Apparent density of a metal powder, or the weight of a unit volume of loose powder expressed in grams per cubic centimeter, is one of the fundamental properties of a powder. This characteristic defines the actual volume occupied by a mass of loose powder, which directly affects processing parameters such as the design of compaction tooling and the magnitude of the press motions required to compact and densify loose powder.
In most compacting operations, dies are filled by volume measure, and presses operate either to a fixed position or a fixed pressure. If the press operates to a fixed position, pressure can be maintained at a constant level only if the apparent density of the powder does not change. If, however, the press operates to a fixed pressure, consistency in apparent density is necessary to ensure compacts of equal height. Small fluctuations in apparent density can be compensated for by adjustments of pressure or stroke of the presses, but large-scale compacting requires that the apparent density of the powder be controlled within close limits.
Factors Affecting Apparent Density. Apparent density of a metal powder depends on the density of the solid material, particle size, particle size distribution, particle shape, surface area and roughness of individual particles, and particle arrangement. Apparent density is strongly affected by particle size. It generally (1) decreases with decreasing particle size, (2) decreases as the particle shape becomes less spherical and more irregular, (3) decreases with increasing surface roughness, and (4) is frequently controlled by mixing various sizes of particles.
Particle Size. Decreasing particle size generally decreases apparent density. The smaller the particles, the greater the specific surface of the powder. This phenomenon increases the friction between particles and subsequently decreases the apparent density. Powder particles that exhibit very low friction because of their rounded shape, such as gas-atomized (spherical) stainless steel powder, do not demonstrate this characteristic. The effect of decreased particle size on density is particularly significant for particle sizes of less than 20 /’m. Table 1 shows the effect of particle size on apparent density for several metal powders.
Table 1 Effect of particle size on apparent density for several metal powdersMaterial | Average particle diameter’3′, /’m | Apparent density, g/cm3 |
Aluminum | ||
Atomized | 5.8 | G.62 |
6.8 | G.75 | |
15.5 | G.98 | |
17.0 | 1.G4 | |
18.0 | 1.G9 | |
60% above 44 (+325 mesh) | 1.22 | |
75% above 44 (+325 mesh) | 1.25 | |
Copper | ||
Electrolysis | 90% min, -325 mesh | 1.5-1.75 |
Hydrometallurgical | 81.9%, -325 mesh | 1.69 |
Oxide reduced | 95% min, -325 mesh | 2.1G-2.5G |
Hydrometallurgical | 49.1%, -325 mesh | 2.42 |
Oxide reduced | 50-65%, -325 mesh | 2.65-2.85 |
Electrolysis | 60-75%, +100 mesh | 4.G-5.G |
Atomized | 70% min, -325 mesh | 4.9-5.1 |
50-60%, -325 mesh | 4.9-5.5 | |
Nickel | ||
Carbonyl | 3.2 | 0.61 |
Precipitation | 3.5 | 1.81 |
Carbonyl | 3.8 | 1.87 |
4.1 | 2.10 | |
Precipitation | 4.4 | 2.09 |
8.0 | 2.60 | |
-40+325 mesh | 3.60 | |
Tungsten | ||
Oxide reduced | 1.20 | 2.16 |
2.47 | 2.52 | |
3.88 | 3.67 | |
6.85 | 4.40 | |
26.00 | 10.20 | |
Stainless steel | ||
Atomized, spherical | -325 mesh | 4.3 |
-270+325 mesh | 4.5 | |
-200+270 mesh | 4.4 | |
-150+200 mesh | 4.5 | |
-100+150 mesh | 4.5 | |
Iron | ||
Reduced | 6 | 0.97 |
Carbonyl | 7 | 3.40 |
Reduced | 51 | 2.19 |
Electrolytic | 53 | 2.05 |
63 | 2.56 | |
Reduced | 68 | 3.03 |
Electrolytic | 78 | 3.32 |
(a) From Fisher subsieve sizer for single values and screens for size fractions
(a) From Fisher subsieve sizer for single values and screens for size fractions
Particle Shape. As particle shape becomes less spherical, apparent density decreases, due to both the increase in frictional surface area and less uniformity of powder particles during packing. Spherical powders, which are normally produced by atomizing, frequently have high apparent densities, about 50% of the density of the wrought metal. Spheres are most likely to pack without bridging or arching to create empty spaces; they tend to move easily past each other because of their smooth surfaces. At the other extreme in particle shape are flake powders, which often have apparent densities less than 10% of the wrought density. These powders are useful primarily as pigments, because their low apparent density aids in obtaining mixtures in paint.
