Aluminium Engineering
Aluminium is a core engineering material that allows for a limitless number of structures to be built. It is a light material that contains alloys, which possess a superior strength to weight ratio than steel. Aluminium offers a specific gravity of 2.7, while the mass and weight are only 35% of iron and 30% of copper.
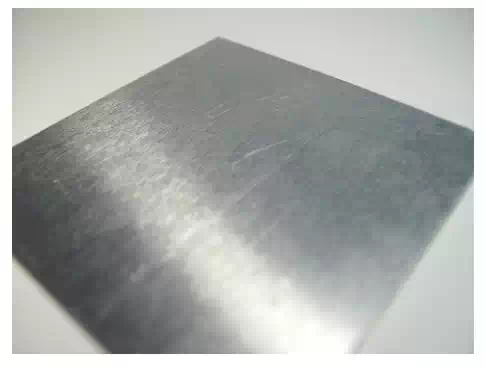
As one of the core building materials in projects, engineers will often use it because it is cost effective to transport. At the same time it is also one of the most resistant metals to corrosion. That makes it virtually maintenance free, and perhaps one of the most viable solutions for a long-term structure that is being designed.
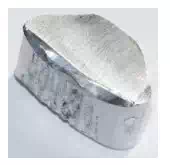
Considered one of the most eco-friendly core engineering materials, it uses minimal energy and resources during construction. While the most common of the building materials for modular homes, it is also found in other projects including:
- Culverts
- Curtain walls on high rises
- Dome roofs
- Handrails
- Highway signs
- Portable buildings
- Scaffolding
- Water towers
Aluminium cladding that has been insulated is also thermally efficient. When used in a structure, it helps to keep the building cooler in the hotter months and warmer in the coldest months. Properly insulated aluminium cladding has been shown to be as effective as 4” of brick and 10” of stone.
When used in design, aluminium is one of the more pliable core building materials. It can be bonded, curved, welded or tapered to meet the design specifications of a building. Making it one of the most versatile choices that is available.
Stainless Steel Engineering
Stainless steel is used extensively all around the world. It has the same strength as regular steel but with the advantage of being corrosion resistant, and certainly more attractive than common steel. On the downside, it is considerably more expensive than regular steel, particularly if it’s been used a very large quantities. For this reason, it is essential to find a reputable stainless-steel engineering firm to hand medium to large projects.
When it comes to stainless steel engineering, you don’t only want experienced engineers working on your project either. You also want to work with a company that is able to guarantee the quality of the materials they use, keeping in mind that not all stainless steel is the same when it comes to quality. While different grades of stainless steel are deliberately produced in order to meet varying demands, some of it is simply poor quality. Using cheap stainless steel might save you money in the short term not in the long run it is going to cost you more because it will need to be replaced, and replacing it will also entail labour costs.
Understanding the Grades
Most of us use stainless steel item on a daily basis, even if it is only our knives and forks, and perhaps a few pots. For the average homeowner, stainless steel does usually represent a large cash outlay, but when it comes to stainless steel engineering applications, it is a very different matter. As a general rule, it is regarded as a “special material” and typically only used if and when necessary. Not only is stainless steel considerably more costly, but it is also far more difficult to machine when compared to regular carbon steels or aluminium.
Manufacturers produce different grades for different purposes, and newcomers to the stainless-steel engineering industry can quickly become confused with regards to the various grades of stainless steel. For example, some stainless steel might contain 11% chromium, while other stainless steel can contain more than 20%. Generally speaking, there are six grades of stainless steel, each with their own set of pros and cons.
Austenitic Stainless Steel (Sae 300 & Sae 200)
SAE 300 (chromium nickel) and SAE 200 (manganese nickel) are by far the two most commonly used grades, and both are extensively used for making cookware; cutlery, and a wide range of medical items. They are also used for other manufacturing seamless tubing intended for the food and beverage industry due to their remarkable corrosion resistance properties which is achieved by a 16% chromium content, along with a small amount of nickel or manganese.
Ferritic Stainless Steel
This grade of stainless steel contains between 10.5% and 27% chromium, and hardly any nickel at all although a range of alloys can be added in order to achieve certain goals. One example would be that unlike most stainless steel, ferritic stainless steel is magnetic. It also has much better ductility than the stainless steel mentioned above, but it is more difficult to weld, and somewhat less resistant to corrosion, two important factors which need to be taken into consideration by stainless steel engineering firms when designing any particular structures. As with the above grades, ferritic stainless steel is widely used for manufacturing cutlery and cookware, but at the lower end of the price range.
