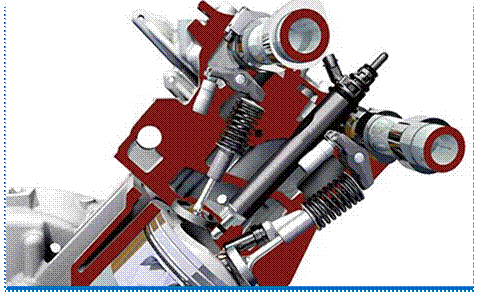
Improving internal combustion engine efficiency is a prime concern today. Engineers have devised many methods like turbocharging, cam-less engines, direct fuel injection, VIT, regenerative braking, etc. In this article we discuss the factors limiting the efficiency of ICE and ways to increase it.
Increasing Efficiency
● There is a lot of concern nowadays about the efficiency of the internal combustion engine (ICE), and a lot of research is being done to improve it. But what exactly is the efficiency of the internal combustion engine and how do we measure it? The efficiency of any engine is simply calculated from the energy of the fuel supplied per unit time to do work and the output at the shaft of the engine after subtracting all losses. The input power of the fuel can be obtained from the mass of the fuel and its calorific value. The shaft output can be measured from a brake dynamometer. Simply put efficiency is Output/Input. The average ICE has an efficiency between 20 to 30%, which is very low.
● If we see a heat balance sheet of the internal combustion engines for a spark ignition or gasoline engine we find that the brake load efficiency is between 21 to 28%, whereas loss to cooling water is between 12 to 27%, loss to exhaust is between 30 to 55 %, and loss due to incomplete combustion is between 0 to 45%.
● Similarly when we analyze the heat balance sheet of a compression ignition or diesel engine we find that it has a brake load efficiency between 29 to 42 % and loss to cooling water is between 15 to 35 %, losses to exhaust is between 25 to 45 %, and losses due to incomplete combustion is 0 to 5 %.
● By analyzing the two heat balance sheets we find that in Gasoline engines loss due to incomplete combustion can be rather high. In this article we discuss the various technologies and methods that may be employed to increase the efficiency of Internal Combustion Engines as well as automobiles.
Heat Balance Sheet
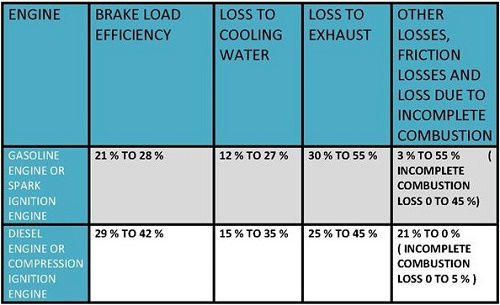
Factors Limiting the Efficiency of Internal Combustion Engine
● By analyzing the heat balance sheet we find that the factors limiting the efficiency of an internal combustion engine are as follows:
○ Heat losses during cooling of engine.
○ Heat losses in exhaust gases.
○ Friction loss
○ Transmission efficiency losses. Losses in clutches and fluid couplings, etc.
○ Friction losses in tires. Tire selection is a compromise between safety, stability, and performance. A safer tire will give a minimum braking distance, good stability, less skidding, but less fuel efficiency. A tire having less surface contact and more of a line contact will be fuel efficient, but unsafe.
○ Losses due to incomplete and imperfect combustion. Perfect combustion would result in the production of carbon dioxide and water.
○ Loss due to braking
○ Losses due to viscosity of lubricating oil.
○ Compression ratio. The higher the compression ratio the higher the thermal efficiency. As in spark ignition or gasoline engines the compression ratio is limited by pre-ignition (not in compression ignition or diesel engines), the diesel engines are about 30% more efficient than gasoline engines.
○ Drag of the vehicle
○ Imperfect valve timing
○ Losses in driving cam shafts
○ Energy consumed by auxiliaries like water pumps and oil pumps
Carnot’s Theorem for Efficiency
● The second law of thermodynamics states it is impossible to construct an engine which will work in a complete cycle and produce no other effect except the raising of a weight and the cooling of a heat reservoir. Thus it there is a limit to the thermal efficiency of heat engines.
● Sadi Carnot, a French military engineer had studied the second law and stated that, “ No heat engine working in a cycle between two constant temperature reservoirs can be more efficient than a reversible engine working between the same two reservoirs.” Thus the maximum efficiency any heat engine can have is by using the Carnot’s cycle (two reversible isotherms and two reversible adiabatic). The Carnot limit is the maximum efficiency any engine can have. To date the highest efficiency which has been obtained is 52% in a Maritime diesel engine of 90,000 horsepower.
Methods and Technology for Improving Internal Combustion Engine Efficiency
● The practical methods and new technology that help in increasing the efficiency of the internal combustion engines are as follows:
○ Regenerative braking: As braking a car or automobile wastes the kinetic energy in the form of heat, regenerative braking is ideal method when you want to brake your vehicle to control speed (like when going downhill). In this electromagnetic braking is done as small motors absorb the energy and convert it into battery energy.
○ Variable Injection Timing: This is already used in Maritime engines. At low loads and speeds, the injection is advanced allowing same mean effective pressure to be maintained. This not only increases the efficiency of the engine as the scavenge pressure is maintained, it also allows for lower quality fuel to be burnt.
○ Variable valve timing: In this method the exhaust and inlet valves opening and closing time can be varied, affecting the efficiency of the engine. This method can increase the efficiency by 4 to 5%.
○ Cutting off cylinders: In large engines in cruising or going downhill, half of the cylinders can be cut off thus reducing fuel demand. It cannot be done on small engines as the engine would become rough.
○ Turbochargers: A turbocharger is an exhaust gas recovery device that increases boost air pressure thereby optimizing combustion. It increases efficiency by 7 to 8%.
○ Direct Fuel Injection: In previous engines, the fuel was mixed with air and injected, but nowadays fuel is directly injected into the combustion chamber and mixing takes place according to the profile of the combustion chamber. It increases efficiency by 11 to 13%.
○ Twin spark plugs and multiple injectors: As the flame front starts from the spark plug and proceeds outward, some fuel remains unburnt as ejected before the flame front can reach it. In a twin spark plug cylinder two flame fronts are created, causing better combustion.
○ Using the correct viscosity of lubricating oil, as viscous oil can result in losses due to friction.
○ Integrated starter and generator systems: In this system the engine is immediately stopped when idling and started when the accelerator is pressed.