An automated or automatic guided vehicle system (AGVS) is a materials handling system that uses independently operated, self-propelled vehicles that are guided along defined pathways in the floor. The vehicles are powered by means of on-board batteries that allow operation for several hours (8 to 16 hours is typical) between recharging. The definition of the pathways is generally accomplished using wires embedded in the floor or reflective paint on the floor surface. Guidance is achieved by sensors on the vehicles that can follow the guide wires or paint.
Automated guided vehicles (AGVs) increase efficiency and reduce costs by helping to automate a manufacturing facility or warehouse.
AGVS can carry loads or tow objects behind them in trailers to which they can autonomously attach. The trailers can be used to move raw materials or finished product. The AGV can also store objects on a bed. The objects can be placed on a set of motorized rollers (conveyor) and then pushed off by reversing them. Some AGVs use forklifts to lift objects for storage. AGVs are employed in nearly every industry, including, pulp, paper, metals, newspaper, and general manufacturing. Transporting materials such as food, linen or medicine in hospitals is also done.
There are a number of different types of AGVS all of which operate according to the preceding description. The types can be classified as follows:
Driverless trains:
This type consists of a towing vehicle (which is the AGV) that pulls one or more trailers to form a train. It was the first type of AGVS to be introduced and is still popular. It is useful in applications where heavy payloads must be moved large distances in warehouses or factories with intermediate pickup and drop-off points along the route. Figure 17 illustrates the driverless strain AGVS.
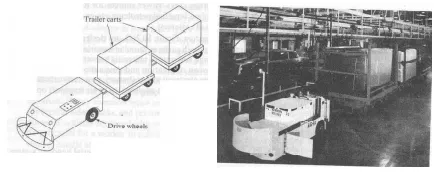
Driverless trains
AGVS pallet trucks:
Automated guided pallet trucks are used to move palletized loads along predetermined routes. In the typical application the vehicle is backed into the loaded pallet by a human worker who steers the truck and uses its forks to elevate the load slightly. Then the worker drives the pallet truck to the guidepatn, programs its destination, and the vehicle proceeds automatically to the destination for unloading. The capacity of an AGVS pallet truck ranges up to 6000 Ib, and some trucks are capable of handling two pallets rather than one. A more recent introduction related to the pallet truck is the forklift AGV. This vehicle can achieve significant vertical movement of its forks to reach loads on shelves. Figure18 illustrates this vehicle type.
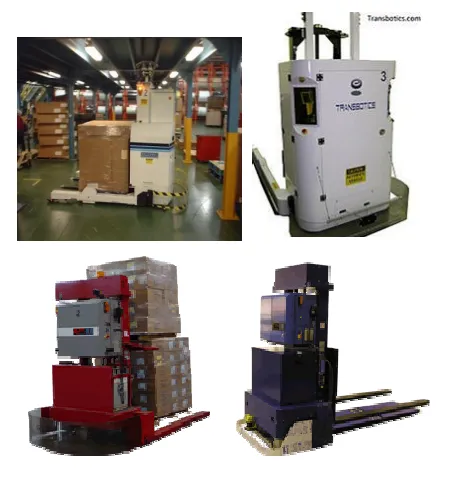
AGV pallet trucks
AGVS unit load carriers.
This type of AGVS is used to move unit loads from one station to another station. They are often equipped for automatic loading and unloading by means of powered rollers, moving belts, mechanized lift platforms, or other devices. The unit load carrier is pictured in Figure 20. Variations of the unit load carrier include light-load AGVs and assembly line AGVs. The light-load AGV is a relatively small vehicle with a corresponding load capacity (typically 500 Ib or less). It does not require the same large aisle width as the conventional AGV. Light-load guided vehicles are designed to move small toads (single parts, small baskets or tote pans of parts, etc.) through plants of limited size engaged in light manufacturing. The assembly line AGVS is designed to carry a partially completed subassembly through a sequence of assembly workstations to build the product.
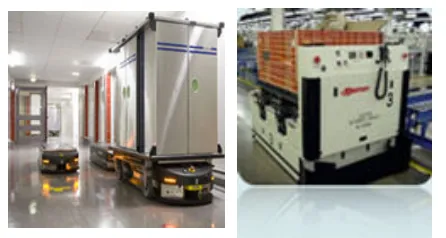
AGV unit load carrier