Martensitic Stainless Steel
With chromium content of 12 to 14 percent, martensitic stainless steel offer less corrosion resistance than the two grades mentioned above, but machining it is considerably easier. I can also be hardened, which in turn has made it the stainless steel of choice for cutlery; knives and a range of tools. It is also typically the material used for making razor blades and blades used in food processors, although this is not always the case.
Precipitation-Hardening Martensitic Stainless Steel
This is the “go to” material for stainless steel engineering firms tasked with designing and/or manufacturing various components used in the paper industry, and things like turbine blades used in the aerospace industry. Its biggest draw is superior strength and corrosion resistance when compared to regular martensitic stainless steel.
Duplex Stainless Steel
Duplex stainless steel is used extensively in the marine and petrochemical industries as well as in the pulp and paper industry and the chemical industry. It is largely valued by stainless steel engineering companies for it enhanced strength and cheaper cost when compared to many other grades of stainless steel. Additionally, duplex stainless steel is also notably more resistant to stress-corrosion cracking; crevice corrosion and pitting when compared to some other grades.
The Future of Stainless Steel Engineering
Stainless steel is used in one form or another in virtually every industry, from surgical implants to aircraft turbines, so it comes as little surprise that new grades are continuously being developed and tested for their suitability. This ongoing development process inevitably means that stainless steel engineering companies are under constant pressure to revise their own strategies and techniques, beginning with the design phase of projects, and continuing all the way through the production stage.
According to statistics, current global production of stainless steel exceeds 25 million tons, and this figure is set to rise dramatically in the coming years. As with many commodities that enjoy such a big demand, the quality of stainless steel can vary significantly from one manufacturer to the next. For the reason, MJS Engineering only use the highest quality British made stainless steel, regardless of how big or how small a project might be. In addition to using only the best material, we also take great pride in the fact that we employ some of the country’s most experienced and most skilled engineers.
When it comes to stainless steel engineering, taking shortcuts or cutting corners can prove to be an extremely costly mistake, and one which can have a devastating impact, not only on the clients we serve, but also on our own rock-solid reputation here at MJS Engineering.
Titanium Engineering
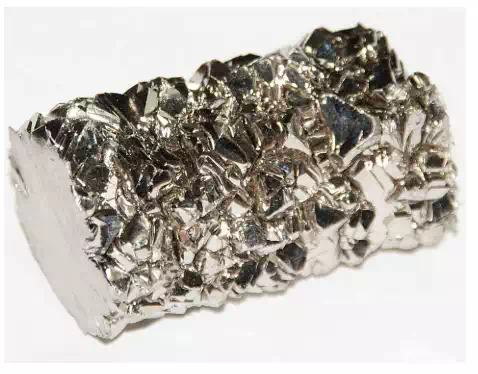
Titanium’s Properties
Titanium is a highly stable metal that isn’t impacted by corrosion. Its thermal expansion is half of stainless steel and a third of aluminium. The gravity of titanium is 60% of steel at 4.51 g/cm3. That is half of copper and 1.7 times the gravity of aluminium. This means it puts less of a burden on the building.
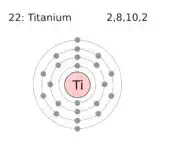
Shock resistant and durable, it also has excellent mechanical strength, making it one of the better core building materials on the market. In areas that are plagued with earthquakes or could experience violent movement, this is the choice building material. It also offers exceptional insulation in buildings and can reduce heating and cooling costs.
COST OF TITANIUM ENGINEERING
Guggenheim Museum Bilbao and Cerritos Millennium Library were the first buildings to utilize Titanium panels. However, titanium isn’t cost effective for most projects. It costs nearly 10 times stainless steel and in most cases, would require a million-dollar budget. It is also difficult to weld and the welds that are formed are not as neat as with other metals that can be used.
Additionally, it does have a higher tensile strength, but has lower elastic modulus than steel. This causes service level concerns with the metal. The only way for them to work in most settings is to shorten the span of beams and deepen them. Cutting the beams is also difficult.
In most cases, choosing stainless steel over titanium makes more sense when you compare the costs and the overall practicality of using this material.
Brief History of Bronze
The Romans, who were well-known for their incredible engineering skills, were the first people to use bronze cladding. Up until that point it had mainly been used for sculpting, making tools, and weapons; it was not until the Middle Ages that bronze became widely used in architecture.
PROPERTIES OF BRONZE
Like some other core building materials, bronze is an alloy. It consists mainly of copper, but by combining it with other metals it produces an alloy that is much harder than simple copper. Architectural bronze is generally 57% copper, 40% zinc, and 3% lead. It is often regarded as a brass alloy because it contains zinc as the primary alloying ingredient.
