4.1 COMPONENTS OF FINISHED LUBRICATING OILS
The use of animal fats to reduce friction and wear and tear of mechanical parts has been the practice from time immemorial. However, since the availability of petroleum sources, lubricants are now manufactured using petroleum stocks. Today’s lubricating oil is mainly composed of base hydrocarbon oil, lubricating base oil stock (LOBS), obtained from vacuum distillates after treatment in the refi nery, as discussed in Chapter 3, with some additives to meet the requirements for its end use. Synthetic base oils, such as polyalphaolefi ns, alkylated aromatics, polybutenes, and aliphatic diesters, are also used as base oils. The following additives are blended with the base oil.
Detergents: These are surfactants to cleanse the harmful carbon and sludge deposits on the surface of the metals in contact.
Sodium or calcium sulfonates or organic sulfonates are excellent detergent agents in lube oils. Dispersants: These are used to disperse the oil-insoluble products of oxidation and other formations in the oil phase and does not allow these to deposit on the metallic surfaces of bearing or rolling or sliding metals. Examples of dispersants are succinimides, esters of
polysuccinic acid or succinate ester, and hydroxyethyl imide. Antioxidants and stabilisers: These agents prevent auto-oxidation of hydrocarbon base oils present in the lubricant. This chemical reaction is in three stages: initiation, propagation, and termination, similar to a polymerisation reaction forming resinous layers. Copper soaps are an excellent retardant of such auto-oxidation. Aromatic amines and phenols are examples of antioxidants.
Viscosity index improvers: Polymethacrylates and polyisobutylene are excellent viscosity index (VI) improvers. These agents keep the viscosity of oil nearly unchanged over a wide range of temperature fl uctuations.
Friction modifi ers: These agents modify the coeffi cient of friction by adhering to the metallic surface. Examples are amines, amides, their derivatives, carboxylic acids, phosphoric acids and their salts. Pour point depressants:
Polymethacrylates, polyacrylates, and di-tetra paraffi n-phenol-phthalate act as the pour point suppressants.
Demulsifi ers: Acidic gases, moisture, carbon particles and other products may form at high temperatures, especially in engines, and form an emulsion with the lubricant oils. Sulfonates, alkylated phenolic resins, polyethylene oxide, etc., are good demulsifi ers.
Anti-foaming agents: Gases and moisture are responsible for foam formation with the lubricating oil. The most widely used anti-foaming agent is polydimethylsiloxane. Corrosion inhibitors: Ingress of oxygen and the presence of moisture cause oxide corrosion, and acidic chemicals and mercaptans may cause chemical corrosion aided by high temperatures. Esters or amides of dodycyl-succinic acid, thiophosphates, etc., act as corrosion inhibitors.
Anti-oxidants also prevent oxide corrosion. Thickeners: Sodium or calcium soaps act as thickeners, which are required to retain the fi lm of lubricant over the metallic surfaces in contact and do not allow the metallic surfaces to come in direct contact without the lubricant fi lm within them. A variety of lubricants are used depending on the type of application, such as automobiles, aircraft, ships, and engines. These are broadly classifi ed as automotive lubricants, aviation lubricants, industrial lubricants, marine lubricants, etc. Under this broad classifi cation, they are further classifi ed as engine oil, gear oil, bearing oil, hydraulic oil or transmission oil, cylinder oil, etc., depending on the fi eld of application. Lubricants used in marine diesel engines are presented in Table 4.4.
