Rolling
Rolling is a type of motion with respect to the surface it combines the translation and rotation of the object. During rolling there is no sliding at that case we can say that is pure rolling, if any sliding is observe during the process than we can see the deformation related to the area so some sliding is occurred. Rolling is the metal forming operation we can see in industries. Rolling is divided in to two types they are hot rolling and cold rolling. Rolling process must be done with the help of hot rolling only in case if they mention then choose for the cold rolling process. When you are comparing the rougher and smoother rolls for higher reduction at that situation the rougher rolls can produce the higher reduction during the process.
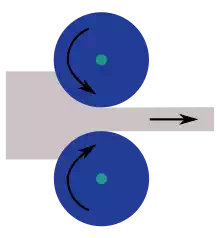
Hot Rolling:
Hot rolling process can be done during the uniform working temperatures. Hot rolling is used to break down the blocks in to billets and blooms. From that it transfers the material to produce new products like sheets, plastics. A set of rolls with Compressive forces which was applied on the materials to obtain a plastic deformation. Due to rolling the cross section of the work piece material must be reduced. The material must be passed in between the rolling’s. At that case process of time the material should be pressed it results to length of the work piece is increased and thickness is reduced. Hot rolling is done at the high temperature ranges only to develop the large deformation. It results to stress free products. The major problem occurred at the time of scaling. No dimensional accuracy is maintained during the hot rolling process.
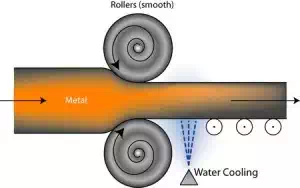
Cold Rolling:
Cold rolling is used to increase the strength and hardening of the material during the process and also improves the surface finish of the work piece materials. During the cold rolling we can produce the products like sheets, bars, rods, strips etc. Cold rolling process produce smaller products compare with the hot rolling process. Cold rolling does not reduce the width of the material when compare to the hot rolling process. In a single pass the hot rolling reduce the width of the material. We can see various types of strips and sheets in cold rolling process they are skin rolled, quarter hard, half hard, and full hard. By using the full hard rolling it reduce the thickness of material by 50 %. Skin rolling reduces the 0.5 to 1 % of the material during the process. With the help of cold rolling we can get the high surface finish, uniform thickness etc.
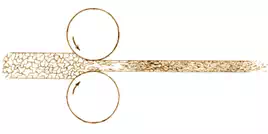
Rolling mills
Rolling mills consists of bearings to supports the gear box, motor, speed control devices, hydraulic system and rolls etc. Rolling mills are dividing in to several types they are
· Two high rolling mills,
· Three high rolling mills,
· Four high rolling mills,
· Tandem rolling mills and
· Cluster rolling mills.
The basic type used in the rolling mills is two high rolling mills.
Two High rolling mills:
In the two high rolling mills two reversed rolls are used for the process. One roll is operated in one direction and the other is operated in the opposite direction. The two high rolling mills are divided in to two types they are
Reversing mills and non-reversing mills
Two High Reversing Mills
The two high reversing type mills type are used in the slabing mills and measuring and for outline work in rails, mills, plates, and structure. Compare with the other process this is very expensive.by using this type of mills we can increase the productivity of the material.
Two high non reversing mills
In the two high non reversing mills are operating in the same direction. Both the rolls are moving in the same direction continuously. In this process less amount of motive force is used .the material must be carried back every time and passing the material in to the rolls. This process is used in the train plate mills.
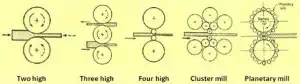
Three high rolling mills
In this process we can see three rolls they are arranged in the parallel direction one above the other. The roll is travelling in the opposite direction at that time of process the material may be moving in between the top and middle roll in one direction and the middle and foot roll in the opposite direction. Initially the work piece must be passed through the foot roll and then middle roll then it returns in between the middle and the first rolls. During the passes in between the rolls the thickness of the work piece material must be reduced. Lifted tables are arranged on the tables to move the material in vertical direction or either sides. Because of that arrangement the material must be suckled automatically into the gaps present in the rolls.by using three high rolling mills we can produce groove and plain surface on the work piece material.
Four high rolling mills:
In this milling process four rolls are arranged one above the other. The upper and lower rolls are operating in one direction and the middle two rolls are operating in opposite direction. Compare with the upper and lower rolls the middle two rolls are smaller in size. The upper and lower rolls are known as backup rolls they are providing hardness to the work rolls (middle rolls).the four rolling are used for the rolling of the plates, sheets and strips for cold and hot rolling
Tandem Rolling mills:
Two to three sets of rolls are arranged in parallel arrangement. The upper and lower rolls are moving in one direction and the middle two rolls are moving in the opposite direction. So process is done in between the rolls.
Cluster rolling mills:
Cluster rolling mill is special type of four high rolling. In this type of rolling mills two back up rolls are arranged to the work rolls. This type of rolling mills is suitable for the very small diameter materials with suitable lengths.
Advantages of hot rolling
- When the metal is in plastic stage at that time we can see large deformation
- We can notice that the porosity of the metal must be minimized
- Impurities are broken and spread through the metal
- Metal consists of the grain structures that are polished
- The physical proprieties must be improved.
Disadvantages of hot rolling:
- Due to high temperatures corrosions must be take place on the surface of the metal
- Due to corrosion surface finish must be poor and metal loss
- Tolerance maintenance is not possible.
- High amount of tool cost for the process.
Advantages of cold rolling:
- Compare to the hot rolling process dimensional control is possible in cold rolling
- There is no oxidation process takes place in the process so high surface finish is possible.
- Hardness and strength of the material is increased
Disadvantages of cold rolling
- By using cold process we can process the ductile material sonly
Rolling defects:
By using the rolls they can produce high amount of rolling force on the rolling sheets at that case of time the sheet thickness can be increased without requirement. Elastic deformation in the mills is takes place. The deformation varies from 1 to 4.Due to the elastic deformation we can see uneven thickness in the material sheets. To reduce the deformation we can choose the material with high elastic modulus. Smaller diameter rolls are used for producing very thin sheets. Flatness of the sheets mainly depends upon the deflection of the roll.