2.1 CRUDE OIL ANALYSIS
Crude petroleum oil is a mixture of hydrocarbons. The hydrocarbon gases, methane, ethane, propane, and butane, are present in crude oil in its dissolved state. Methane has a high vapour pressure and it escapes from crude oil unless pressure above the vapour pressure is maintained. Usually it separates out from crude oil itself from the well and is collected separately as natural gas and a trace of it may be found in crude oil under atmospheric pressure. Though ethane has a higher vapour pressure than propane and butane, traces of it are usually found in crude oil right from the well. Propane and butane are present in the liquid state at slightly above atmospheric pressure owing to their low vapour pressure and high solubility in crude oil. The propane–butane mixture is separated from crude oil and is used as liquifi ed petroleum gas (LPG). The remaining liquid hydrocarbons can be separated as boiling fractions such as naphtha cut (boiling up to 140°C), kerosene cut (boiling between 140°C and 270°C), gas oil or diesel cut (boiling between 270°C and 350°C), by heating and vaporising the crude oil by a gradual increase in temperature followed by collection after condensation. When crude oil is heated in a distilling fl ask, vapours start emanating as the temperature rises and these vapours are collected after condensation using ice cold water. The temperature of vapour giving the fi rst drop of condensate is reported as the initial boiling point (IBP), which may be above or below 0°C depending on the presence of the lowest boiling hydrocarbon in crude. This vaporizing phenomenon is so fast at the beginning that temperature measurement is quite uncertain as the vapour of the fi rst drop is immediately followed by the mixture of vapours with increasing boiling points, hence this must be noted in the shortest possible period (within 5–10 min) after the charge is heated. As heating is continued, more and more hydrocarbon vapours with increasing boiling temperature are separated from crude and collected as condensates. This process is continued with gradual heating until no further vaporisation takes place. The vapour temperature and the volume of liquid condensates (boiling fractions) collected are measured and reported as the distillation analysis of crude oil. In the laboratory, such a batch distillation is carried out for a specifi ed amount of crude oil (500 cc, 1 litre or more). During distillation at atmospheric pressure, the rate of vaporisation decreases gradually after 40–45% of crude is distilled and, fi nally, negligible or no vaporisation takes place. If attempts are made to increase the temperature by further heating, the residual crude in the fl ask may undergo thermal cracking (break down of hydrocarbon compounds present originally in the charge), which is a reaction phenomena other than distillation. Alternatively, when heating of the residual oil is continued under vacuum, vaporisation is restored and condensates are collected. Distillation, in fact, is done at atmospheric pressure and then followed under vacuum. The separation of hydrocarbons can be improved if the vapour and its condensates (refl ux) are in intimate contact for some time during distillation and a reproducible distillation analysis is possible. Such a method of distillation is known as true boiling point (TBP) distillation. A refl ux ratio of 5:1 is usually sought as the standard separation. Separation of fraction by 1% volume can be obtained at a very close temperature difference and such a close separation is comparable with a distillation tower of 10–12 plates. A routine crude distillation test is carried out in a standard TBP distillation apparatus in a packed column of specifi c size and packing material with a certain amount of refl ux ratio (refl ux/vapour ratio). A TBP apparatus is shown in Figure 2.1 and a typical TBP analysis curve is shown in Figure 2.2. Usually, the composition of crude oil varies from well to well and it is essential to have a separate TBP analysis for each batch of oil purchased before refi ning. Hence, the yields of light to heavy fractions will vary from crude to crude. A small variation in TBP analysis may have a wide variation in the chemical constituents of the boiling fractions. This analysis indicates the maximum possible yields of raw cuts of products that could be obtained by distillation. In a refi nery, a distillation column is used to separate these cuts in large rates continuously, where the yields of the raw cuts are slightly different from the TBP analysis. In fact, a distillation column is designed on the basis of the TBP analysis of a crude oil. Crude oils having wide difference in TBP analysis cannot be distilled in the same column without sacrifi cing the yields