4.2 AUTOMOTIVE OILS
The majority of automobiles include vehicles run on motor spirit (petrol) or diesel. Different lubricants are used for petrol engines (which are spark ignition type) and diesel engines (which are compression ignition type). These are known as engine oils, which are suitable for use in high temperatures and the oxidising environment of engines. Load (weight to carry) and speed of the vehicles are also to be taken care of before selecting a lube oil to apply. Usually, the temperature of an engine rises rapidly during the start up and continues at that temperature during motion. Such a wide and sudden change in temperature demands that the lubricant should have a high VI. In addition to temperature fl uctuations, lubricants are prone to oxidation and cracking, leading to the formation of cokes, carbons, and gummy substances, which may ultimately deposit on the engine, causing irreparable damage. In addition to engine oils, different lubricants are applicable for other parts of the vehicle, such as the gears, brake, clutch, and bearings. Gear boxes contain the gears immersed in lubricating oil having low viscosity to reduce friction at high speed. The brake and clutch require lubricating oils of low viscosity. Bearings are used in various parts of the automobile from engine to wheels, and require low to high viscous lubricants. At low temperatures and high load, bearings at wheels are lubricated by grease. Since materials of construction and type of engines vary with the make, appropriate lubricants are selected and prescribed by the manufacturers. No single lubricant is therefore applicable for all makes. Finished lubes are classifi ed according to the Society
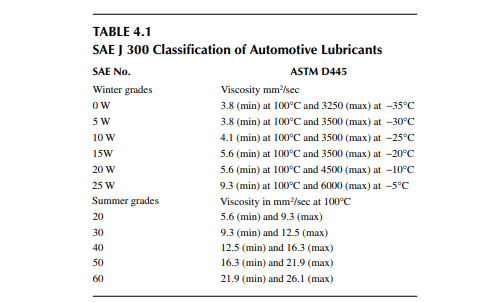
of Automotive Engineers’ (SAE) numbers as given in Table 4.1. The viscosity of the lubricants and its variation with temperature (VI) and the pour point are the important parameters to satisfy the compatibility of application of lubes. Winter grades are classifi ed as SAE numbers from 0 to 25W as typical examples of cold temperatures and from 20 to 60 SAE numbers for warming up the cranks of engines. A multigrade lubricant is a blend of more than one type of lubricant. For example, SAE15W 50 is an example of a blend of two grade oils. Usually, polymeric materials, such as ethylene–propylene copolymer, polymethyl acrylate, and butadiene, are added to these multigrade oils. However, rigorous testing of appropriate lubes must be carried out on cars of different makes in the testing laboratory or workshop for their suitability before prescribing them for engines and other parts. Since the performance of these lubes may not be satisfactory after a certain period of time due to degradation because of contamination, reaction, physical and chemical changes in the property of the ingredients or the base oils, it is inevitable that the lube must be drained out and replaced with fresh stock. This drain out period must be specifi ed for the prescribed lubricants. The longer the drain out period, the more attractive the lubricant is in the market.
4.3 INDUSTRIAL LUBRICANTS
Industries use a large amount of lubricants, known as industrial oils, i.e., transmission oils, turbine oils, compressor oils, seal oils, cooling oils, gear oils, bearing oils, hydraulic oils, and cutting oils.
4.3.1 BEARING LUBRICANTS
Bearings used in machineries face either sliding or rolling frictions. Usually, greases or solid lubricants are used to lubricate the small bearing surfaces. Lithium greases
or graphite are the common lubricants. However, a solid polymeric lubricant, such as polytetrafl ouroethylene (PTFE), coating of the sliding bearing surfaces may be used for low load friction. These are popularly known as non-lubricated or self-lubricated bearings. Circulating lubricating oils are commonly employed for bearings of high load and speed where lubricating oil not only reduces friction but also cools the bearing surfaces. For this lubrication system, a thin oil layer between the bearing surfaces must be maintained by high pressure circulating pumps. Gaseous lubricants, such as air, nitrogen, oxygen, and helium, are used in the bearings of aeroplanes and aircrafts. A gaseous lubricant has the advantage that the chemical properties of gas do not change with temperature. At high temperatures, the viscosity of gas increases and, as a result, a gaseous lubricant is preferred over liquid lubricants in high load bearings in aerodynamic applications. Liquid or gaseous lubricants or grease are not applicable for bearings used under vacuum and at very high temperatures when radiation is appreciable. In this case, solid lubricants are used in the bearings. Molybdenum disulfi de, graphite, boron nitride, and cadmium iodide powders are used as the lubricants. PTFE rings or lining over the bearing surfaces are also used to lubricate the bearing surfaces. Initially, these solids are not lubricating in nature, but with the heat of friction the lubricating property is manifested.
