Keys are very useful and inexpensive locking devices for transmission shafts. The problems of key shear stress in shafts and their impacts on transmission system are described below.
· Keys are used to connect the shaft to the rotating machine elements such as the hub, gear, socket, flywheel, and pulley. They are responsible for maintaining the accurate position of the shaft and the rotating element of the machine. A keyway is provided in the shaft to attach the key.
Some undesired problems occur in keys during the rotation of the shaft. The major shaft with key shear stress problems are the failure of keys and backlash due to the stress introduced during rotation. Because of them, there starts relative rotational motion between the connected elements that causes loss of torque and thereby loss in efficiency of the system. It is a necessity to understand these problems so as to avoid any energy loss.
The Function of Keys
There are two main functions of keys when they are used to lock the transmission shaft.
· The primary function is to transfer torque from the rotating shaft to the rotary element of the machine. The same key works to transmit torque in both direction; from shaft to the machine element, or from machine element to the shaft.
· The second function of the key is to restrict relative rotational motion and axial movement between the shaft and the machine element. Some special types of keys are also available, such as feather and splines, keys that allow axial movement between them.
Failure of the Shaft Key
The force imposed due to the rotation of the shaft causes the failure of the keys. There are two types of key failures.
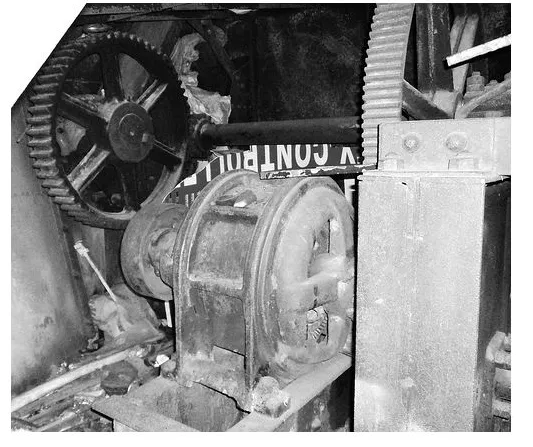
Shear Failure of Keys
As the term indicates, shear stress is the cause of this type of key failure. Actually, during rotation the shaft and the machine element, say hub, each element exerts equal and opposite force on the key. These opposite forces introduce shear stress along the radius of the shaft. The key is then starts deforming and after some time it fails.
The ultimate stress depends on the material strength of the key and angular velocity of the rotation. You can calculate the shear force applied on the key using the formula given below.
· F = π ω l
· T = Fr
Where,
F= the shear stress acting on the key,
·
· L= effective length of the key,
ω= angular velocity of the shaft,
r= radius of the shaft, and
T= maximum torque transferred by the key.
Crushing Failure of Key
Crushing of a key is the reason of this type of key failure. During rotation the shaft and the hub impose compressive force on the key. This compressive force causes its deformation. The key is then permanently deformed under this force and finally crushing occurs.
This compressive force can be calculated using the parameters of the shaft and the key. The formula for the calculation is given below.
· F = πH/2
· T = Fr
Where all elements are the saem as above and H is the height of the key.
Backlash in Key
Backlash occurs when key is not properly fixed in the keyway. The forces applied on the key by the shaft and hub during rotation may change the parameters of the keyway. Due to increased size the keyway starts allowing the key to move and this movement causes backlash.
Two types of movement occur between key and keyway. First is sliding of the key without twisting and the second is twisting of the key without sliding. The backlash is denoted by backlash angle α, and
α=180b / rπ
Where, b is the arc length.
Backlash must be minimized to get best performance. The backlash becomes larger and large as time passes. The complete elimination of backlash is impossible; however, precise fitting and accurate machining mating components can reduce backlash to a great extent.
Backlash increases due to the following reasons:
· The loading and unloading in the machine, frequently.
· Change in angular acceleration with a high rate.
· Applying high impacts between key and keyway, repeatedly.
Summary
Dynamic loading is an important cause of key failure and backlash. However, if we use keyless frictional type connections between shaft and hub then we can eliminate most of these problems. An example of keyless frictional type connection is using a shrink disk that offers zero backlash to the system.
A shaft with key shear stress problems can be found very easily in all torque transmission systems and luckily key replacement is not very expensive. Inspecting the key regularly will result in catching a failure sooner and allow your production to stay on schedule. Even if a failure is not imminent you may discover oxidation or part welding during your inspection.