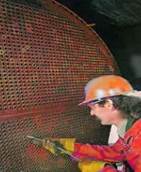
Eddy current inspection is often used to detect corrosion, erosion, cracking and other changes in tubing. Heat exchangers and steam generators, which are used in power plants, have thousands of tubes that must be prevented from leaking. This is especially important in nuclear power plants where reused, contaminated water must be prevented from mixing with fresh water that will be returned to the environment. The contaminated water flows on one side of the tube (inside or outside) and the fresh water flows on the other side. The heat is transferred from the contaminated water to the fresh water and the fresh water is then returned back to is source, which is usually a lake or river. It is very important to keep the two water sources from mixing, so power plants are periodically shutdown so the tubes and other equipment can be inspected and repaired. The eddy current test method and the related remote field testing method provide high-speed inspection techniques for these applications.
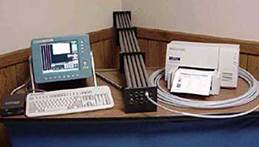
A technique that is often used involves feeding a differential bobbin probe into the individual tube of the heat exchanger. With the differential probe, no signal will be seen on the eddy current instrument as long as no metal thinning is present. When metal thinning is present, a loop will be seen on the impedance plane as one coil of the differential probe passes over the flawed area and a second loop will be produced when the second coil passes over the damage. When the corrosion is on the outside surface of the tube, the depth of corrosion is indicated by a shift in the phase lag. The size of the indication provides an indication of the total extent of the corrosion damage.
Note the different signal responses provided by the two probes. Also note that the absolute probe is much more sensitive to dings and the build up of magnetite on the outside of the tube than the differential probe is.