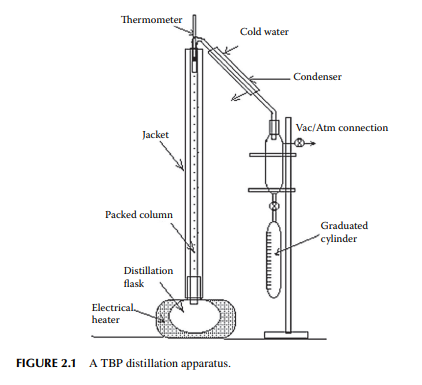
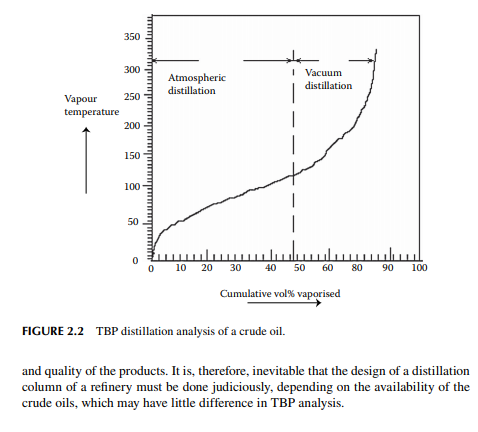
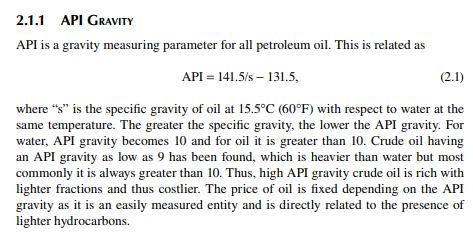
2.1.2 CHARACTERISATION FACTOR
The next entity is the characterisation factor (CF), which is most commonly used with API gravity to judge the quality and many physical properties of crude oil and its products. This is defi ned as the ratio of cubic root of the molal average

2.1.3 BOTTOM SEDIMENT AND WATER
Bottom sediment and water (BSW) is a measure of the quantity of residual sediment mostly settleable from the crude oil (if suffi cient time is allowed for settling) and water. This may contain both heavy asphaltic hydrocarbon oil and non- hydrocarbons, such as inorganic salts. An amount of BSW is routinely tested for every batch of crude oil received in a refi nery. Water, salt, and sediment are removed from the storage tanks, followed by electrical desalting. Throughout the world, petroleum products are tested according to the methods and equipment specifi ed by the American Standard for Testing Materials (ASTM). Detailed testing procedures are available from the ASTM handbooks for testing petroleum products. Some of the common properties and an outline of the testing methods for petroleum products are presented in the following sections.
2.2 DOMESTIC FUELS
2.2.1 LIQUIFIED PETROLEUM GAS
Liquifi ed petroleum gas (LPG) is a mixture of propane and butane in liquifi ed form at a pressure of about 10–15 atm, depending on the proportion of the components present. This is the fi rst product of distillation from crude oil. Raw hydrocarbon gases contain sulfurous hydrocarbons, which may be odorous and corrosive. Hence, treatment of these gases is carried out to remove unwanted impurities, such as mercaptans, hydrogen sulfi de associated with the gases, and moisture. LPG is tested for its quality as required by its use as a domestic cooking gas. One of the simplest tests of LPG quality is the weathering test (Figure 2.3). In this test, 100 mL of liquid LPG is kept in a test tube with a mercury-in-glass thermometer dipped into it. Liquid LPG starts vaporising through the open mouth
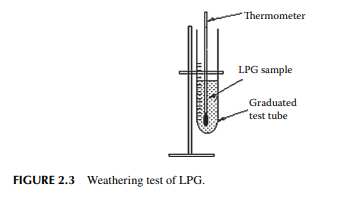
of the test tube to the atmosphere, causing the temperature to fall rapidly. After 95 mL of liquid is vaporised, the residual liquid temperature is noted. If the temperature is very low (below 0°C), then the proportion of propane in the mixture is more and if it is high (above 2°C), then the proportion of butane will be more. For domestic use, the maximum weathering temperature should be 2°C. Slightly lower than this temperature may be useful, but the carrying capacity in the cylinder will be reduced. Whereas, higher than this temperature should not be acceptable because incomplete vaporisation may occur at a low ambient temperature (e.g., in winter or in hilly places like Darjeeling). In order to avoid excessive pressure in the fi lled cylinder for the required mass (usually 14.2 kg for domestic cylinders) it is required to test the vapour pressure of LPG at a temperature slightly above room temperature. This is measured in a high-pressure vessel (known as a Reid vapour pressure vessel) fi tted with a pressure gauge and a constant temperature bath with a thermometer. The experiment is known as Reid’s vapour pressure test and the pressure measured is reported as Reid vapour pressure (RVP). Domestic LPG has a maximum RVP of 8 kg/cm2 at a temperature of 37.8°C. A RVP measuring arrangement is shown in Figure 2.4. In fact, commercial LPG may not have a uniform composition of only propane and butane, but may contain an amount of lighter gases in traces and also contain some olefi nic gases obtained from petrochemical plants. The presence of mercaptans and hydrogen sulfi de causes corrosion to vessels, pipelines, and joints, which may be further aggravated by the presence of moisture. LPG is tested for its corrosive