4.3.2 HYDRAULIC LUBRICANTS
Hydraulic fl uids are viscous liquids used in power transmission for control, braking in automobiles and machineries, raising or lowering loads by multiplying the transmitted force, and so on. In addition to these activities, hydraulic fl uids lubricate the mating parts of machines and are used in a wide variety of environments, such as air, water, gaseous, and high and low temperatures. These fl uids are practically non-volatile in the temperature of use. These fl uids are mostly high viscous, high VI, petroleum-based oil with or without additives. Synthetic oils, such as esters of polyglycols, phosphoric acid, and silicones, are also used as hydraulic fl uids. It is desirable that all hydraulic lubricants should also have a high fl ash point and be fl ameproof.
4.3.3 COMPRESSOR LUBRICANTS
Gases are compressed either in reciprocating or centrifugal compressors. In the reciprocating compressor, the piston and cylinder is lubricated by lubricating oil, which must have a low vapour pressure and a low carbon-forming tendency. Lube vapour, especially petroleum base oil and carbon particles, may contaminate the compressed gas and lead to explosion. Modern reciprocating compressors are lubricated by PTFE polymer rings and lining. For natural gas or refi nery gas compressors, polyalkylene glycols are used. For centrifugal compressors, solid lubricants or polymeric synthetic oils are used.
4.3.4 PUMP LUBRICANTS
Small water pumps are lubricated by grease in the bearing, but large pumps are lubricated by liquid lubricants either using the gravity falling cup method or by
separate circulation using gear or screw pumps. Modern pumps use solid lubricants, like graphite, or polymeric material, like PTFE. Miscellaneous industrial lubricants, such as transformer oils, cutting oils, and sealing oils, are used, and the specifi cation of each is defi ned by the user industries. The varieties of industrial grade lubricants are classifi ed as viscosity grades according to ISO 3448 standard, and are presented in Table 4.2.
4.4 AVIATION LUBRICANTS
Some of the major factors determining the selection of lubricants for the engines and bearings of aerodynamic vehicles are air temperature and pressure at various altitudes, type of engines and turbines, load and speed, etc. Air temperature may be as low as −80°C at the highest altitude or as high as +40°C on the ground. Pressure may vary from 1 atm on the ground, falling with an increase in altitude. The engines may be reciprocating or rotary types. Previously, very pure petroleum base oils or castor oil were used without any additives. Now, in the modern turbine-type engines, multigrade oils are being used. The typical specifi cations of reciprocating and turbine engines oils are presented in Tables 4.3A and 4.3B.
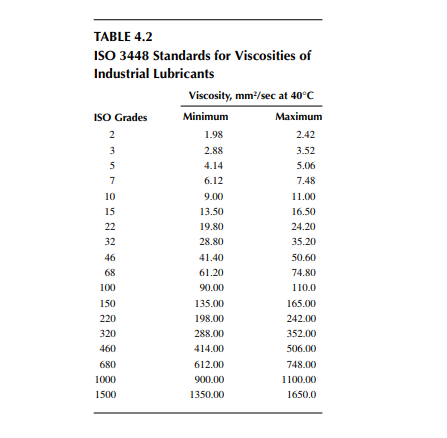
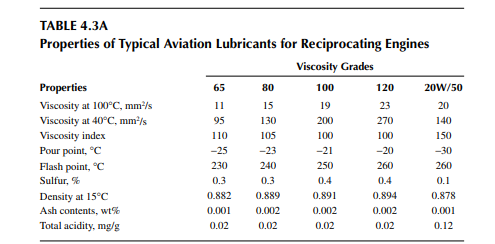
4.5 MARINE LUBRICANTS
Marine craft, such as barges, speed boats, small ships, tankers, big ships, and submarines, are run on a variety of fuels, e.g., high speed diesel, light diesel oil (LDO), and residual fuel oil (FO). Small vehicles run directly on fuels using reciprocating engines and bigger vehicles use turbines. Modern cargo ships and crude tankers are run on electricity empowered by their own power plant fuelled by furnace oil or LDO. Hence, the requirements of lubricants vary with the types of vehicles. Large vehicles use lubricants for motors, for reciprocating or turbine engines, bearings, and industrial lubricants wherever applicable. Lubricants used in marine diesel engines are presented in Table 4.4.
