While designing machines, often it needs to provide supports for the rotating shafts either separately or inbuilt in the parts of the machine itself. Such a support, called bearing, not only serves as support to the rotating shaft but also facilitate its smooth running as well. Almost all kinds of machineries have bearings, a few commonly found examples which invariably have bearings are, crankshafts of engines, axle of automobiles, spindles of machine tools such as, lathe, drilling, milling and grinding machines, shafting in workshops, etc.
Bearing technology represents one of the old problems for mechanical engineers. Rolling element bearings developed in the last century were a revolutionary improvement over the plain bearings that had been pushed to their limits in applications like electric motors and automobile wheels. Similarly, rolling element bearings are today being pushed to their technical limits by the demands of applications like semiconductor manufacturing, high resolution scanning, and high-speed machinery.
Air bearings represent the next logical step in bearing design. Air bearings in general have a proven track record having been employed in coordinate measuring machines for 20 years. The many technical advantages of air bearings such as near zero friction and wear, high speed and high precision capabilities, and no oil lubrication requirements are powerful advantages for today’s machine designers. However, these benefits have not been more fully utilized to date because air bearings are difficult to manufacture and they have not been commercially available until recently.
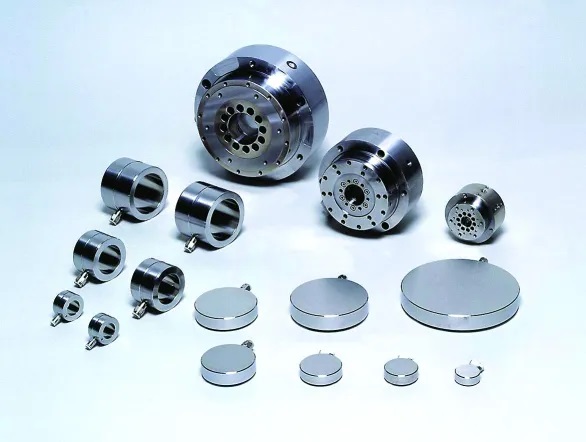
INTRODUCTION
- An air bearing is a non-contacting system where a gas film (typically air) acts as the lubricant that separates the two surfaces in relative motion.
- Air bearing technology offers real advantages to applications where the demand for accuracy, speed and reliability is crucial.
- Air bearings avoid the traditional bearing-related problems of friction, wear, and lubricant handling, and offer distinct advantages in precision positioning and high speed applications.
How Air Bearings Work
The basic principle of operation of air bearings has been established for more than fifty years. An air bearing may comprise of a sleeve separated from a plain shaft by a small gap, typically 5–50 um. High pressure air is fed through small orifices in the sleeve through to the bearing gap where it flows along the gap and out of the ends of the bearing. Orifice size is matched to the bearing size so that under no load the pressure in the gap, just downstream of the orifice, is approximately half the supply pressure. When a radial load is applied, the gap on one side of the shaft closes down increasing its resistance to airflow and causing pressure to rise. On the opposite side of the shaft, the larger gap has a reduced resistance to airflow and allows pressure to fall. The pressure difference across the bearing gives it the capacity to support the applied load without incurring any metal – metal contact even if there is no shaft rotation.
Air Bearing Spindles
Loadpoint air bearing spindles employ 2 or more cylindrical journal bearings to support radial loads and an opposed pair of flat, annular thrust bearings to support axial loads. A practical design of air spindle also has an integral drive motor and means of work holding.
In a typical spindle compressed air enters through a port on the rear face and is fed through drillings to reservoirs surrounding each journal bearing and reservoirs positioned either side of the thrust bearings. From the reservoirs, air is fed through rows of orifices into the bearing gaps. Exhaust air from the ends of the journal bearings, inner and outer edges of the thrust bearings is vented to atmosphere.
Cooling water enters the air bearing spindle through a port on the rear face. From here it is typically ducted along the spindle where it flows through a reservoir surrounding the front bearing. The cooling water is then fed back along the spindle where it passes through a reservoir surrounding the rear journal bearing before exiting through a port on the spindle’s rear face.
There are basically two types of air bearing:
- Aerostatic Bearing
- Aerodynamic Bearing
ADVANTAGES AND DISADVANTAGES OF AIR BEARINGS
ADVANTAGES:
- Greater Precision
- High Speed
- Increased Tool Life
- Improved Surface Finish
- Long Bearing Life
- Low Thermal Growth
- Lack of Maintenance
- Large Load Capacity
- Reduced Vibration
DISADVANTAGES:
- High geometry accuracy during manufacturing.
- High cost.
- Need to have a clean working environment.
APPLICATIONS OF AIR BEARING
- Lifting weights
- Machines for the Image Setting Industry
- Coordinate Measuring Machines
- Testing Equipment
- High Speed Equipment
- Ultra accurate machine tools
- Linear Stages