properties by the copper strip corrosion test. In this test, a standard polished copper strip is dipped into liquid LPG in a thick-walled small vessel, known as a bomb, kept at a constant temperature, usually 30°C. After 1 h (or maybe more depending on its end use), the bomb is opened and the copper strip is removed and compared its brightness of surface against a set of standard copper strips indicating different degrees of corrosion as ASTM 1, 1a,1b, 2, 2a, etc. The desired specifi cation is that the surface brightness of the strip under study should not be any worse than ASTM 1. Hydrogen sulfi de in LPG is usually not present in the domestic cylinder. As, in the refi nery hydrogen sulfi de is removed from hydrocarbon gases by absorption in a solvent (usually in diethyl amine, DEA). Traces of hydrogen sulfi de and mercaptan can
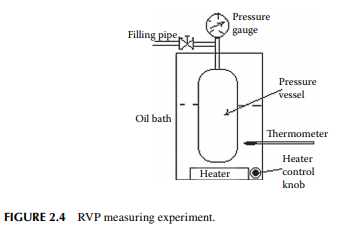
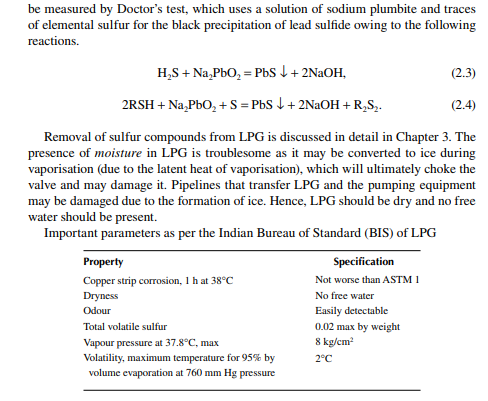
2.2.2 KEROSENE
Kerosene or superior kerosene oil (SKO) is another domestic fuel mainly used for lighting or lamp oil. It is also used as a domestic stove oil. It is a petroleum product that boils in the range of 140°C–280°C and is available from crude petroleum oil. It is heavier than naphtha or petrol (motor spirit, MS), but lighter than diesel oil. The major properties of kerosene that determine its burning quality are the smoke point and the fl ash point.
2.2.2.1 Smoke Point
The smoke point is determined as the height of the fl ame (in millimetres) produced by this oil in the wick of a stove or a lamp without forming any smoke. The greater the smoke point, the better the burning quality. Domestic kerosene should have a smoke point of 20 mm (minimum). This is measured in a standard testing apparatus consisting of a standard lamp with a wick of specifi ed dimension and mass. In this apparatus, a mirror is provided to position the fl ame in the centre such that the straight height of the fl ame can be measured in a graduated scale. Smoke is produced mainly due to the presence of carbon and heavy hydrocarbon particles in the fl ue gas. The presence of aromatic hydrocarbons contributes carbon atoms when burnt. In the refi nery, aromatic hydrocarbons are removed by extraction to a desirable extent so that the smoke point becomes greater or near 20 mm. A smoke point testing apparatus is shown in Figure 2.5.
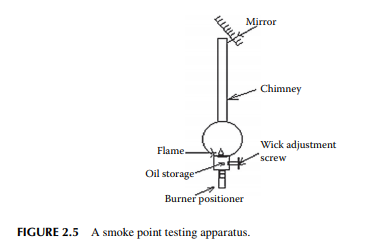
2.2.2.2 Flash Point
The fl ash point is defi ned as the temperature of the oil at which it momentarily fl ashes in the presence of air and the igniting source. For domestic kerosene, it should not be below the ambient temperature. In India, this value is 35°C (minimum). This is determined in the laboratory using a standard cup, standard fl ame, and under standard atmospheric conditions. There are two standard test methods for measurement—the open cup method (Abel’s method) and the closed cup method (Pensky–Mertinus method). In either test, oil is taken in a closed container provided with a stirrer and a heater as shown in Figure 2.6. The temperature of the oil in the bath is measured by a thermometer. The oil is heated at the rate of 5°C–6°C per minute and a standard fl ame is introduced every 30 sec. The temperature at which a momentary fl ash occurs is noted as the fl ash point.
2.2.2.3 Char Point and Bloom
Other burning qualities of kerosene are char point and bloom formation. Char point is defi ned as the coke and ash left on the wick after complete burning of the oil. For domestic kerosene, the maximum amount of char allowed is 20 mg/kg of oil burnt. If the oil contains more aromatics, more organic char may be found. Bloom is the
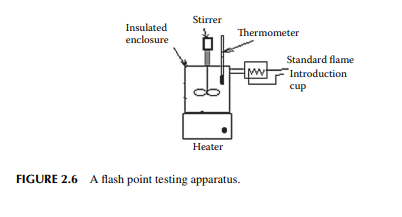
darkness produced by the fl ame of the oil while burning in a standard glass. The bloom should not be darker than a standard brightness desired in a lamp.
2.2.2.4 Distillation Test
ASTM distillation of kerosene is carried out under atmospheric conditions. Finished kerosene must be at least 20% distilled at 200°C or lower and the fi nal boiling point (FBP) should be no more than 300°C. Kerosene that is too light is dangerous for use in a domestic kerosene stove as explosion may occur owing to the presence of a very light boiling fraction especially in the range of naphtha. The presence of too heavy boiling fractions in kerosene will make it a poorly burning fuel.
