Railways have used vacuum brakes for years, and automobiles still utilize vacuum assisted brakes. There is always a need for better braking system than the current generation of brakes. The primary goal of this study is to demonstrate that vacuum brakes can be a better alternative to todayβs hydraulic brakes. Since the brake actuation is done using a mechanical linkage, a suitable wheel cylinder assembly has been designed and manufactured.
CONSTRUCTION OF VACUUM BRAKE SYSTEM
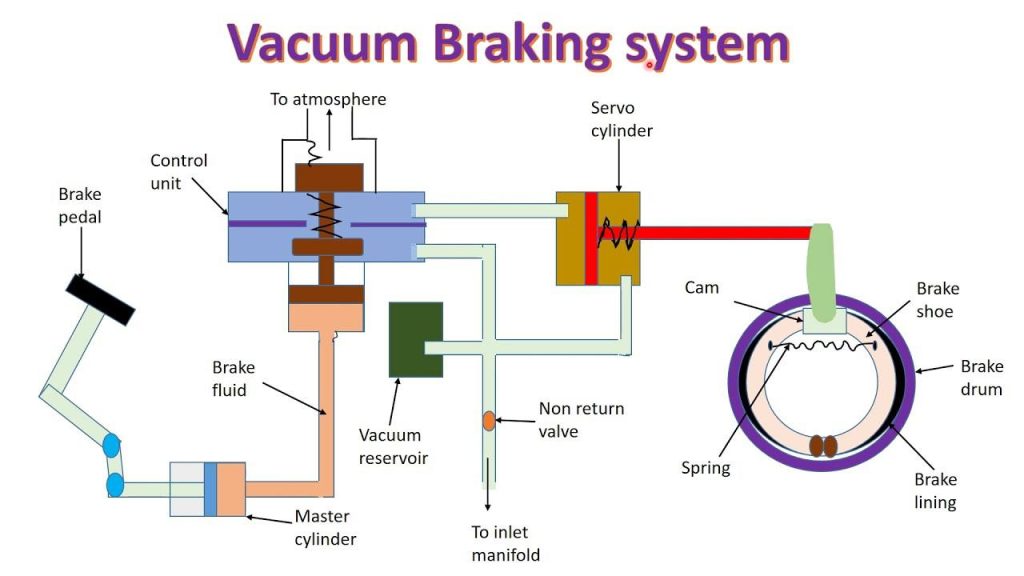
Vacuum braking system consists of:
- Brake cylinder,
- Compressor,
- Vacuum reservoir,
- Direction control valve,
- Flow control valve,
- Brake hoses,
- Brake linkages,
- Drum brake and foot brake pedal.
WORKING OF VACUUM BRAKE SYSTEM
- The brakes are always in released condition with vacuum unit the driver pushes the brake pedal. In this condition position of piston cap is in cap end of the brake cylinder and cam is twisted for compressing the spring which provides free rotation of drum.
- When the driver pushes the brake pedal slowly then the flow control valves open slightly to the atmosphere. It loss of vacuum causes the brake to be applied due to spring force. When the flow control valve opens fully then alternatively the forward direction.
- The direction of flow is changed and atmospheric air enter through the exhaust port of direction control valve to piston cap end. Due to pressure difference the piston moves backward with vacuum and spring force.
- The movement of link rod attached with piston rod releases the cam to normal position which makes internal resistances from the brake shoes against drum.
- When driver release the brake pedal then valve lever comes back to initial position. The direction of flow is again changed and atmospheric air enter through the exhaust port of direction control valve to piston rod end. Due to pressure difference the piston moves forward with vacuum.
- The movement of link rod attached with piston rod twists the cam and compresses the spring which makes enough clearances between brake shoes and the drum. This release the brake.
The detailed study on the vacuum brakes system has been done. From the calculations based on the brake tests performed on road and dynamometer, various parameters like deceleration, stopping distance, brake efficiency, brake force are known to be better in vacuum brake system than hydraulic brake system.
Further, the results of static structural analysis performed with ANSYS software shows that the material EN 8 material with which the camshaft, wheel cylinder assembly has been manufactured was found to be reliable and can withstand more force than it is actually experiencing. Further, the air from the compressor can be used for any other auxiliary systems like tire inflation system, Air impact wrench, etc. Hence it can be concluded that vacuum brakes can be a good alternate to current generation hydraulic brake system.
ADVANTAGES AND LIMITATIONS
ADVANTAGES
- Simple in design.
- Ability to get partial release, the pneumatic brake do not require additional equipment.
- Greater amount of safety, vacuum loss results in braking of vehicle.
- Highly reliable in case of railway wagon.
- Vacuum brakes are also called fail safe since the vacuum is used for applying the brake.
LIMITATIONS
- A very large brake piston and cylinder is required to generate the force necessary on the brake blocks.
- Vacuum brakes are slow in release the brakes.
- Additional equipment are necessary to speed up its operation.