to cumyl hydroperoxide and acetone (by-product). The reaction is carried out in cylindrical steel columns agitated by blowing air through cumene in the alkaline solution as an emulsion containing soluble salts of heavy metals like Mn, Co, or Cu. A reaction temperature of 80°C−120°C and a pressure of air at 0.5−0.8 MPa are maintained in the reactor. The reaction time is about 1−2 h. The product stream containing cumyl hydroperoxide is separated from unconverted cumene, which is recycled. Cumyl hydroperoxide is then split into phenol and acetone in the presence of a catalyst, e.g., strong sulfonic acid or ion exchange resins, in a stirred tank reactor at a temperature of 70°C−80°C and a pressure of 0.1−0.2 MPa. Phenol is then purifi ed from by-products, e.g., acetone and methylstyrene, by distillation.
5.3.15 POLYURETHANE
These are thermosetting resins obtained by condensation polymerisation of polyol (diols or triols) and a diisocyanate. Examples of monomers are toluene diisocyanate [(CH3)(C6H4)(NCO)2] and dihydric alcohol or glycol [(CH2OH)2]. The polymerisation is carried out in a stirred tank autoclave reactor at a temperature of around 200°C under nitrogen pressure. Molten polymer is then taken directly to the fi bre spinning unit.
5.3.15.1 Toluene Diisocyanate
This is produced from toluene in three stages. In the fi rst stage, toluene is nitrated to dinitrotoluene; in the second stage, dinitrotoluene is reduced by catalytic
hydrogenation to toluene diamine; and in the third stage, toluene diamine is converted to toluene diisocyanate. In the fi rst stage, toluene is treated with a mixture of concentrated sulfuric acid and nitric acid in a series of agitated reactors at a temperature from 50°C to 65°C. In the second stage, nickel is used as the catalyst to hydrogenate the dinitrotoluene to diamine in a series of stirred tank reactors at a temperature of 170°C and a hydrogen pressure of 8−9 MPa. In the third stage, phosgene (COCl2) is treated with toluene diamine to produce toluene diisocianate. Phosgene is manufactured by chlorination of activated charcoal at a temperature of 50°C.
5.3.16 SILICONE
This is a polymer of siloxanes (R3SiO)3. Industrially, it is produced by alkylating with an organic halide, CH3Cl, or C6H5Cl with elemental silicon (Si) in the presence of a catalyst (Cu and CuO mixture) at about 200°C−300°C and at a pressure of 100−200 kPa for a long reaction time of about 48 h. The reactor is a cylindrical column fi tted with a screw-type agitator and a jacket. The di [(CH3)2SiCl2] and tri silanes [(CH3)3SiCl] produced are separated and hydrolysed separately, each at a temperature of 30°C−50°C to yield silicone polymers [(CH3)2SiO]n. The lower molecular weight polymers are oil, whereas the higher molecular weight polymers are solids. Silicon (Si) is obtained from silicon dioxide by a reduction reaction with carbon at about 1300°C in an arc furnace.
5.4 PETROCHEMICAL COMPLEX
Considering the multiplicity of raw materials, intermediates, and products, it may be necessary to build different large or small plants producing a limited number of products catering to the needs of other petrochemical manufacturing units or plants. In fact, the varieties of petrochemicals cannot be achieved from a single plant, but rather from a group of plants, each group being owned by the same or a different company. Such a group of plants is called a petrochemical complex.
5.4.1 DOWNSTREAM UNITS
Finished products from a petrochemical complex are utilised by a large number of manufacturers of domestic and industrial commodities, such as bottles, fi lms, ropes, garments, automotive parts, and paints.