2.2.2.5 Sulfur Content and Corrosion
Since sulfur produces hazardous sulfur dioxide, kerosene must be free from it, although a trace of it is always present. Domestic kerosene must not have a sulfur content of more than 0.25% by weight. A corrosion test of kerosene is also carried out using the copper strip corrosion method. Corrosiveness of oil will damage the storage tanks, stove containers, pipelines for transportation, etc. For domestic kerosene, it should not be worse than ASTM 1 in the copper strip test for 3 h at 50°C in a standard bomb. Important parameters as per the Indian BIS of kerosene
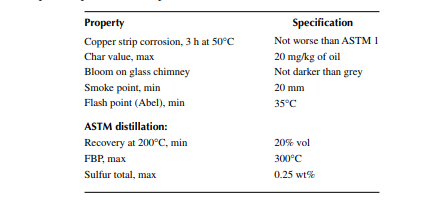
2.3 AUTOMOTIVE FUELS
2.3.1 MOTOR SPIRIT
MS is known as petrol in India and Europe but as gasoline in the U.S. It is an automotive fuel for running motor cars. Diesel is the other automotive fuel. There are two types of vehicles in India, classifi ed as petrol and diesel vehicles according to the type of automotive fuels they use. The engine of a petrol car is different from the engine of a diesel car. Petrol or MS is suitable for spark ignition (SI) type engines and diesel for compression ignition (CI) engines. In the SI engines, fuel is burnt directly by introducing an electrical spark into the mixture of air and vapour of MS through the carburettor (a mixing device of air and vapour of fuel) of the engine. Power is developed due to the volumetric expansion of burnt gases (fl ue gas) in the engine cylinder during the expansion stroke (forward stroke) and exhausted
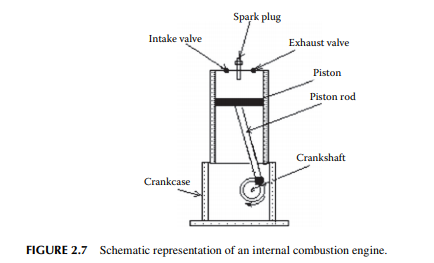
hydrocarbon liquid is needed as the fuel because it is readily vaporised, which is the most essential requirement for combustion in an SI engine. In the ASTM distillation, no internal refl ux is maintained, like TBP, and as a result the separation is not as good as it could be in TBP distillation. Correlation for the conversion from ASTM to TBP and vice versa is available and hence ASTM distillation data can be readily converted to TBP. ASTM distillation is the easiest test for the boiling ranges of hydrocarbons in MS. The required ASTM distillation analysis of MS is that 10%, 50%, and 90% vaporisation should occur at the maximum vapour temperatures of 70°C, 125°C, and 180°C, respectively. Though the IBP may vary, the FBP will not exceed 215°C. These vaporisation temperatures have signifi cance in engine performance. The 10% point of distillation is important for starting an engine. In winter, when ambient temperature is low and if the 10% point is high, vaporisation of MS will be diffi cult unless heated. Again, if it is very low it may cause vapour locking due to excessive vaporisation. The 50% point is an indication of uniform vaporisation in the engine during the warming-up period of driving and the 90% point is important as far as the crankcase dilution is concerned. If the 90% point is high, a residual part of the fuel will be unburnt and will mix-up with the motor oil used for lubricating the piston of the engine, causing dilution of crankcase oil. This is also the reason for increased fuel consumption per kilometre. Figure 2.9 depicts a ASTM distillation analysis of MS.
