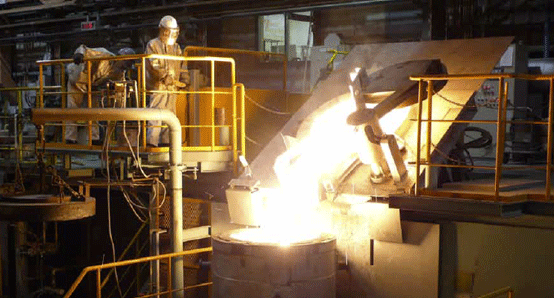
Molten steel being transferred into a ladle prior to atomisation (Courtesy Epson Atmix Corporation, Japan)
Iron powder production
In tonnage terms, the production of iron powders for PM structural part production dwarfs the production of all of the non-ferrous metal powders combined. Virtually all iron powders are produced by one of two processes.
The sponge iron process
The longest established of these processes is the sponge iron process, the leading example of a family of processes involving solid state reduction of an oxide. In the process, selected magnetite (Fe3O4) ore is mixed with coke and lime and placed in a silicon carbide retort.
The filled retort is then passed through a long kiln, where the reduction process leaves an iron “cake” and a slag. In subsequent steps, the retort is emptied, the reduced iron sponge is separated from the slag and is crushed and annealed.
The resultant powder is highly irregular in particle shape, therefore ensuring good “green strength” so that die-pressed compacts can be readily handled prior to sintering, and each particle contains internal pores (hence the term “sponge”) so that the good green strength is available at low compacted density levels.
Sponge iron provides the base feedstock for all iron-based, self-lubricating bearings and still accounts for around 30% of iron powder usage in PM structural parts.
Solid state reduction is also used for the production of refractory metal powders, using hydrogen as the reducing agent, and for the production of specialist iron powders by the reduction of mill scale (again using hydrogen).
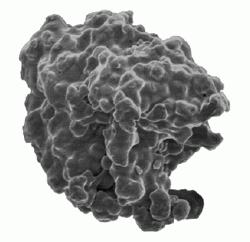
Typical morphology of an iron powder particle (ASC100.29) produced by water atomisation (Courtesy Höganäs AB, Sweden)
Water atomisation
Driven by the trend towards higher density levels in PM structural parts as a means of increasing performance levels, sponge iron powders have been increasingly supplanted by powders made by water atomisation.
Atomisation involves the disintegration of a thin stream of molten metal through the impingement of high energy jets of a fluid (liquid or gas). Water is the most commonly used liquid in atomisation.
Water atomised iron powders also have irregular particle shape and therefore good green strength. Unlike sponge iron, the individual powder particles do not contain internal porosity and, because of extensive development of the annealing process, have superior compressibility (see section on Forming processes). Water atomised powders are therefore the material of choice where high green density is sought in PM structural parts.
Non-ferrous metal powder production
Inert gas atomisation
Non-ferrous metal powders are produced by a variety of means. The most significant of these is another atomising process, this time using an inert gas as the atomising fluid. In inert gas atomisation, the particle shape produced is dependent on the time available for surface tension to take effect on the molten droplets prior to solidification and, if a low heat capacity gas is used (nitrogen and argon are most common), this time is extended and spherical powder shapes result.
Spherical powders are particularly useful in hot isostatic pressing (see section on Forming processes), where green strength is not an issue but initial packing density of the powder in the container is significant.
Close-coupled atomisation
The atomising nozzle design can provide either free-fall or close-coupled atomisation. In close-coupled (or confined) atomisation, the design of pouring nozzle and atomising head is adjusted so that impingement of the gas jets and molten stream occurs immediately below the exit of the nozzle with little or no free-fall height. This variant of atomisation technology has proved particularly useful for the production of fine powders for a range of applications, including Metal Injection Moulding.
Plasma atomisation
Developed by PyroGenesis, the plasma atomisation process uses argon plasma torches at > 10,000°C to melt and atomise titanium and other metals into fine droplets. The process has the distinction of producing highly flowable and very pure spherical metallic powders using wire as its feedstock. This method ensures a high level of traceability allowing for applications in the biomedical and aerospace sectors.
Centrifugal atomisation
A further branch of the “atomisation family” comprises a number of centrifugal atomisation processes. There are essentially two types of such processes; in the first type, a cup of molten metal is rotated at high speed or a molten stream of metal is allowed to fall onto a rotating disc or cone; in the second type, the Rotating Electrode Process (REP), a bar of metal is rotated and the free end is progressively melted by an arc from a tungsten electrode. If a plasma arc is involved, the process is known as PREP (Plasma Rotating Electrode Process) and this is a leading candidate for titanium powder production.
There are a few other powder production technologies that have areas of application.
Electrolysis
Electrolysis is a means of producing metal powders and has been most commonly used for the manufacture of copper powders for specialist applications. Electrolytic powders are produced by following the principles used in electroplating, with the conditions changed to produce a loose powdery deposit rather than a smooth adherently solid layer. The formation of powder deposits that adhere loosely to the cathode is favoured by low metal ion concentration in the electrolyte, high acid concentration and high cathode current density. The starting material is a pure metal anode.
Mechanical comminution
Brittle materials can be pulverised in ball mills, hammer mills or attritor mills to form powders. Intermetallics and ferro-alloys are commonly processed this way. As variants on this approach, Hydride-Dehydride (HDH) titanium alloy powders can be produced by reacting the alloy in solid form with hydrogen to form a brittle hydride, which can then be pulverised and dehydrided, and Hydrogen Decrepitation of Nd-Fe-B magnetic alloys, which can cause spontaneous decrepitation of the solid alloy.
Carbonyl and chemical conversion
Finally, there is a range of chemical conversion processes, with the leading example being the carbonyl process for the production of fine nickel or iron powders. In this process, the crude metal is reacted with CO under pressure to form the carbonyl, which is gaseous at reaction temperature, but decomposes to deposit the metal on raising temperature and lowering pressure.
Other chemical conversion processes include:
· The manufacture of Platinum powders from sponge created by thermally decomposing platinum ammonium chloride.
· The Sherritt-Gordon process for the manufacture of nickel powders by hydrogen reduction of a solution of a nickel salt under pressure.
· Chemical precipitation of metals from solution of a soluble salt e.g. silver can be precipitated by adding a reducing agent to a silver nitrate solution.