The name compression ring describes its function in the piston. These are sets of rings which can be easily identified as they occupy the top most position, above the oil scraper rings. These rings mainly seal against the pressure of the air being compressed. These have a good thermal expansion co-efficient. Thus the butts of these rings never meet during working conditions.
Be very careful when fitting a new piston ring onto a piston. If you are not careful, there is a chance of the ring being fitted up-side-down. If we look at the cross-section of the piston ring closely, there is a sealing edge provided and this side of the piston must be facing upwards. The manufacturer will provide some information for identifying the top side of the piston. Either the top area of the piston is marked as βTop” or some numbers are visible. Reference to the manufacturer’s manual is necessary before assembling piston rings onto a piston. (Please see the sketch below; click to enlarge and use the Back button in your browser to return to the same place on this page.)
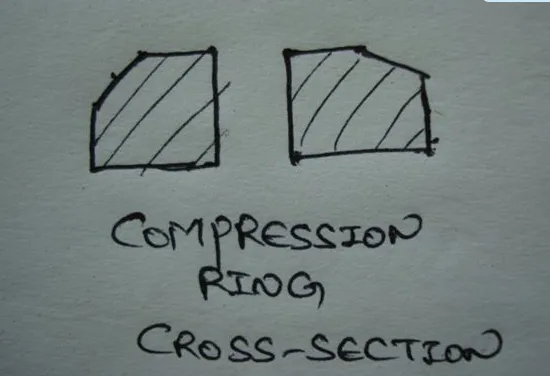
Oil Scraper Rings
Oil scrapers are sets of rings that are used solely for the purpose of scraping oil from the liner after the lubrication action is over. These rings are found usually close to the gudgeon pin area and right below the compression ring sets. A close-look up of the cross section of the oil scraper rings reveals that the edges of these rings are so sharp that they have the ability to scrape down the oil from the liner after the lubrication. The sharpness does not mean that they will cause harm to the liner during the scraping action.
Extensive care must be exercised when fitting the ring onto the piston; if fitted up-side-down, the oil carry over will increase drastically and might result in blowing of the delivery line when the line gets hot. The important point to note about these oil scraper rings is they have springs fitted inside the rings. To be clearer, they have springs fitted first onto the piston groove, and then the piston ring is fitted upon them. Thus the spring applies a force, so that the oil scraper ring is pressed against the liner, enabling it to scrape the oil down to the crankcase.
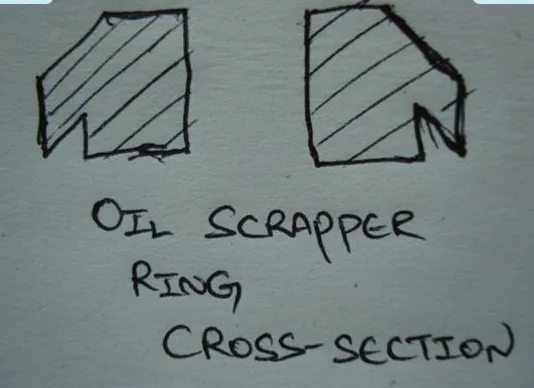
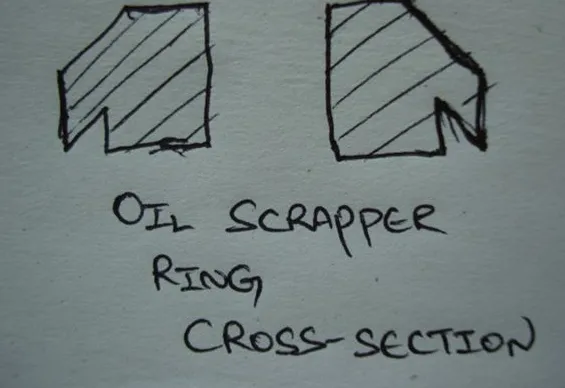
Connecting Rod:
The connecting rod of a reciprocating air compressor is one of the most important running gears. It connects the crank pin to the piston. The rotary motion of the crankshaft is converted into a reciprocating motion of the piston by the connecting rod. The type of motion of the connecting rod is very special and is called an articulating motion. Thus the connecting rod has another name, the articulating rod. The connecting rod upper end, which is connected to the pistonβs gudgeon pin, is known as the small-end and the end connected to the crank pin is called the big-end. These two ends have bearings, for easy and smooth transfer of motion between the mating parts. The bearing at the small-end is the small-end bearing and the other one is called the big-end bearing. The small end bearing is usually shrunk-fit, whereas the big end bearing is a removable, shell type, half-split, white metal bearing.
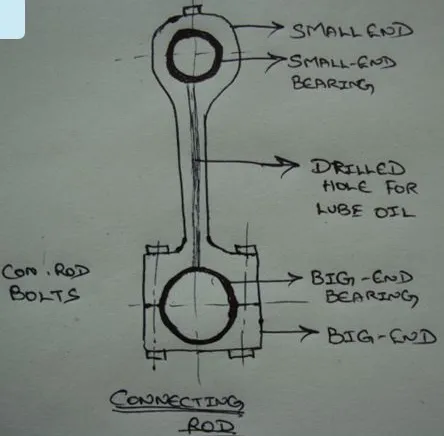
If the compressor is of the forced lubrication type, then usually the connecting rod will have a drilled hole through its center where the oil reaches the small-end bearing from the big-end bearing. Thus the connecting rod has a lube oil passage, eliminating the need for external piping arrangements.