2.3.1.2 Octane Number
Engine performance is measured by the maximum power development and the rate at which it is developed at different engine speeds. If the rate of power development
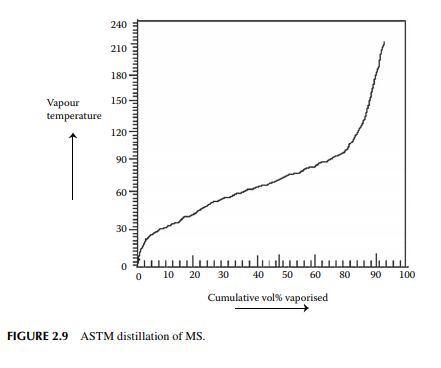
is not uniform with speed, rather it fl uctuates, then this type of situation is called knocking or hammering of the engine. Several experiments found that the composition of MS plays the main role in knocking. If MS contains more propane, butane (short chain hydrocarbons), iso-octane (branched chain hydrocarbons), benzene, toluene, xylenes, and aromatics (ring compounds) in the boiling range of MS then the rate of power development is smooth without knocking, whereas the long chain hydrocarbons give rise to severe knocking if present in the fuel in substantial amounts. Since MS is a mixture of all the short or long chain, branched, and ring hydrocarbons, it is common practice to use iso-octane as the fi ngerprint for measuring the relative engine performance of the mixture. Specifi cation of MS as far as engine performance is concerned is denoted by octane number. Octane number is defi ned, for any MS fuel, as the percentage of iso-octane in a mixture of iso-octane and n-heptane, which will give the same engine performance as could be achieved by the actual fuel sample. Thus, if an engine runs with 100% pure iso-octane, the power rating is 100% (knock free) and is defi ned as 100 octane number. If the engine is run with n-heptane, a straight chain hydrocarbon, there will be tremendous knocking in the engine and the octane number is taken as zero. If the engine is run with a mixture of isooctane and n-heptane with different proportions, the engine power rating will fall with the decrease in the proportion iso-octane in the fuel. The octane number of the MS sample, therefore, falls within 0 and 100. This is measured in a standard engine, known as the co-operative fuel research (CFR) engine. However, the octane number may be greater than 100, which is called the performance number. An engine test is carried out at two different speeds and the octane numbers are defi ned as the research octane number (RON) and the motor octane number (MON), which are conducted at two different speeds, 600 and 900 rpm, respectively. However, tested octanes may not correspond to real performance when the road conditions differ. RON is more applicable for city driving whereas MON is applicable for highway driving. The octane number falls with the increase in speed, which is why MON is always less than RON for the same MS fuel. Aircrafts using gasoline require very high RON fuel as necessary with the cruising speed. It is also found that the octane number falls with the altitude. The octane number of a MS fuel can be increased by adding tetra-ethyl lead (TEL), but this has been prohibited by environment protection laws. Hence, organic substances like methyl- or ethyl tertiary butyl ethers (MTBE or ETBE) are used instead of TEL for boosting the octane number.
2.3.1.3 Corrosion
The presence of mercaptan sulfur may cause corrosion in the fuel pipes and the engine cylinder and produce sulfur dioxide during combustion. In the past, merox (a catalytic mercaptan oxidation method) treatment was done to convert corrosive mercaptans to non-corrosive disulfi des, but this did not remove the sulfur originally present in the fuel. However, it did give rise to the formation of sulfur dioxide during combustion. Since emission of sulfur dioxide is prohibited by environmental protection laws, nowadays mercaptans and other sulfur compounds are mostly removed
by a catalytic hydrodesulfurisation unit in a refi nery. The corrosive effects of other organic compounds along with traces of sulfur-bearing compounds and additives must be tested in the laboratory. The copper corrosion test similar to that described in the testing of LPG is also carried out in the laboratory at standard temperature (50°C) for 3 h.
2.3.1.4 Reid Vapour
Pressure RVP of MS should not exceed 0.7 kg/cm2 (gauge) otherwise there will be the tendency for vapour locking in the engine and vapour loss as well during its storage. Too low vapour pressure will give rise to problems starting the engine. RVP is measured in a similar manner as described for the testing of LPG.
2.3.1.5 Oxidation Stability
MS is, in fact, a mixture of hydrocarbons obtained from various units of a refi nery, such as reformate (obtained from a naphtha reforming plant), thermally (viscosity breaking unit, coking unit, etc.), and catalytically cracked gasoline components (from a fl uidised bed catalytic cracking unit). By-products from petrochemical plants, like aromatics and pyrolysis gasoline components, are also blended. All these components may contain much unsaturated hydrocarbons especially the di-olefi ns, which are susceptible to mild polymerisation when in contact with oxygen or air. These polymerised products make layers of fi lms or gum like substances and reduce the effectiveness of the fuel while used. This gum formation is a slow process but may cause severe damage to fuel if stored for a long time. Therefore, the storageability of MS is measured in terms of the period during which the fuel does not form any gum. This is tested in the laboratory by contacting fuel and oxygen (or air) in a pressure vessel at a constant temperature for a specifi ed period (usually 6 h or longer) and a fall in pressure, if any, is observed.
2.3.1.6 Additives Various
additives, like colour (to distinguish octane numbers), anti-icing (to reduce ice formation), anti-static (to disperse the generation of statical electric charges), anti-oxidant, anti-corrosive, and octane boosting agents are added to the fuel.
2.3.2 HIGH SPEED DIESEL
High speed diesel (HSD) is another liquid fuel that is used most abundantly in our country in a variety of vehicles and appliances, such as cars, buses, tractors, lorries, barges, speed boats, railway engines, irrigation pumps, and generator sets. Like MS, diesel is also a mixture of hydrocarbon compounds, boiling in the range of 250°C–360°C. Unlike MS, diesel oil is not vaporisable at ambient condition but requires heating. Diesel is burnt in a CI engine where the fuel is atomised and sprayed in the hot compressed air. Since the temperature for autoignition (the method of ignition without the aid of fi re or spark) for diesel oil is much lower than MS, the temperature during compression of air causes this ignition.
