Lubricant is a material that reduces friction between the mutual contact surfaces and improves the smoothness, with the motion of one surface over other
The material used in this process is known as lubricant. Lubricants are generally semi liquids or liquids, in some cases gases or solids and sometimes combination of liquids, solids and gases.
When the body is moving then heat is generated on the surface, in that process with the help of the lubricant heat generation is minimized. Lubricant transfers the forces, transporting foreign particles, cooling or heating the surfaces. Reducing the friction is known as slipperiness or lubricity.
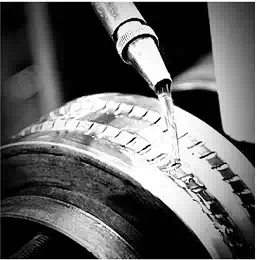
Basic type of lubricants
- Oil
- Gases or liquid lubrication
- Greases or semi-solid lubrication
- Dry Lubricants or solid lubrication
Oils
Oils are used to cover all the liquid lubricants. Different types of oil lubricants are natural oils, mineral oils, synthetic oils, process fluids and emulsions.
Types of oils
Natural oils
The natural oils are mainly used in the boundary lubricants. It consists of animal facts and vegetable oils. Compared to the mineral oils, natural oils are less stable. In the manufacturing of food and bio degradable industry palm oil and castor oil are used as lubricant in present days.
Mineral oils
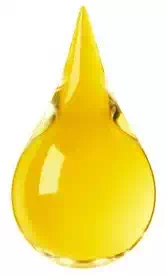
Mineral oils are most commonly used lubricants. The below shown is a picture sample of the mineral oil.
When compare to the other oils mineral oils are considered to be standard. Generally mineral oils are bi-products of petroleum. In mineral oils we can find appropriate viscosity for the lubrication, so it acts a lubricant. In the mineral oils the chemical composition consists of hydrocarbons, which covers only the hydrogen and carbon.
Synthetic oils
Synthetic oil consists of di-esters, Polyol esters, phosphate ester, hydrocarbons, silicone’s and polyglycols.
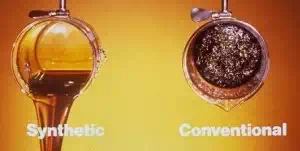
The synthetic oils are different from each other in the properties and performance.
Di-esters:
Die esters are used in high temperatures. It acts as a good lubricant and available in different viscosities. Die esters are used as a base oil in industries for lubrication.
Polyol esters:
Polyol esters are mainly used in aircraft jet engines. They are available at very high viscosity. They are act as good lubricating agents.
Phosphate esters:
The reaction between the alcohols and phosphoric acids gives the phosphate esters. They are mainly used in the aircraft engines, coal mines, hot metal process and hydraulic system. The chemical properties are related to best anti wear additives and provide good lubricant. In rubber and plastics it shows the poor thermal stability.
Synthetic hydrocarbons:
Synthetic hydrocarbons are also classified into several types; one among them is branched- chain oil, this is also known as polyalphaolefins. Polyalphaolefins are the important class of synthetic oils and they look like mineral oils. In refined mineral oils we can perceive the similar properties and performance.
Silicones:
Silicones are the polymer substances. They are based on the chain reaction which contains alternate oxygen and silicon atoms. In different viscosity ranges the silicones are available. In high temperatures conditions they are stable. In steel material it shows very poor boundary lubrication.
Polyglycols:
These are stretched chain polymeric liquid. When the polyglycols are heated above 200, in that process they decompose completely and never produce products.
B) Gases
Gases lubrication is similar to the liquid lubrication. The liquids and gases are viscous fluids but they are altered into two particulars. The viscosity of the gases is lower compare to the liquids where the compressibility is higher. In Comparison to the air, gases are lower in the load capacity and film thickness. In gases we find that a resistance is seen in attack the bearings, where they can easily decompose.
Advantages of gases lubrication
- In lubrication there is no need of seal requirement
- High speeds are possible
- Low friction and viscosity
- There is no solidification, vaporization, decomposition and cavitation
- The temperature is ranges from – 200 to 2000
Disadvantages of gases lubrication
- The capability of load is very low
- Low film thickness and damping
- High grade manufactures are required to get close tolerances.
- Low clearances and smooth surfaces
C) Greases:
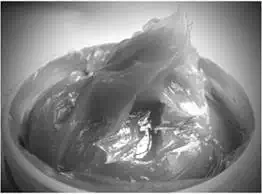
Grease is also known as semi solid lubricant. In the greases we can see the combination of the thickeners and lubricating oils.
Thickeners present in the oil are spread in the lubrication oil to produce a stable structure or gel in the gears. And rolling contact bearing the greases provides semi-permanent lubrication and the maintenance cost is also low. Greases are not used at high speed because the friction is developed in the vehicle which causes overheating.
Advantages of grease
- Reduces vibration and noise
- The lubricant is good for vertical shafts
- Oil vapour problems are reduced
- Water resistance is also reduced
Disadvantages of grease
- It does not performs the cooling operation due to the semi-solid nature and we find the poor dissipation of heat
- No friction
- Contaminants are not separated
- Dust and dirt particles are not easily separated from the grease
D) Solid lubricants
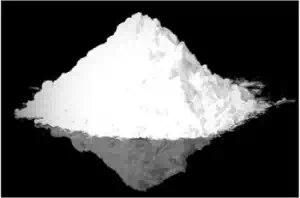
Solid lubrication is also known as the dry lubrication. In the solid lubrication without the help of the liquid medium friction is reduced between the two sliding surfaces.
In solid lubricant, the material is placed between the two bearing surfaces the solid material is placed. When load is applied on the bearing material, then it shears easily. The friction coefficient is mainly related to bearing load and shear force.
Requirements
- Material should be able to maintain the load without any deformations and distortions
- Wear rate and coefficient of the friction must be low and acceptable.
Advantages of solid lubrication
- At high loads and pressure it is more effective than fluid lubricants
- They are highly stable in dangerous radiations, temperatures and sensitive environment
- Higher cleanliness
- Equipment must be simple and light
Disadvantages of solid lubrication
- Self-healing properties are very poor.
- The broken solid film leads to shortage the life of the lubricant
- We can see high friction and wear
- Due to low thermal conductivities we can see poor heat dissipation.
Solid lubricants are divided into 4 types .they are
Polymer, carbon and graphite, metal solid, ceramic and cermet
Polymers
Polymers are suitable for the light loads. Before selecting a polymer one have an idea on the limitations they have:
- Due to melting of the polymers premature failures can occur because of the low thermal conductivity of a polymer that restricts the heat dissipation.
- In slide contact of the two polymers are operated normally and it reduces the speed of the polymer related to metal surface.
The polymers are classified in to 3 types they are
- Synthetic polymers,
- Nylon,
- Poly tetra fluoro ethylene