4.6 GREASES
Grease is thickened oil containing the base oil and thickening additives. The mineral base oil must meet many different requirements, e.g., viscosity, VI, and oxidation stability, such as that required for making lubricating oil. But the other important properties for base oil required for grease making are the viscosity-gravity-constant (VGC), the aniline point, carbon type, and solubilising property. The thickeners are
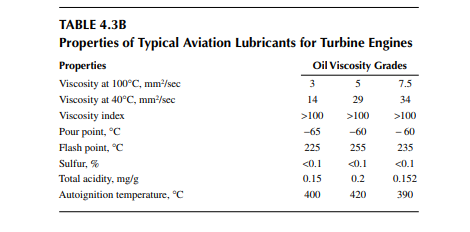
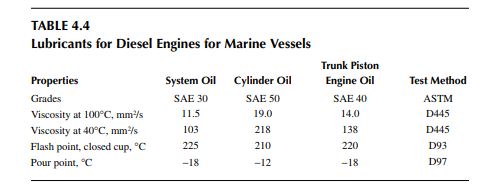
the sodium, calcium, or lithium soaps of fatty acids. Greases are popularly classifi ed according to the type of thickeners used. The melting point and the water content of the soaps are important parameters. Sodium soaps (melt at 150°C) are preferred over calcium soaps (melt at 100°C) for their higher melting point. The evaporation of water present in these soaps limits their use much below their melting points. Lithium-12 hydroxystearate soap is an excellent thickener for grease making. This grease is able to maintain its properties at high temperatures without losing its lubricating property up to 140°C along with excellent resistance to mechanical deformation and immunity to the presence of water in the fi eld of application. Modern grease employs a mixture of calcium–lithium and aluminium–barium soaps. A major thickener in the grease industry is lithium 12-hydroxystearate, a soap of 12-hydroxystearic acid, obtained from vegetable oils and animal fats. In place of metallic soaps, thickening agents, such as clays, PTFE powder, and graphite, are also used in grease. But these require frequent replacement of grease to maintain uniform lubricity. Most modern greases also include some additives to modify the property of the grease to suit different environments of applications. These are antioxidants, corrosion inhibitors, anti-wear, extreme pressure additives, adhesives, etc. Grease behaves as non-Newtonian fl uids and the majority usually manifest as Bingham plastics. The consistency index or apparent viscosity is measured for grease. Apparent viscosity is measured as per the ASTM D1092 method and consistency is measured by cone penetration index as per the ASTM D1403 method. A worked grease sample, obtained through a grease worker, which is a cylindrical vessel equipped with a piston with holes, is prepared before testing for cone penetration. Standard working is done by forcing the piston back and forth 60 times in 60 sec. The penetration index is measured at 25°C. In addition to these, the drop point is also determined according to the ASTM D556 method. Grease specifi cation is classifi ed according to the National Lubricating Grease Institute (NLGI). The properties and uses of typical greases are presented in Table 4.5.
4.7 LUBE BLENDING AND GREASE MANUFACTURE
Lube blending is the intelligent art of mixing various ingredients with the lube base stock, satisfying the desired physical, chemical, transport and mechanical properties,
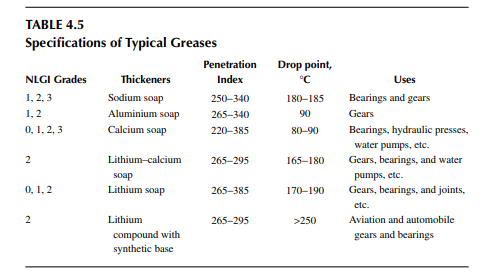
usually known as tribological properties. The blending units consist of kettles with steam or electric heating facilities where the additives are mixed while continuously monitoring the desired properties. Additives, such as anti-wear, antioxidant, anti-rust, anti-foam, and corrosion inhibitors, are given in small quantities and are procured from various sources. Usually lube blending and grease making are carried out in the same plant where large amounts of soaps of fatty oils are blended for grease and hence a saponifi cation unit is part and parcel of a blending plant. A schematic general lube blending plant is shown in Figure 4.1a and a typical calcium grease making plant is presented in Figure 4.1b, where calcium soap is prepared from metered amounts of lime slurry and vegetable oil at the desirable operating temperature and oil/lime ratio in a continuous stirred steam-heated tank or a kettle heater. Modern plants use electric heating in the kettles. A number of kettles may be used to increase the production rate. Fats or vegetable oil are saponifi ed and a soap mixture is pumped to a special type of kettle, known as a Lancaster mixer, where the base oil (usually petroleum base) is mixed at a high speed of about 3000−4000 rpm and at a temperature of 170°C−180°C. In fact, the operating temperature and time of mixing are monitored for the desired consistency of the grease. The effl uent from the kettle is then fi ltered to remove sludge and particulates from the liquid grease before storage or continuous packaging.