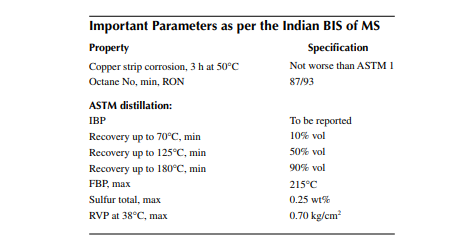
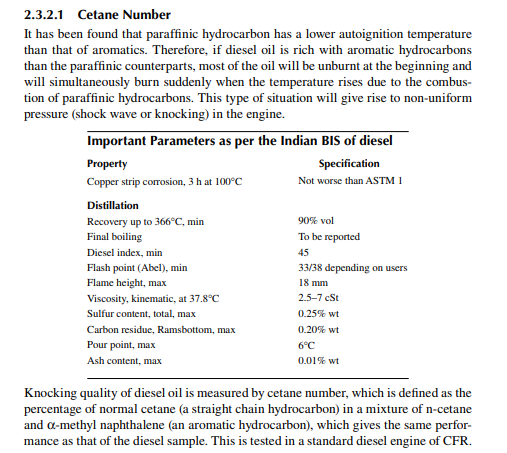
2.3.2.2 Diesel Index
The presence of paraffi nic hydrocarbons in diesel may be related by the aniline point, which is the temperature at which aniline solubilises the fuel in equal amounts
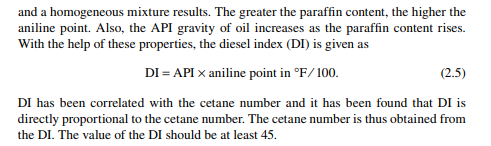
2.3.2.3 Sulfur
In order to reduce pollution, the sulfur content of diesel should not be large. In refi neries, catalytic desulfurisation is carried out to remove sulfur from diesel oil. The sulfur content should not be more than 0.25% by weight of the oil.
2.3.2.4Corrosion
A corrosion test of diesel is also carried out using the copper strip method at 100°C for 3 h.
2.3.2.5 Flash Point
The fl ash point of diesel is a minimum of 33°C for automobiles. However, depending on the ambient temperature, it may be higher. The lower the fl ash point, the greater the chance of autoignition. During winter a low fl ash point is preferable while in summer it should be more (around 35°C). Too high a fl ash point may cause knocking in the engine.
2.3.2.6 Flame Length
In the combustion chamber of an engine, a long fl ame length may damage the chamber. Hence, a short fl ame length is desirable. Diesel oil should not produce a fl ame length of more than 18 mm. In the refi nery, sometimes kerosene and other hydrocarbons, like heavy naphtha, are also blended in diesel with the result that the fl ame length may increase. Hence, reduced crude oil (RCO) is injected to adjust the fl ame length to the desired value.
2.3.2.7 Pour Point
The pour point is defi ned as the temperature at which oil will cease to fl ow due to the formation of wax crystals. In India, the pour point of diesel has been fi xed at a value less than 6°C. However, in colder places, a lower pour point is advisable.
2.3.2.8 Viscosity
In a fl ow process, fl uid experiences a kind of friction opposing the fl ow. This friction is known as fl uid friction, which is defi ned as the resistive force (shear) exerted between two parallel sliding layers of fl uid moving in the direction of fl ow. This shear force is proportional to the rate of change of velocity (shear rate) of the sliding layers. Viscosity is the proportionality constant between the shear force and the shear rate. The higher the viscosity, the greater the friction and the fl uid is termed more viscous. Most hydrocarbon liquids follow this rule (Newton’s law of viscosity). Low viscosity is preferred for diesel oil at ambient temperature. It should be between 2.5 and 7 centi stoke (cSt) at 38°C.
2.4 AVIATION FUELS
The fuels used in aeroplanes are called aviation fuels. Depending on the type of aircraft, like jet planes or turbine planes, different types of aviation fuels are used. They are either gasoline based for jet planes or kerosene based for turbine planes. Aviation gasoline is usually polymer gasoline or alkylated gasoline having an octane number greater than 100, usually expressed as the performance number. Kerosenebased aviation fuel is known as aviation turbine fuel (ATF) and is mostly consumed by passenger aeroplanes. This fuel is the hydrocarbon fraction boiling in the range of 150–250°C and is similar to the kerosene fraction. Though it resembles kerosene, tests are carried out under stringent conditions for the safety of the airborne people in the fl ying machines. A corrosion test is carried out using the copper strip test for 2 h at 100°C and a silver strip test is carried out for 16 h at 45°C. Distillation tests are conducted as for kerosene while the 20% recovery should be at 200°C and the FBP should not be more than 300°C. Besides freezing point is to be below −50°C as the sky temperature may be very low at high altitude.