BRONZE USES
While the decorative uses for bronze are nearly unlimited, it is often used in door frames, window casements, store fronts, and various forms of decorative tiles. Because it has become such a prized metal over the centuries, bronze is usually used to make small items meant to accent the décor and add a touch of refinement rather than in large quantities.
BRONZE OXIDATION
In its natural state, or “raw”, bronze is salmon coloured, but it is rarely ever seen in this condition. As it ages, bronze goes through a continuous process of corrosion and oxidation that turn it anywhere from dark brown to lime green in colour. This layer of oxidation is call the patina and is desirable in some instances. The stages of oxidation or corrosion can vary depending on such things as the composition, exposure to the elements, and what materials are adjacent to the bronze.
BRONZE ENGINEERING
In many cases when architectural bronze is used, the highly polished or “raw” look is desirable and is achieved by coating the core materials with clear lacquer or frequent oiling or polishing of the material.
Making use of bronze in the design of your home or structure is not only a long-lasting investment, but the aesthetic value that it adds to any project is undeniable.
Marble Engineering
Many of the oldest buildings in the world stand as a testament that stone is one of the most reliable and stable of all building materials. Of all types of stone, one of the most beautiful and sought after is marble. Famous building such as the Taj Mahal and the Parthenon are examples of the beauty and durability of marble, as are many Roman and Greek sculptures. Buildings such as the Lincoln Memorial and the Washington Monument are more recent, but no less striking examples of this magnificent stone.
With proper engineering, the uses of marble in construction are almost endless. The price, however, is somewhat limiting to most budgets. A metamorphic rock, marble can be found in a vast array of patterns and colours, some of which include variations of brown, red, and green, as well as many shades of white. The trace minerals that are trapped in the stone give it the characteristic veining and flecking that make it one of the more popular building materials.
Common Uses for Marble Engineering
In modern society the most common uses for marble are in flooring or countertops, but it can also be used in many more innovative ways. Since it is somewhat softer than quartz, or granite, it can be cut into very thin slabs and given a translucent look through the use of backlighting. In this way, many people can use marble to enhance the overall appearance of their home or business without the expense of flooring an entire structure.
Marble can be found throughout the world and is quarried in blocks for building, as well as being cut into thin slabs for architectural cladding, flooring, and countertops. Because of its structural stability it can easily span long distances while still providing a stable expanse if the proper engineering techniques are employed.
Different types of marble are used for different purposes in construction and for areas that will receive a high amount of use, such as floors, Dolomite marbles are used. While it can stain, wear, or scratch over time, the endless uses and the timeless beauty of marble will ensure that it remains one of the most elegant building materials to be found.
Timber Engineering
Whether you are building a home or a business, choosing the right material for its construction is perhaps the single most important decision that you make. With such a vast array of building materials available (both natural and man- made), the choices may seem overwhelming at best. When faced with so many different choices, it can be easy to overlook one of the simplest, sturdiest, and most cost-effective building materials; timber.
Advantages of Timber Engineering
From the engineering standpoint, timber makes a great building material because its flexibility makes it able to accommodate heavy weight loads because it will bend to adjust. When placed vertically, timbers are extremely rigid and strong; perfect for weight bearing walls. The thermal efficiency of timber also allows you to make the walls thinner, giving you up to 10% more space in every room or hallway.
In addition to the extra space and thermal efficiency, timber provides excellent sound insulation. Because the quality and types of timber used in today’s construction involve using layers of different materials, the result is a thinner wall that insulates sounds much more efficiently.
The durability of timber has made it one of the most popular building materials throughout history. With the proper engineering, good design, and correct finishing, timber doesn’t require chemical treatment to make it long lasting. When you look at some of the most beautiful Victorian-era homes that are still standing, and structurally sound, after hundreds of years, it is proof that good engineering, combined with the proper materials, is an unbeatable combination. Even without treatment, timber is resistant to many things that cause other materials to fail, such as frost, heat, and corrosion.
In general, a home or business constructed of timber is a good investment. The initial cost of construction is very budget friendly, and the building will have comparatively low maintenance and running expenses. The average life expectancy of a structure build from timber is 80 to 100 years (with many lasting much longer than that). When you integrate modern technology, such as air extraction, controlled ventilation, and even solar panels, you get a low-maintenance, cost efficient, and eco-friendly structure that will last well beyond your lifetime.
Laminates Engineering
Engineering is a term which can apply to a considerable variety of disciplines and/or fields. Some of the best-known fields would, of course, be industrial engineering, residential engineering, structural engineering, marine engineering and civil engineering. Nonetheless, as new technologies surface, so too do new fields of engineering. A good example would be marine engineering, a specialist discipline which has only been around for about 100 years. Another prime example would be laminates engineering, a specialist field which has witnessed a phenomenal amount of growth during the past two to three decades.