4.8 ENVIRONMENTAL IMPACT OF LUBRICANTS
Since it is necessary to replace the lubricating oil and grease after some days or weeks or even after a few months, these must be disposed off. In many applications, such as in two-stroke engines, railways, chains, and in rubber tyres, lubricants are continuously lost to the atmosphere. Most of these losses are due to inappropriate maintenance and leakages, which cause enormous pollution and lead to accidents and fi re. Direct draining and disposal in a landfi ll are also common, leading to pollution. Recycling
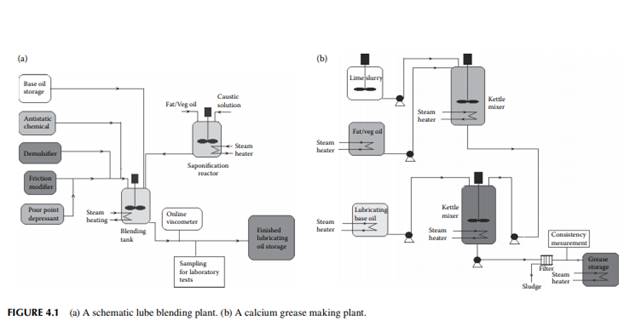
is a good practice but costly. It was reported that about half of the lubricants sold in the market are consumed and the remaining half is either recycled or burnt as fuels. The presence of petroleum base stocks and some metal contents are not biodegradable and contamination in water and land may lead to poisonous effects on the aquatic culture and plantation. Polycyclic hydrocarbons (PCH) present in petroleum base oils are potential carcinogens, too. Hence, modern day lubricants are being developed from vegetable or natural base oils rather than from mineral base oils. Vegetable or natural oilbased lubricants are bio-degradable and can be disposed off after biological treatment or as land fi ll or fertiliser.
4.9 RECLAMATION OF USED LUBRICANTS
As far as the volume of lubricants and grease used and replaced is concerned, recycling of used lubricants after treatment is a standard and economic practice in many countries. There are a variety of reclamation technologies for used lubricants, depending on the quality and quantity of availability. Used lubricants are usually available as a mixture of base oils, additives, and contaminants, such as water, metallic scales, rusts, and inorganic salts. These can be ascertained by bottom sediment and water (BSW) analysis, like crude oil. Hence, the primary treatment involves removal of inorganic matters. The acid-clay process is the oldest and dominant process of re-refi ning of used lubricants. In this process, after dewatering and desalting of the feedstock, acid is mixed in a stirred vessel. Sludges and oily layers are separated in a settler. Excess acid in the oil mass is then neutralised with a caustic solution and the oily mass is then further clay treated, which is then subject to vacuum distillation. A variety of base oils may be obtained from the distillation step, depending on the quality of the used lubricant feedstock. Acid is recovered from sludges and neutralised with a caustic solution before disposal. The propane deasphalting method is also applied for highly viscous industrial lubricants to recover the base oil and organic matters. Catalytic hydrogenation for desulfurisation, stabilisation of unsaturates, and discoloration may follow for the recovered base oils. The recovery of inorganic additives may not be economically feasible in any of the processes. Recovered base oils are then fed back to the blending plants or sold as FO.
Example 4.1
Calcium stearate soap as a thickener is prepared from fat (mutton tallow) and calcium hydroxide. Determine the amount of lime and fat required to produce 100 tons of soap lye per day in a continuous saponifi cation reactor. Assume that stearic acid content in the tallow is about 30% by weight, purity of lime is 80% by weight, and saponifi cation reaction is 45% complete by weight.
