Before moving forward in order to understand the concept of six sigma, let us first understand the term sigma and statistics.
Sigma
The term sigma means standard deviation. Standard deviation measures how much variation exists in a distribution of data. It is a key factor in determining the acceptable number of defective units found in a population. Six sigma projects strive for no more than 3.4 defects per million opportunities, yet this number is confusing to many statisticians.
Standard Deviation
Small standard deviation means that data cluster closely around the middle of a distribution and there is little variability among the data. Normal distribution is the bell-shaped curve that is symmetrical about the mean or average value of a population.
Normal Distribution and Standard Deviation
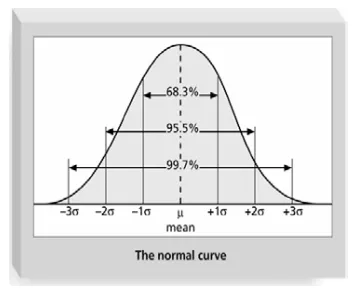
Definition
Six sigma at many organizations simply means a measure of quality that strives for near perfection. Six sigma is a disciplined, data-driven approach and methodology for eliminating defects (driving toward six standard deviations between the mean and the nearest specification limit) in any process– from manufacturing to transactional and from product to service.
Six sigma means a failure rate of 3.4 parts per million or 99.9997% perfect. However, the term in practice is used to denote more than simply counting defects. Six sigma can now imply a whole culture of strategies, tools and statistical methodologies to improve the bottom line of companies. In all, six sigma is a rigorous analytical process for anticipating and solving problems. The objective of six sigma is to improve profits through defect reduction, yield improvement, improved consumer satisfaction and best-in-class product/process performance.
Unlike the statistical term, “sigma” is a measure of conformance to specification. Table 12.1 shows examples.
Six Sigma and Defective Units
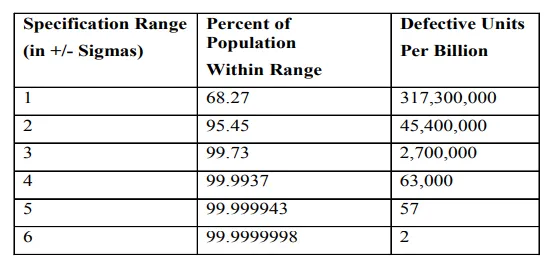
Table — Data for the short-term process output
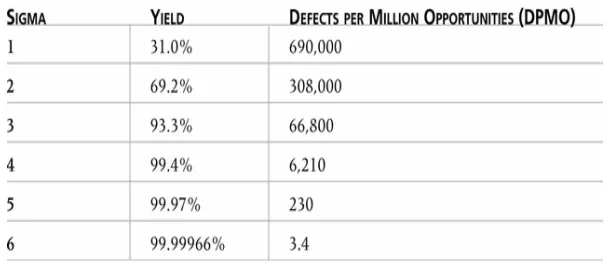
Table — Data when the process shifts somewhat over a long period of time
As non-conforming rate decreases, “sigma” rating increases. The sigma rating is based on the distribution of a process output as related to a customer requirement. Figure shows the short-term process output (solid blue) which is centered in the specification. The short-term variability of the process output is such that the Upper Specification Limit (USL) and the Lower Specification Limit (LSL) are both six standard deviations (called σ or sigma in statistical parlance) away from the center. Recognizing that most of the processes shift somewhat over a long period of time, an arbitrary change of plus or minus 1.5σ is expected to happen, leaving 4.5σ between the shifted average and the specification limit. This means that a process running at a six-sigma level in the short term can tolerate a relatively large amount of drift and still make only 3.4 PPM nonconforming over the long term with the dashed blue line.
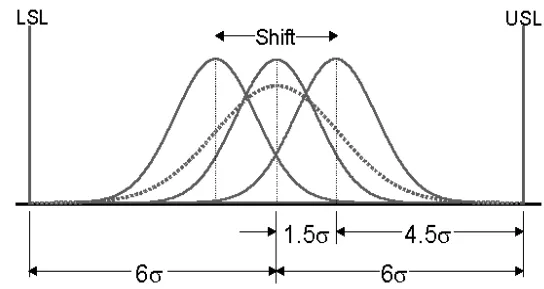
Figure– Short-term process output
Phases of Six Sigma
There are six generic implementation phases for six sigma. These are as follows:
· Establish management commitment
· Business diagnostics
· Develop the management infrastructure
· Business process identification and metrics
· Project selection
· Deployment
a) Training
b) Project execution
c) Review
Why is it important?
World-class companies typically operate at about four sigma or 99% perfection. To get to the six-sigma level means cutting down on huge costs and thereby wasted dollars. For example, if you were at four-sigma level, you would be producing products at the rate of 6,200 defectives for every million you produce vs. 3.4 defectives if you are at the six-sigma level. Moreover, six sigma improvement projects typically return in excess of $150k to $250k per project with a black belt returning as much as $1 million to the bottom line each year.
The popularity of six sigma is growing. Some of the companies that have successfully implemented six sigma are as follows:
· Motorola (1987)
· Texas Instruments (1988)
· IBM (1990)
· Asea Brown Boveri (1993)
· Allied Signal/Kodak (1994)
· GE (1995)
· Whirlpool
· PACCAR
· Invensys and Polaroid (1996/98)
Recently, Ford, DuPont, Dow Chemical, Microsoft and American Express have started working on instituting six sigma processes.
When to use it?
Bottom line drives management action. What is your cost of (poor) quality? First you need to determine that. If properly implemented, six sigma implementation can become a profit center for the company. Jack Welch at GE claims that the returns on six sigma implementation amount to about $500 million as of 1998. Remember that six sigma is complementary to other initiatives such as ISO or QS 9000 (which is mainly procedural), total quality management (which is mainly cultural), and statistical process control (which is primarily statistical process monitoring).