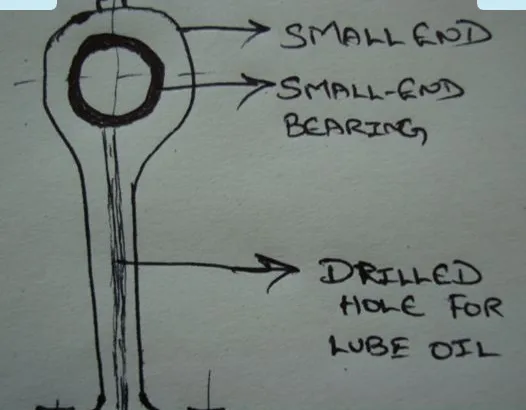
The bottom end of the connecting rod is split into two equal parts, or sometimes split at an angle. This is to enclose the crankpin of the crankshaft within it. The bottom part of the bottom end is fixed with the crankpin in between. The connecting rod bolts are tightened, thus making the bottom-end act as one unit.
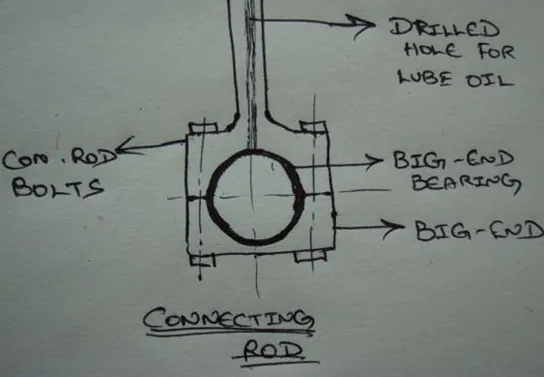
Crankshaft:
The crankshaft can be called the spine of any reciprocating machinery. The size and length of the crankshaft depends on the type of the air compressor. The crankshaft has three important parts jointed together or fabricated from the same piece. They are
1. Crankpin
2. Crank web
3. Journal
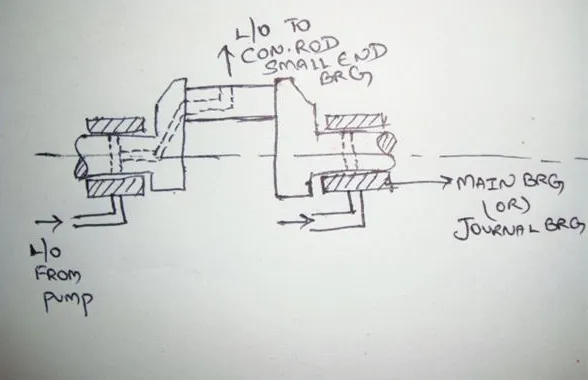
Looking at the attached image, the main journal is the one which rests on the main bearing. It forms the center line of the crankshaft. The crank web are the appendices, projecting outside the center line of the crankshaft, giving way to support the crank pins, which are connected to the connecting rod.
The crankshaft has one end connected to the drive, which may be either an electric motor or diesel engine. The other end is usually a blind with a shaft seal and a journal bearing. The end which is connected to the drive usually has a flywheel attached to it. The flywheel in turn is attached to a flexible coupling.
Lubrication System
This system is applicable only to those types of compressors that employ forced lubrication. The compressor crankcase forms an inherent oil sump; where some calculated amount of oil is available as a reserve even after the oil is under work, i.e. lubrication. The lube oil is drawn by the lubricating oil pump, which is driven or an attached pump with the crankshaft. The pump takes suction from the inherent lube oil sump of the compressor, and it supplies oil under pressure to a common manifold, from where the oil is routed to each main journal bearing and enters the drilled hole on the crankshaft after lubrication of the main bearing. After entering the drilled hole, the oil moves towards the crank pin, via the crank web, and thus lubricates the bottom end bearing of the connecting rod. After lubrication, some of the oil climbs up the drilled hole in the connecting rod and thus reaches the small end bearing, thus lubricating the gudgeon pin and related moving parts. The oil after lubrication falls down into the crankcase sump.
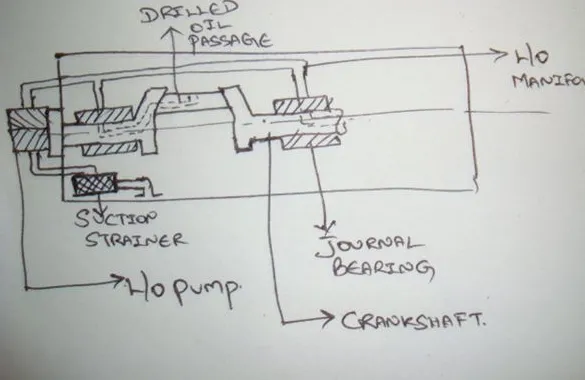
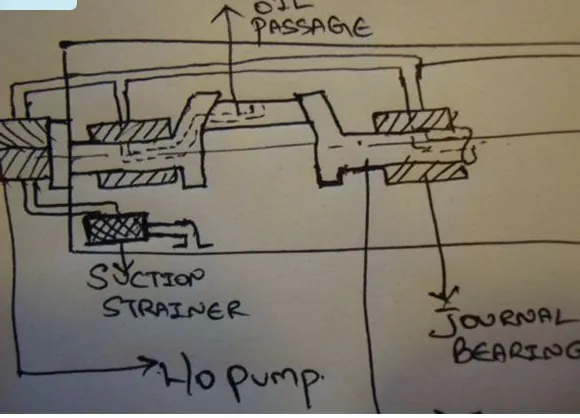