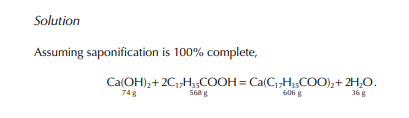
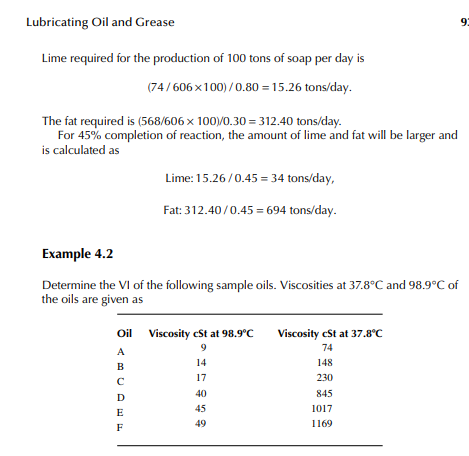
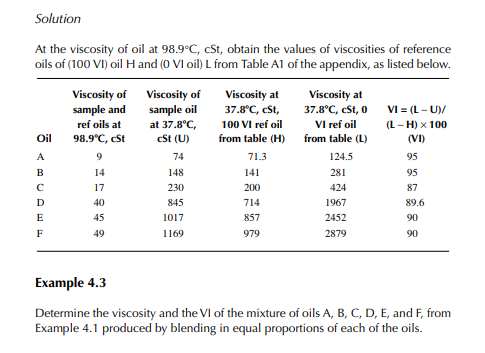
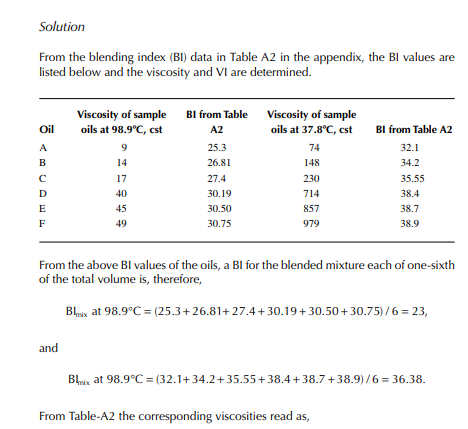
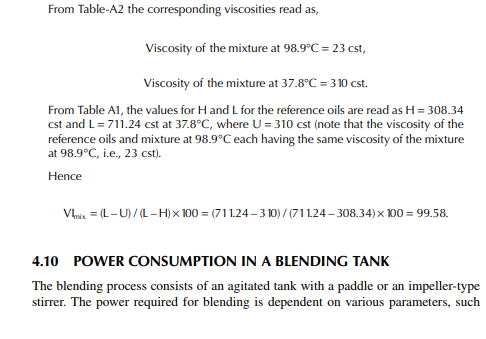
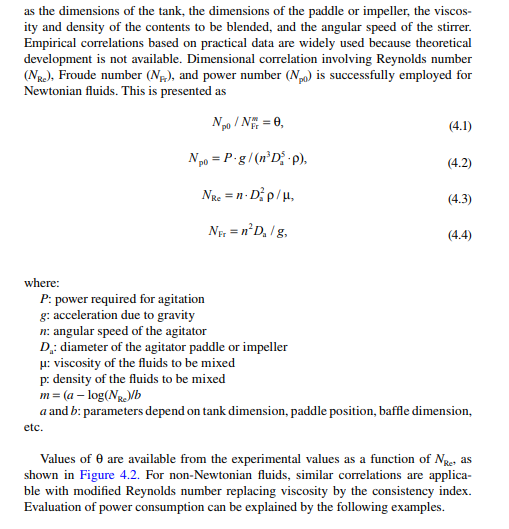
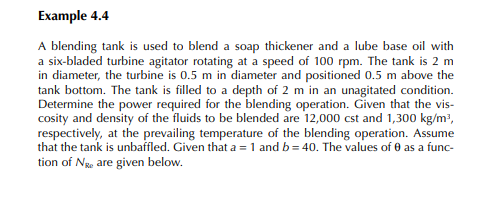