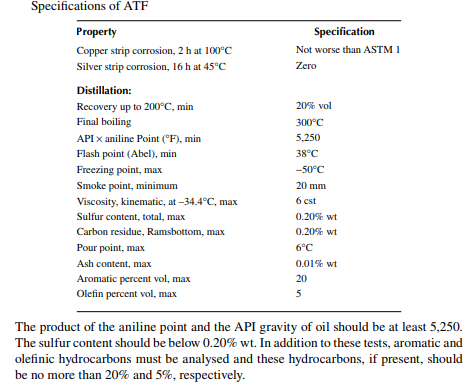
2.5 FURNACE FUELS
2.5.1 GASEOUS FUELS
Industrial furnaces are mostly fuel-fi red furnaces and use gaseous and liquid hydrocarbon fuels. Off-gases and by-product gases commonly generated in refi neries and
petrochemical plants consist of methane, ethane, propane, butane, and their olefi nic homologues. Gaseous fuel can generate a higher temperature than liquid petroleum owing to its higher heating value.
2.5.2 LIQUID FUELS
Light diesel oil or LDO (much heavier than HSD) is a liquid fuel. It is usually a blend of vacuum gas oil, coker gas oil, deasphalted oil, waxy distillates, etc., and falls into the category of black oil. A few properties measured as given in the table are the fl ash point, viscosity, total sulfur, pour point, and carbon residue. It is a cheap liquid fuel as compared to HSD and is commonly used in furnaces.
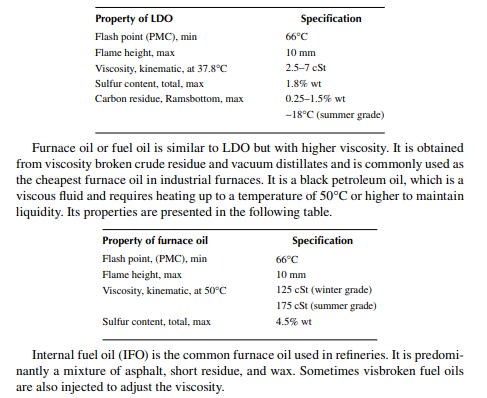
2.6 LUBRICATING OILS
A lubricant is a solid, semi-solid, or liquid material that is used to reduce friction between two solid surfaces. Examples of lubricants are graphite, sulfur, wax, soap, and mineral oil. Lubricating oils are liquid lubricants mainly made from petroleum oils (lube oil base stocks) blended with soaps of fatty acids and other additives. A lubricating oil present between two solid surfaces reduces the friction while in
motion and also helps in cooling down the heat of friction. The main ingredients are petroleum base stocks that are obtained from vacuum distillates of crude oil. These distillates are heavy petroleum fraction and cannot be vaporised like petrol or diesel. The quality of a lube oil is determined by properties like viscosity, viscosity index, pour point, and some additional properties determined by their end uses. 2.6.1 VISCOSITY Viscosity is a parameter that measures resistance to fl owability of liquid or gas. It is defi ned as the force exerted between two sliding layers of liquid or gas moving at different velocities. Visosity (or coeffi cient of viscosity) is the proportional constant between this force (shear) and the velocity gradient (rate of deformation due to shear or rate of shear). In the centimetre–gram–second system (cgs) unit, it is expressed in terms of gm cm/sec or poise. Usually it is expressed in centipoise or cP, where 1 poise = 100 cP. In SI, unit viscosity is expressed as pascal. Sec. However, in the hydrocarbon industry, the term “centistoke” is more popularly used as the measure of viscosity, which, in fact, is the kinematic viscosity. This is the ratio of viscosity (cP) to the density (g/cc) of the fl uid. There are various methods of viscosity measurement, e.g., capillary, orifi ce, rotary, fl oat or falling sphere, and vibrational methods, depending on the ranges of viscosity from light to heavy. A pressure drop in a tube of defi nite length and diameter can be used to measure viscosity by Poisulle’s equation of fl ow. Stoke’s law may be used to measure viscosity in a falling sphere method where time of fall at a defi nite height is reported. Viscous shear or drag in terms of power consumption for a typical rotating disk on a fl uid fi lm over a static one is a measure of viscosity.
2.6.2 SAYBOLT METHOD
This is a capillary method. For light and non-sticky hydrocarbon liquids, the Saybolt method is used where time (t) of effl ux of a defi nite quantity (60 cc) of liquid through a typically designed capillary tube kept in a constant temperature bath is measured. This is reported as Saybolt seconds. Viscosity in centistoke is related with Saybolt second (t) is given as
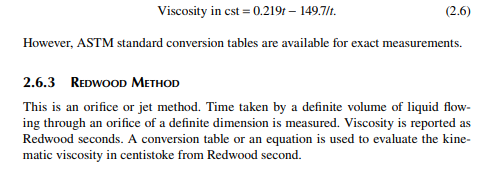
2.6.4 BROOKFIELD METHOD
This method uses a rotary type viscometer consisting of two disks containing the liquid under test. The shear force experienced by the rotating disk is measured against the liquid over the static one. Standard liquids are used for calibration.
