For any of the three types of production, there are certain basic functions that must be carried out to convert raw materials into finished product. For a firm engaged in making discrete products, the functions are:
1. Processing
2. Assembly
3. Material handling and storage
4. Inspection and test
5. Control
The first four of these functions are the physical activities that “touch” the product as it is being made. Processing and assembly are operations that add value to the product. The third and fourth functions must be performed in a manufacturing plant, but they do not add value to the product. The Figure 6 shows the model of the functions of manufacturing in factory .
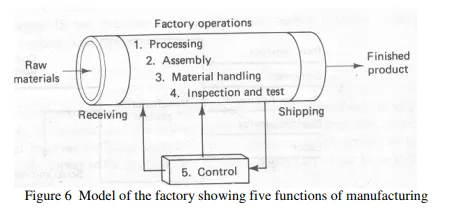
Processing operations
Processing operations transform the product from one state of completion into a more advanced state of completion. Processing operations can be classified into one of the following four categories:
1. Basic processes
2. Secondary processes
3. Operations to enhance physical properties
4. Finishing operations
Basic processes are those which give the work material its initial form. Metal casting and plastic molding are examples. In both cases, the raw materials are converted into the basic geometry of the desired product.
Secondary processes follow the basic process and are performed to give the work part its final desired geometry. Examples in this category include machining (turning, drilling, milling, etc.) and press working operations (blanking, forming, drawing, etc.).
Operations to enhance physical properties do not perceptibly change the physical geometry of the work part. Instead, the physical properties of the material are improved in some way. Heat-treating operations to strengthen metal pans and preshrinking used in the garment industry are examples in this category.
Finishing operations are the final processes performed on the work part. Their purpose is, for example, to improve the appearance, or to provide a protective coating on the part. Examples in this fourth category include polishing, painting, and chrome plating Figure 6 presents an input/output model of a typical processing operation in manufacturing. Most manufacturing processes require five inputs:
1. Raw materials
2. Equipment
3. Tooling, fixtures
4. Energy (electrical energy)
5. Labour
Assembly operations
Assembly and joining processes constitute the second major type of manufacturing operation. In assembly, the distinguishing feature is that two or more separate components are joined together. Included in this category are mechanical fastening operations, which make use of screws, nuts, rivets, and so on, and joining processes, such as welding, brazing, and soldering. In the fabrication of a product, the assembly operations follow the processing operations.
Material handling and storage
A means of moving and storing materials between the processing and assembly operations must be provided. In most manufacturing plants, materials spend more time being moved and stored than being processed. In some cases, the majority of the labour cost in the factory is consumed in handling, moving, and storing materials. It is important that this function be carried out as efficiently as possible.
Inspection and testing
Inspection and testing are generally considered part of quality control. The purpose of inspection is to determine whether the manufactured product meets the established design standards and specifications. For example, inspection examines whether the actual dimensions of a mechanical part are within the tolerances indicated on the engineering drawing for the part and testing is generally concerned with the functional specifications of the final product rather than the individual parts that go into the product.
Control
The control function in manufacturing includes both the regulation of individual processing and assembly operations, and the management of plant-level activities. Control at the process level involves the achievement of certain performance objectives by proper manipulation of the inputs to the process. Control at the plant level includes effective use of labour, maintenance of the equipment, moving materials in the factory, shipping products of good quality on schedule, and keeping plant operating costs at the minimum level possible. The manufacturing control function at the plant level represents the major point of intersection between the physical operations in the factory and the information processing activities that occur in production.