5.4.2 PETROCHEMICALS’
HUB Since various petrochemical plants are needed to build a petrochemical complex, it is inevitable that feedstocks from the mother unit must be utilised by the intermediate manufacturers in a complimentary mission in a common framework of business procedures agreed by them. In order to maintain a healthy fl ow of fi nished and semi-fi nished products under a common umbrella of marketability
involving the downstream manufacturers of fi nished commodities, it is essential to accommodate all of the manufactures in a common area, a petrochemical hub. Such a holistic concept can reduce the considerable cost of storage, transportation, manufacturing, selling, and distribution, and the price of products. In such a hub, industries will be able to share facilities, such as power, transport, water supply, and civic amenities, which will ultimately help to promote sustainable industrial activities.
5.5 PROCESSING OF PLASTIC, RUBBER, AND FIBRE
Plastics, fi bres, and rubber are the major synthetic polymers. Plastics are also known as plastomer, which is characterised by a low moduli of elasticity of about 700−7000 kPa. However, elasticity varies with temperature. Plastics soften with an increase in temperature and because of this property, plastics are used for making furniture, ropes, fi lms, pipes, and a variety of domestic and industrial goods, which are used at low temperatures. Rubbers are polymers of lower elasticity with a moduli ranging from 70 to 700 kPa. They are also called elastomers. Hard rubbers are mainly used in making tyres for automobiles, aeroplanes, tractors, bikes, etc. Soft rubbers are used for lining furniture, sheets, bags, shoes, etc. Fibres are the polymers with the highest moduli of elasticity, ranging from 7,000 to 70,000 kPa. Fibres are used mainly as staple fi bres for making clothing. Thermoplastics are polymers that can be melted by heating and solidify after cooling repeatedly without any change in its plastic property. Plastics soften when heated, but there is a temperature at which the viscous liquid mass becomes like glass and brittle while it is cooled from molten state. This temperature is called the glass transition temperature. The higher the glass transition temperature, the more suitable the plastic is for use as it becomes brittle at or below this temperature. Hence, additives, known as placticisers, are mixed during the processing of plastics to increase this transition temperature. For instance, polyethylene has a glass transition temperature of −30°C or lower, whereas tefl on has a glass transition temperature at slightly above 100°C. A few examples of the glass transition temperatures of plastics are given below.
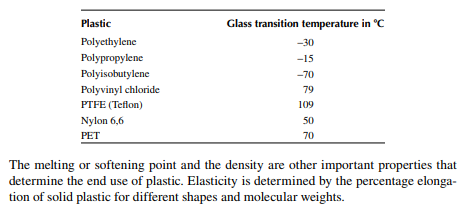
Thermosetting plastic softens when heated, and when cooled it does not return to its original soft stage, but hardens and cannot be remelted without damaging the original properties. Examples are phenol formaldehyde, urea formaldehyde, and melamine formaldehyde. Bakelite, which is used for making electrical switches and accessories, falls into this category. Thermosetting plastics are harder but more brittle than thermoplastics. These are cross-linked polymers and usually require reinforcement with other materials, such as glass fi bres, synthetic fi bres, cotton, and paper, to obtain the required toughness as engineering plastics. Phenol formaldehyde and urea formaldehyde are the most common thermosetting plastics. Basic raw polymer materials, e.g., powder or pellets of plastics, are obtained from the moulding processes as described in the next sections, which are then mixed with other additives and processed at high pressure, hot compression, blowing, etc., to yield the desired mechanical properties, size, and shape, depending on the type of end uses. Rubbers are softer materials as compared to plastics with very low elasticity and can be easily stretched longitudinally and restored to its original shape without distortion. Very low mechanical energy is required for such stretching and hence low elasticity. This property makes rubber suitable for making high-pressure tyres and tubes, pipes, balloons, membranes, balls, etc. A good quality tyre made from a basic polymer, such as polyisoprene, neoprene, and polybutadiene with additives, is capable of withstanding compression and expansion repeatedly. They are also good heat and electrical insulators. Mechanical operations like mixing process known as compounding of rubber necessary for desired properties of fi nished material. Natural rubbers from some plant origins, lacking in necessary mechanical strength, are also mixed with synthetic rubbers in the compounding process.
