Air Brake System is the brake system used in automobiles such as buses, trailers, trucks, and semi-trailers. George Westinghouse created air brakes for utilizing it in trains for railway service. A secured air brake was patented by him on 5th, March 1872. At first air brake is produced for use on trains and now it is used common in automobiles. Westinghouse made various modifications to enhance his creation, directing to several appearances of the automatic brake which was extended to include road vehicles.
Compressed Air Brake System– The Compressed Air Brake System is a different air brake used in trucks which contains a standard disc or drum brake using compressed air instead of hydraulic fluid. Most types of truck air brakes are drum units, though there is growing trend to the use of disc brakes. The compressed air brake system works by drawing clean air from the environment, compressing it, and hold it in high pressure tanks at around 120 PSI.
Whenever the air is needed for braking, this air is directed to the functioning cylinders on brakes to activate the braking hardware and slow the vehicle. Air brakes use compressed air to increase braking forces. The large vehicles also have an emergency brake system, in which the compressed air holds back a mechanical force using springs which will otherwise engage the brakes. If air pressure is lost for any reason, the brakes will hold and vehicle is stopped.
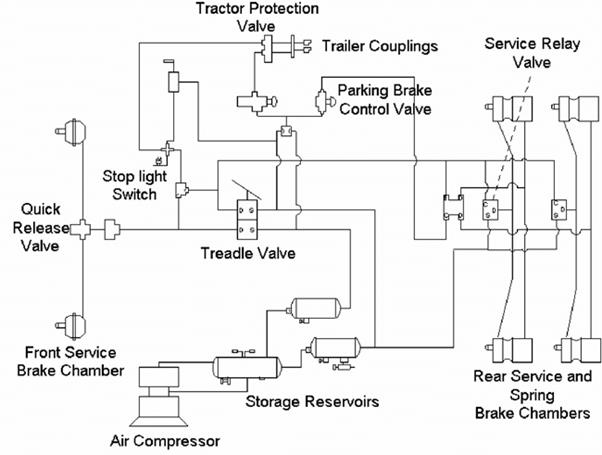
Design and Function– The Compressed air brake system is separated into control system and supply system. The supply system compresses, stores and provides high pressure air to the control system and also to other air operated secondary truck systems such as gearbox shift control, clutch pedal air assistance servo, etc.,
Control system– The control system is separated into two service brake circuits. They are the parking brake circuit and the trailer brake circuit. This two brake circuits is again separated into front and rear wheel circuits which gets compressed air from their individual tanks for more protection in case of air leak. The service brakes are applied by brake pedal air valve which controls both circuits. The parking brake is the air controlled spring brake which is applied by spring force in the spring brake cylinder and released by compressed air through the hand control valve.
The trailer brake consists of a direct two line system the supply line which is marked red and the separate control or service line which is marked blue. The supply line gets air from the main mover park brake air tank through a park brake relay valve and the control line is regulated through the trailer brake relay valve. The working signals for the relay are offered by the prime mover brake pedal air valve, trailer service brake hand control and prime mover park brake hand control.
Supply system– The air compressor is driven off of the automobile engine by crankshaft pulley through a belt or straightly off of the engine timing gears. It is lubricated and cooled by the engine lubrication and cooling systems. The Compressed air is initially directed through a cooling coil and into an air dryer which eliminates moisture and oil impurities and also contains a pressure regulator, safety valve and a little purge reservoir. The supply system is outfitted with an anti freeze device and oil separator which is an alternative to the air dryer. The compressed air is then stored in a tank and then it is issued through a 4 – way protection valve into the front and rear brake circuit air reservoir, a parking brake reservoir and an auxiliary air supply distribution point. The Supply system also contains many check, pressure limiting, drain and safety valves.