Milling in an attrition mill (Fig. 24) is effected by the stirring action of an agitator that has a vertical rotating shaft with horizontal arms. This motion causes a differential movement between the balls and the material being milled, thus providing a substantially higher degree of surface contact than is achieved in tumbler or vibratory mills.
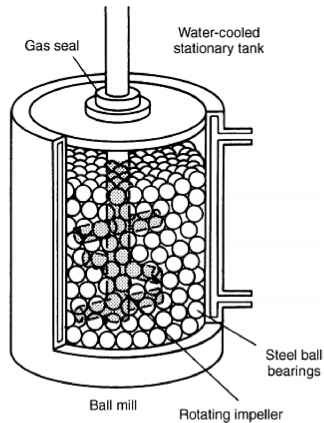
Fig. 24 Attrition ball mill
Milling is accomplished by impact and shear forces. The rotating charge of balls and milling product form a vortex at the upper end of the stirring shaft, into which the milling product and balls are drawn. The milling product is impacted by balls traveling in various trajectories that collide within the dilated charge of medium and powder.
While ball mills use large mediums, normally 12.7 mm (0.5 in.) or larger, and run at low rotational speeds of 10 to 50 rpm, the attrition mill agitator rotates at speeds ranging from 60 rpm for production units to 300 rpm for laboratory units and uses mediums that range from 3 to 6 mm (0.125 to 0.25 in.). Power input to attrition mills is used to agitate the medium, not to rotate or vibrate the heavy containment vessel.
For hard materials such as ceramics, carbides, and hard metals, attrition mills are more efficient than conventional tumbler and vibratory ball mills. The main advantages of attrition mills for mixing and blending tungsten carbide/cobalt cutting tool powders include short milling time, production of fine particle size (submicron sized), and enhanced smearing of cobalt onto carbide particles. Attrition mills effectively mill metals in inert atmospheres, such as in solid-state or mechanical alloying processes, but are not cost effective. Product output is relatively low with attrition mills, compared to large tumbler and vibratory ball mills. Consequently, tumbler ball mills usually are used for production runs of over 135 to 180 kg (300 to 400 lb) per day.
Mechanism of Attrition Mills. The central rotating shaft of an attrition mill, equipped with several horizontal arms, exerts sufficient stirring action to tumble the grinding medium randomly through the entire chamber volume, causing irregular movement by the following:
Impact action on the medium Rotational force on the medium
Tumbling force as medium fills the void left by the shaft
For fine grinding, both impact and shearing forces must be present. In attrition mills, impaction is caused by constant impinging of the grinding medium, due to irregular movement. Shearing action is produced by random movement of the balls in different rotational directions, which exerts shearing forces on the adjacent slurry. The strongest medium agitation occurs at a point located two-thirds of the way from the center. Grinding does not occur against the chamber walls, which serve as a container rather than a grinding surface. Minimal wear of chamber walls ensures long service life.
In attrition grinding, grinding time is related to medium diameter and agitator speeds, within given limits, as:
where t is grinding time required to reach a certain median particle size; k is a constant that varies with the slurry being processed and the type of medium and mill being used; d is diameter of the medium; and n is shaft movement, in revolutions per minute.
Attrition mills are classified as batch-, continuous-, or circulation-type mills. In the batch mill, material is fed into the jacketed chamber and is ground until the desired dispersion and particle size are achieved. Premixing is accomplished in the grinding chamber. Chamber walls are jacketed so that either hot or cold water can be circulated to control and maintain the temperature of the batch. Batch attrition mills can process high-density material, such as tungsten carbide, as well as viscous materials, and are suitable for dry grinding and for processing dispersion-strengthened metals.
Continuous attrition mills, best suited for large production output, consist of a tall, narrow, jacketed chamber through which a well-remixed slurry is pumped in at the bottom and discharged at the top. Grids located at the bottom and top retain the grinding medium.
The circulation grinding system is comprised of an attrition mill and a large holding tank, generally ten times the volume of the grinding unit. The circulation attrition mill is filled with medium and contains grids that restrain the medium while the slurry passes through. Attrition mills generally have high pumping rates. Usually, the contents of the holding tank are passed through the system at a rate of ten times per hour.
One advantage of the circulation attrition mill is that large quantities of material can be handled with a minimum investment in grinding medium and equipment. The slurry can be monitored continuously, and processing can be stopped when the desired particle size dispersion is achieved.