Calculations for heat exchanger designs use heat transfer parameters such as convection heat transfer coefficients, overall heat transfer coefficients, and log mean temperature differences. These calculations are needed for shell and tube and double pipe heat exchangers, as well as other types.
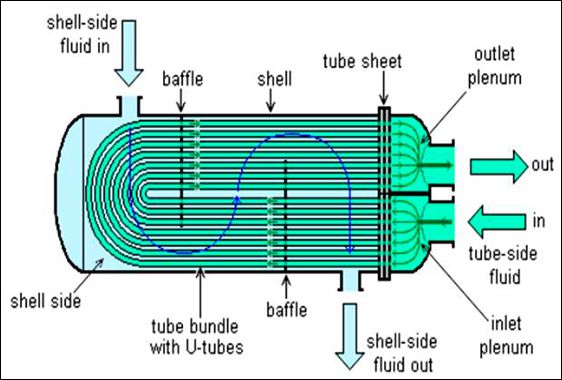
Types of Industrial Heat Exchangers
There are many types of heat exchangers used in a wide variety of industrial applications including power plants, boilers for industrial steam, chemical plants, and many types of manufacturing facilities. Several different configurations are used to accomplish the basic function of transferring heat from one fluid to another without mixing the two fluids together. The types of heat exchangers described and discussed in these articles include the two most common industrial heat exchangers, the shell and tube heat exchanger and the double pipe heat exchanger, along with information about spiral heat exchangers, flat plate heat exchangers, fin-tube heat exchangers, and condensers.
· Types of Shell and Tube Heat Exchangers
· Characteristics and Design of Double Pipe Heat Exchangers
· A Fin Tube Heat Exchanger Gives Good Air Heat Exchanger Efficiency
· Features and Characteristics of the Spiral Heat Exchanger
· Features and Characteristics of the Flat Plate Heat Exchanger
· How Does a Compact Flat Plate Heat Exchanger Work?
· The Purpose of a Condenser and Its Different Types
Heat Transfer Coefficients and Heat Transfer Fundamentals
Convection heat transfer coefficients and log mean temperature differences are needed for heat exchanger design calculations. Natural convection heat transfer coefficients are calculated using a correlation of dimensionless numbers, typically Nusselt number in terms of Grashof number and Prandtl number. Forced Convection heat transfer coefficients are calculated from correlations of Nusselt number in terms of Reynolds number and Prandtl number. These articles provide information, equations and example calculations for natural convection and forced convection heat transfer coefficients, overall heat transfer coefficients and log mean temperature differences. There is also information about heat exchanger flow patterns and equations and calculations for combined convection and conduction heat transfer.
· Calculations for Overall Heat Transfer Coefficient Estimatiion with Excel Spreadsheets
· Excel Spreadsheets for Natural Convection Heat Transfer Coefficient Calculations
· Calculation of Forced Convection Heat Transfer Coefficients with Excel Spreadsheets
· Calculation and Significance of Log Mean Temperature Difference
· Combined Thermal Conduction and Convection Heat Transfer Calculations
· Counter Flow, Parallel Flow, and Cross Flow Heat Exchanger Flow Patterns
Heat Exchanger Design – Theory and Calculations
Heat exchanger design is an iterative process. A preliminary value for the required heat transfer area can be calculated using an estimate of the overall heat transfer coefficient together with information about the required rate of heat transfer, the flow rates of the two fluids, and the inlet and outlet fluid temperatures. Preliminary details of the heat exchanger can then be calculated, including items such as diameter, length, and number of tubes for a shell and tube heat exchanger, diameter and length of the shell, number of tubeside passes, and number of shellside passes. The allowable pressure drop across the heat exchanger can also be calculated and used in the preliminary design. With a preliminary detailed design completed, a better estimate of convective heat transfer coefficients and the overall heat transfer coefficient can be made and adjustments can then be made to the preliminary detailed design as necessary. The use of Excel spreadsheets for the preliminary design calculations is included in some of these articles.
· Fundamentals of Heat Exchanger Theory and Design
· Use of Excel Spreadsheets in Preliminary Heat Exchanger Design Calculations
· Preliminary Heat Exchanger Design Example
· Shell and Tube Heat Exchanger Design
· Excel Formulas for Pressure Drop in Shell and Tube Heat Exchanger Design
· Designing an Air to Air Heat Exchanger
Heat Exchangers on Ships
Heat exchangers are used on ships in the power production process, such as for diesel engines, boilers, and economizers, as well as in production of steam for accommodation and deck equipment. The heat exchangers used include common types used as industrial heat exchangers, such as the shell and tube heat exchanger, the plate heat exchanger, and the fin tube (radiator) type.
· Uses of Heat Exchangers on Board Ships
· A New Innovation – Plate Heat Exchangers for Ships Engines
· A Ship’s Boiler Steam Supply for Accommodation and Deck Equipment
· Marine Boiler Auxiliaries, Fixtures and Fittings
· Understanding the Basic Steam Installation System on a Diesel Ship
· Economizer Use with Marine Boilers
Heat Exchangers in Everyday Life
Although most people are not aware of them, heat exchangers are very prevalent all around us in our everyday life. For example, heat exchangers are crucial to operation of furnaces, air conditioning systems, refrigerators and freezers. Automobiles require a heat exchanger in the form of the radiator to provide cooling for the engine and a smaller one for heating of the passenger cabin. High performance engines use heat exchangers in turbochargers.
· Heat Exchanger Types and Their Use in Everyday Life
· Introduction to Air Furnaces – History and Types
· Ground and Air Source Heat Pumps and How They Work to Heat Your Home
· Evaporators for Refrigeration and Air Conditioning Applications
· Types of Heat Exchangers Used in HVAC Systems
· Understanding the Parts that Make up an Engine Cooling System
· How Do Turbochargers Work in an Automobile Engine?