Laminates Engineering:
A Remarkable Display of Teamwork
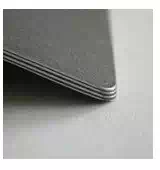
One of the most fascinating things about engineering, is the fact more often than not, engineers from a wide range of fields have to come together in order to successfully complete large engineer’s projects. If we take a cruise ship for example, we can get a clear picture of this remarkable teamwork. We have design engineers; structural engineers; marine engineers; laminates engineers, and even safety engineers, to name only a few. Even a small lapse in communication between the various disciplines could result in a catastrophe, or at best, a massive financial loss. Each department is responsible for choosing the best possible materials for the work they are involved in. The Core building materials in engineering are often said to be the backbone of a construction project and, as such, selection of these materials should be left in the hands of those who best understand them.
What Role Do Laminates Play in Our Modern World?
The most common and most well-known laminates would be those which are routinely used in the manufacturing of furniture and flooring. In developed countries, most homes built or refitted during the past decade or two will have at least a certain amount of laminated furniture or other fitting. Quite often, this could, for example, include basic furniture and fixtures such as kitchen cupboards; work tops, and etc.
Laminate flooring has also become immensely popular in recent years, largely to steady progress in the field of laminates engineers. When laminate flooring was first introduced, it soon gained an undesirable reputation since it was not only costly, but also lack the sort of durability that one sees with good quality hardwood flooring. Today, however, laminated flooring is incredibly robust and just as durable as any sort of wooden flooring. Despite the significant improvement in quality, the cost of laminated flooring has remained remarkably consistent.
If we move beyond our homes, and we look to large commercial buildings, including all modern skyscrapers, we can once again see how widely used laminates have become. Go into any multi-story building and you will see laminate surfaces everywhere, from office partitions to desks to the interior of covering inside elevators. Even windows in these huge skyscrapers are made from laminated glass in order to significantly enhance their strength. In short, laminates are today just as much a part of construction as what any other materials are, and the use of laminated materials is likely to increase even further as laminates engineering advances.
Laminates Engineering in The Shipbuilding Industry
For many decades, boat builders have made use of laminating, and particularly when it comes to strengthening the stem of a small dinghy and etc. In fact, traditional boat builders still use this and other similar techniques when they build small boats. In large vessels, laminates are typically used for the same purposes as they are in commercial and residential building.
In more recent times, however, laminates engineering has produced a remarkable material known as Fiber-Metal Hybrid Laminate Material. Many experts in the field believe that this new material may soon replace the use of regular steel completely in the shipbuilding industry. The reason for this is because it’s lighter than the steel used for ship building, thereby reducing fuel consumption while at the same time allowing for greater speeds.
Another extremely attractive advantage of this material is the fact that it can significantly reduce, or even eliminate the problem of corrosion altogether. While there aren’t currently any ships made entirely from Fiber-Metal Hybrid Laminate Material, it has attracted a great deal of attention from the naval construction industry and from those involved in oceanic engineering.
The Crucial Role of Laminates in Space
Laminate engineering has played a tremendous role in space exploration, and in actual fact, without the use of advanced laminated materials, space exploration as we know it today would essentially be doomed. If we look at the now retired space shuttle fleet, we can immediately see several examples of laminated materials being used. The most glaring example being the heat shield which protects the ship from the incredible temperatures encountered during re-entry through the earth’s atmosphere.
Another astonishing example would be the laminated assemblies which are fitted inside the throat of a craft’s booster rockets. The shuttles as well as most other types of spacecraft also rely on “Nano web” laminates for closed ventilation systems. With this in mind, it is easy to appreciate just how advanced laminates engineering has become over the last few decades.
No Room for Error
While the manufacturing of laminate flooring or laminate work surfaces for kitchens might not require any sort of advanced laminates engineering, it’s a whole different ball game in other industries that rely on laminate technology. From ocean-going passenger liners to nuclear submarines; from giant airliners to stealth fighter jets, technologically advanced laminates represent an almost endless number of opportunities. In truth, laminates are one of the core building materials used in engineering projects all over the world.
Given the massive risk factors present in some field, laminates engineering cannot allow any room for error. Only the most skilled engineers should be consulted, and likewise, only the finest materials should be used, even in applications where human safety is not a relevant issue. Even something as straightforward, and as simple as laminated flooring, should be left to the professionals. A poorly designed laminate floor might last a few years whereas a good quality laminate floor could last a lifetime.