Most powders used for compacting have irregular, somewhat equiaxed particle shapes with apparent densities that fall in the range between those of spherical and flake powders. Apparent densities of these particles range from 25 to 35% of the wrought density of the metal. Figure 13 illustrates the effect of particle shape on apparent density.
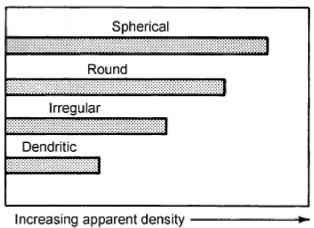
Fig. 13 Effect of particle shape on apparent density of a metal powder
Surface Roughness. Decreasing surface area-to-volume ratios and decreasing surface roughness tends to reduce frictional forces between settling particles. This tendency thus increases apparent density by allowing the particles to move more effectively to fill the free spaces between previously settled particles.
Particle Size Distribution. An effective way to increase the apparent density of a powder is to fill the spaces between particles with smaller particles. Figure 14 shows the effects of adding differently shaped -325 mesh powder to a standard +325 mesh blend of stainless steel powder. Table 2 shows this effect for mixtures of fine and coarse spherically shaped stainless steel powders, where a mixture of about 60% coarse and 40% fine particles is optimal.
Table 2 Effect of mixture of spherical coarse and fine stainless steel particles on apparent densityParticle | Particles, % | |||||
size (mesh) | ||||||
-100+150 | 100 | 80 | 60 | 40 | 20 | |
-325 | 20 | 40 | 60 | 80 | 100 | |
Apparent density, g/cm3 | 4.5 | 4.9 | 5.2 | 4.8 | 4.6 | 4.3 |
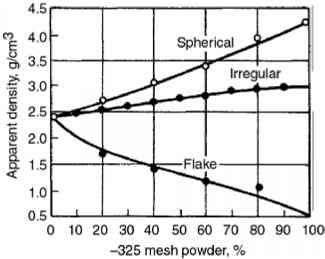
Fig. 14 Effect of three different shapes of -325 mesh powder addition to a +325 mesh distribution on apparent density of 316 stainless powder
The addition of fine spherical powder effectively increases apparent density, while the opposite is true of flake powders. Distribution of a variety of particle sizes greatly affects apparent density. The relative amount of coarsest and finest particles and the percentage of particles between the two extremes determine apparent density. An example of this is shown in Table 3 for three particle size distributions.
Table 3 Apparent densities and flow rates of electrolytic iron powders of three particle size distributions
Particle | Particles, | % | |
size (mesh) | Powder | Powder | Powder |
A | B | C | |
+100 | 4 | 3 | 15 |
-100+150 | 11 | 26 | 10 |
-150+200 | 18 | 18 | 30 |
-200+250 | 16 | 6 | 25 |
-250+325 | 18 | 16 | 5 |
-325 | 33 | 31 | 15 |
Apparent density, g/cm3 | 2.6-2.8 | 3.2-3.4 | 3.8-3.9 |
Flow rate, s/50 g | 29 | 24 | 20 |
Hall Flowmeter and Carney Funnel. The most common method for determining apparent density of metal powders uses the Hall flowmeter. Both ASTM B 212 and Metal Powder Industries Federation (MPIF) standard 04 describe this method.
Critical equipment dimensions are illustrated in Fig. 15(a), 15(c), and 15(d). Apparent density determinations are made by pouring powder into the funnel and allowing it to flow into the 25 cm3 (1.5 in.3) density cup. After the cup is fitted, the funnel is moved away and the excess powder is carefully leveled off using a spatula or straight edge. Care must be exercised to prevent physical densification of the powder in the cup when leveling. The apparent density in grams per cubic centimeter is then determined by weighing the powder in the cup in grams and dividing by 25 cm3 (1.5 in.3) (cup volume).
