Creep is the time-varying plastic deformation of a material stressed at high temperatures. Examples: turbine blades, steam generators. Keys are the time dependence of the strain and the high temperature.
The Creep Curve
Creep in metals is defined as time dependent plastic deformation at constant stress (or load) and temperature. The form of a typical creep curve of strain versus time is in Figure. The slope of this curve is the creep rate dε/dt. The curve may show the instantaneous elastic and plastic strain that occurs as the load is applied, followed by the plastic strain which occurs over time. Three stages to the creep curve may be identified:
Primary creep: in which the creep resistance increases with strain leading to a decreasing creep strain rate.
Secondary (Steady State) creep: in which there is a balance between work hardening and recovery processes, leading to a minimum constant creep rate.
Tertiary creep: in which there is an accelerating creep rate due to the accumulating damage, which leads to creep rupture, and which may only be seen at high temperatures and stresses and in constant load machines.
The minimum secondary creep rate is of most interest to design engineers, since failure avoidance is required and in this region some predictability is possible. In the USA two Standards are commonly used: (i) The stress to produce a creep rate of 0.0001% per hour (1% in
10,000 hours). (ii) The stress to produce a creep rate of 0.00001% per hour (1% in 100,000 hours or approximately 11.5 years). The first requirement would be typical of that for gas turbine blades, while the second for steam turbines. Constant load machines simulate real engineering situations more accurately, but as the specimen extends its cross section area reduces, leading to a rising stress. Machines designed to reduce the load to compensate for the reduced area and maintain constant stress may produce an extended steady state region.
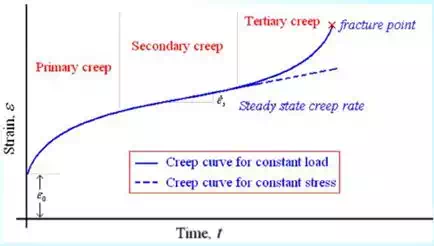