Eddy current testing for external defects in tubes where external access is not possible (e.g. buried pipelines), is conducted using internal probes. When testing thick-walled ferromagnetic metal pipes with conventional internal probes, very low frequencies (e.g. 30 Hz for a steel pipe 10 mm thick) are necessary to achieve the through-penetration of the eddy currents. This situation produces a very low sensitivity of flaw detection. The degree of penetration can, in principle, be increased by the application of a saturation magnetic field. However, because of the large volume of metal present, a large saturation unit carrying a heavy direct current may be required to produce an adequate saturating field.
The difficulties encountered in the internal testing of ferromagnetic tubes can be greatly alleviated with the use of the remote field eddy current method. This method provides measurable through penetration of the walls at three times the maximum frequency possible with the conventional direct field method. This technique was introduced by Schmidt in 1958. Although it has been used by the petroleum industry for detecting corrosion in their installations since the early 1960s, it has only recently evoked general interest. This interest is largely because the method is highly sensitive to variations in wall thickness, but relatively insensitive to fill-factor changes. The method has the added advantage of allowing equal sensitivities of detection at both the inner and outer surfaces of a ferromagnetic tube. It cannot, however, differentiate between signals from these respective surfaces.
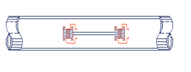