5.5.1 MOULDING OF PLASTICS
Molten matter can be poured into the cavities of templates or moulds of desired objects and cooled to the desired shapes. This process is called moulding, which is carried out in different ways, such as extrusion, injection, blowing, and compression, for making a variety of objects of different shapes, such as bottles, sheets, billets, fi bres, chairs, tables, tanks, doors, windows, and many products for domestic and industrial use.
5.5.2 EXTRUSION MOULDING
An extruder is a machine with a horizontal cylindrical barrel through which a shaft with a helical groove wound over. An electric heating coil is wound around the barrel for heating. Plastic powder is poured into the feed entry hopper at one end of the screw and it is then carried away by the helical groove and the annulus of the shaft and the barrel. The powder material softens due to heating and is forced out at the other end of the extruder. Finally, the softened plastic is forced through a die of desired object.
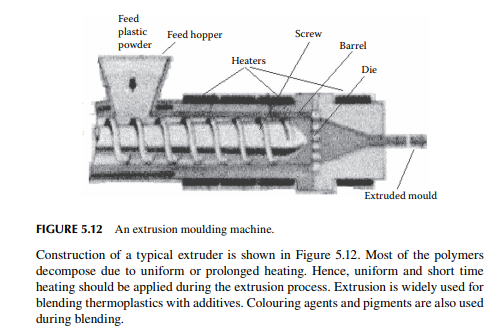
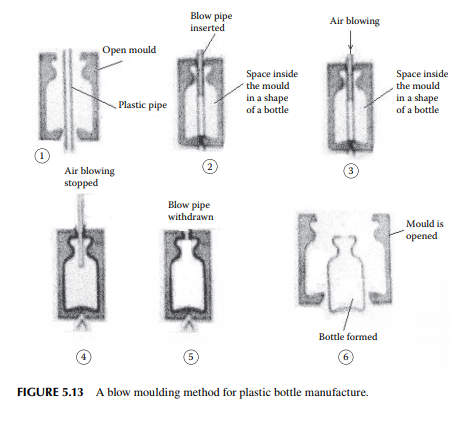
5.5.3 BLOW MOULDING
A blow moulding scheme is explained in Figure 5.13. In this method, hollow objects, such as bottles, pipes, and drums, are produced. At the start, preformed plastics by extrusion or injection are made and hot preform is then blown into a hollow mould and the desired shape is made. PE, polypropylene, and PET bottles are made by this method.
5.5.4 COMPRESSION MOULDING
In this method, two pieces of a mould are used to make the desired object. One of the pieces contains the raw plastic powder, while the other is punched at very high pressure to close the mould under heated conditions. Usually, thermosetting plastic materials of complicated shapes are made by this method.
5.5.5 THERMAL MOULDING
Thermal moulding is a process by which a preform of the plastic sheet of a desired thickness and weight is placed over a specially prepared mould or die with the provision of a vacuum suction and air pressurising system, as shown in Figure 5.14. At the beginning, the sheet is heated to a certain temperature and a vacuum is applied until the sheet takes the form of the contour of the internal space of the die. This is followed by cooling and the product is withdrawn by pushing with the air pressure of the vacuum suction and air pressurising system, as shown in Figure 5.15.