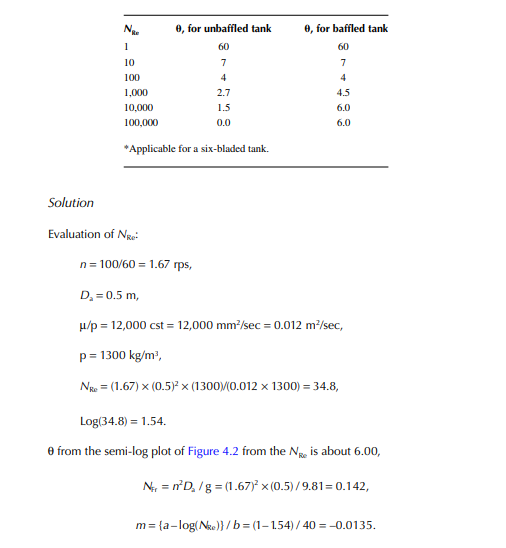
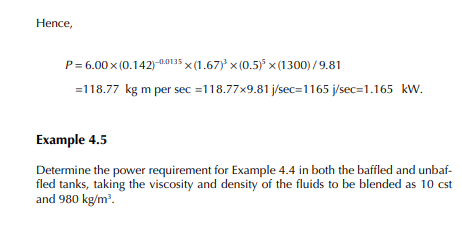
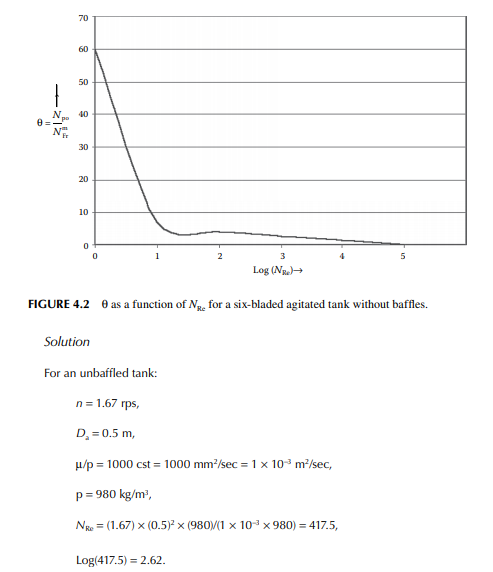
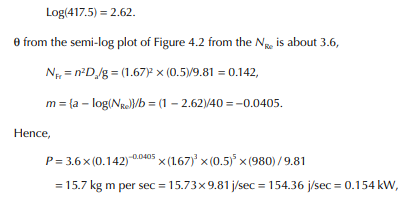
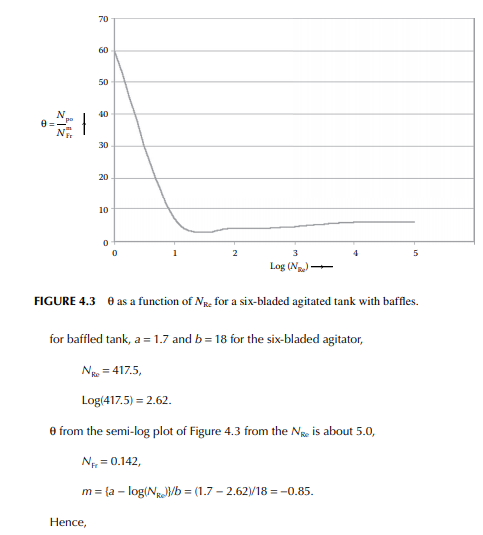
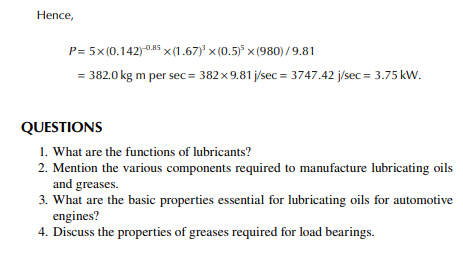
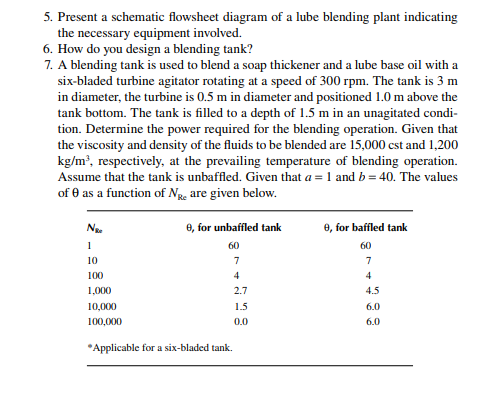