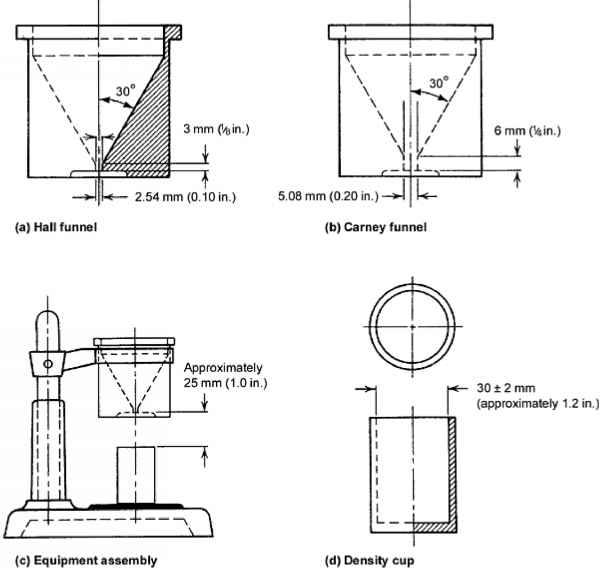
Fig. 15 Dimensions for apparent density equipment
For powders that do not flow freely, a second method, described in ASTM B 417 and MPIF 28, has been devised. This is similar to the Hall flowmeter procedure, except that a different funnel, the Carney funnel, which has an orifice diameter twice that of the Hall funnel, is used (see Fig. 15a and b). This larger opening permits a greater variety of powders to flow. Powders that do not flow readily can be freed by poking a wire up and down in the hole. The wire must not enter the density cup at any time. This second method is fast and correlates well with the Hall flowmeter evaluation of free-flowing metal powders.
A wire is not used with the Hall flow-meter funnel because it may scratch the orifice and ruin the calibration of the funnel for flow tests. The Carney funnel is often used when measuring apparent density of lubricated powders because lubricant adhering to the smaller orifice of the Hall funnel temporarily affects the calibration of the Hall flowmeter.
Scott Volumeter. Another instrument frequently used for determining apparent density is the Scott volumeter, described in ASTM B 329, which was originally developed by Scott, Schaeffer, and White for the determination of the density of dry pigment for paint. As shown in Fig. 16, the device consists of:
A large brass funnel with a metal screen and a smaller funnel with a straight stem for directing the powder into the baffle box
A baffle box with glass sides and two wooden sides containing a series of glass baffle plates and a funnel at the bottom to collect the powder and direct it into the density cup
• A square density cup with a capacity of l6.4± 0.032 cm3 (1 ± 0.002 in.3) or a cylindrical cup with a capacity of 25.00 ± 0.05 cm3 (1.5 ± 0.003 in.3) with an inside diameter of 30.00 ± 2.00 mm (1.2 ± 0.08 in.)
• A stand to support the funnels and baffle box concentric with the density cup, so that the bottom of the baffle box funnel is 19 mm (0.75 in.) above the top of the density cup when the apparatus is assembled
• A level, vibration free base to support the funnels and baffle box
• An analytical balance having a capacity of at least 100 g (3.5 oz) and a sensitivity of 0.1 g (0.0035 oz)
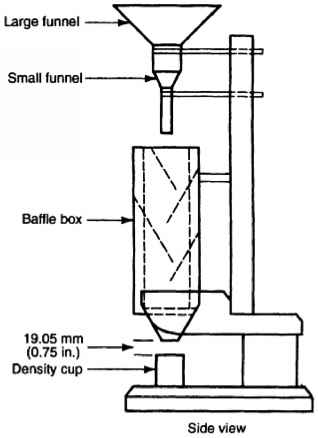
Fig. 16 Scott volumeter
Operating Procedure. The test specimen is carefully poured into the funnel. Ultrafine powders may require light brushing with a nylon brush to initiate powder flow through the screen in the funnel. Powder is allowed to run into the density cup until it completely fills and overflows the periphery of the cup. The funnel and baffle box should then be rotated approximately 90° in a horizontal plane to clear the cup.
Excess material should be removed from the cup by passing a spatula blade in flat contact with the top of the cup. The spatula is moved smoothly back and forth along the top of the cup until all excess powder has been removed. When insufficient powder is left for the first reverse pass to smooth the surface completely, powder on the spatula should be gently replaced on top of the cup. The spatula must be kept level at all times to prevent packing or pulling out of the powder.
After the leveling operation, the side of the density cup should be tapped lightly to settle the powder to avoid spilling. The powder is transferred to a balance and weighed to the nearest 0.1 g (0.0035 oz). The density of the powder in the density cup is given in grams per cubic centimeter if a metric cup is used, or grams per cubic inch if a nonmetric cup is used.
Arnold Meter. Another device developed to determine the apparent density of metal powders is the Arnold meter, described in ASTM B 703 and MPIF 48, which is designed to duplicate the action of a feed shoe filling a die cavity on a P/M press. A hardened, fully demagnetized steel block with a round hole having a volume of 20 cm3 (1.2 in.3) is placed on a sheet of glazed paper. A bronze bushing filled with powder is slid across the hole. The powder collected in the hole is then removed and weighed. Apparent density is calculated by dividing the weight by the volume of the hole.