5.5.6 INJECTION MOULDING
In this method, a plunger (which is a thick solid cylindrical rod) drives the plastic in the heated groove of the die and brings back the perform in the return stroke
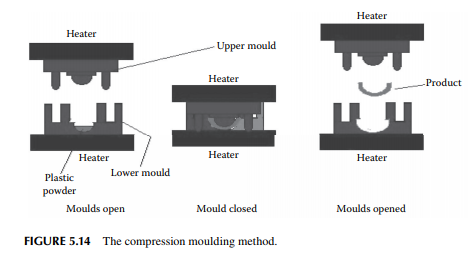
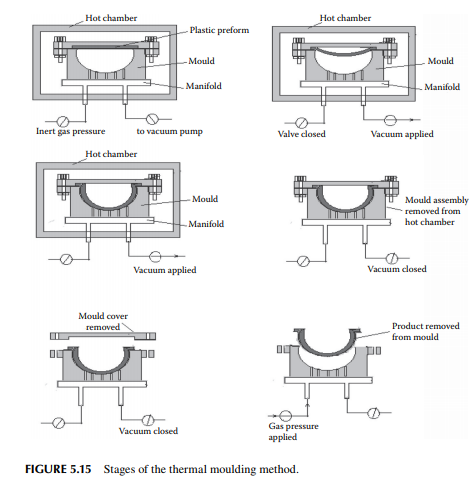
in a reciprocating motion. The entire process takes little time, thus a large number of preforms are produced by a single machine. Such a machine is shown in Figure 5.16. A large plant uses a number of injection moulding machines for the preforms followed by blow moulding for making bottles of various shapes and designs. These plants also supply preforms that are required by small plants, which do not have injection moulding facilities, to produce bottles and other materials.
5.5.7 RUBBER COMPOUNDING
Rubber is used for making tyres, belts, and many domestic and industrial products. Finished rubber is a mixture of polymers with additives, such as graphitic carbon, sulfur, lubricants, and certain metallic oxides, to impart good elasticity, mechanical strength, abrasive resistance, and other properties that should be retained for long use especially for making tyres. Polymer structure of rubber can be changed by reacting with sulfur during vulcanization and properties of rubber
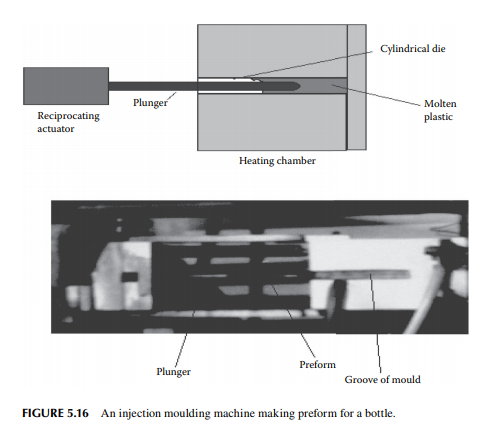
can be changed as desired by the manufacturer. The process of treating rubber polymer with sulfur is called vulcanisation. Rubber is applied for making coated (calendering) materials, which are moulded or extruded to make a variety of products. Rubber generated or available as scraps are also reused by the reclaiming process and converted back to fi nished rubber, known as reclaimed rubber. Highpressure and high-speed mixers, like a two-roll mill or Banbury mixer, are commonly employed for mixing rubber components. The clearance between the rolls (or the stator-rotor in a Banbury mixer) is extremely small to help intense mixing at high pressure. A Banbury mixer is shown in Figure 5.17.
QUESTIONS
1. Compare the advantages and disadvantages of ethane cracking and naphtha cracking for ethylene manufacture.
2. Distinguish between synthetic plastic, rubber, and fi bre.
3. What are the various methods for polyethylene manufacture?
4. What are the raw materials used for the manufacture of polyethylene terephthalate?
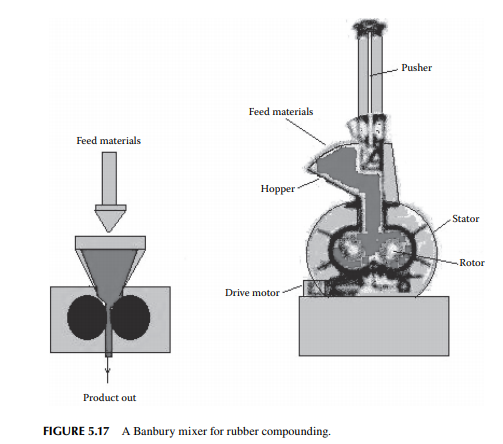
5. What are the various types of nylons available? Mention the method of manufacture of nylon 6,6.
6. What are the various types of moulding methods used for plastic goods? What is a preform?
7. What do you understand by vulcanisation of rubber?