2.6.5 VISCOSITY INDEX
The viscosity index (VI) is a parameter that indicates the rate of change of the viscosity of the oil due to a variation in temperature. This index is defi ned as the ratio of the difference of viscosity (U) of the lube oil to be used with respect to the viscosity (L) of petroleum (aromatic) oil having zero VI to the difference of viscosity (H) of high VI oil (paraffi nic; 100 VI) to the viscosity (L) of zero VI oil for a temperature change from 37.8°C to 98.9°C. This can be written in the following way,
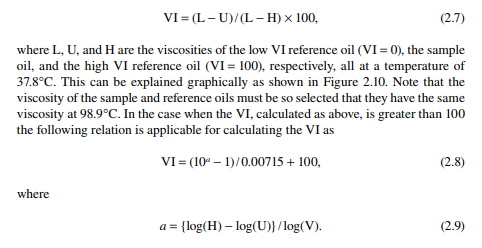
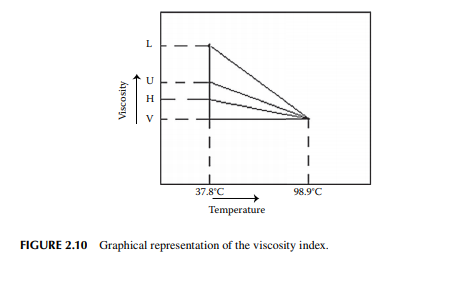
2.6.6 CLOUD POINT
The cloud point is the temperature at which oil becomes hazy or cloudy due to the onset of wax crystallisation or solidifi cation. This is tested in a standard tube in an ice bath. The tube fi tted with a thermometer is placed in the bath. At intervals, the test tube is removed (without disturbing the oil) to observe cloudiness. The temperature is reported to be the cloud point.
2.6.7 POUR POINT
The pour point is the temperature at which a liquid hydrocarbon ceases to fl ow or pour. This is measured by a standard method where a defi nite quantity of an oil sample is taken in a test jar or tube (with a thermometer properly stoppered), heated to 115°F (46°C) to make all the wax dissolve in oil, and cooled to 90°F (32°C) before testing. An ice bath containing ice and salt is made ready at a temperature of 15°F–30°F (−9°C to −1°C) below the estimated pour point based on cloud point and the test tube containing the sample is placed with the thermometer. At intervals of 5°F, the test tube is removed from the ice bath and tilted to see if the oil is mobile or static. If it is found that at a certain temperature the oil shows no movement even when the test tube is kept horizontal for 5 sec, this temperature is reported to be the solid point. The pour point is taken as 5°F above this solid point. Lube oils used in engines, gears, bearings, etc., vary with the properties. For example, in reducing the bearing friction, lube oil should be of high viscosity and high VI so that it is not squeezed out during use and is not thinned out or thickened with frictional heat and also should be capable of bearing load. Heavy semi-solid lubricants containing metallic soaps with base oil classifi ed as grease which are the common load-bearing lubricant. Lubricants used for lubricating the surface of an engine cylinder and piston should have a very high VI but low viscosity. Crankcase oil should also have the same property and it also serves as a cooling medium for engine cylinders. For aviation services, lube oil should have a high VI with a very low pour point. It has been found that the VI of paraffi nic oils is greater than napthenic and aromatic oils, whereas viscosity is low for paraffi nic oils as compared to naphthenic and aromatic oils. Contribution toward the viscosity, VI, and pour point from the paraffi n (P), naphthene (N), and aromatic (A) hydrocarbon groups are listed below. Hydrocarbon groups and properties of lube oils
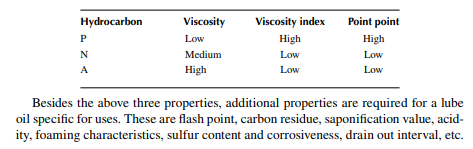
During use, the lubricant should be free from abrasive particles, free from water, free from carbon particles, etc. When it is used for cooling purposes, it should be of low viscosity to reduce fl uid friction during pumping. Power transformers are cooled by lubricating oil, known as transformer oil, which should have a high dielectric constant to avoid breakdown in the high electrical voltage. Varieties of lubricating oils and greases are produced by blending lube base stocks and other additives to meet different uses; presentation of all these are out of the scope of this book. However, a few lube base stocks and their properties according to the BIS are listed in Table 2.1.
2.7 MISCELLANEOUS PRODUCTS
2.7.1 JUTE BATCHING OIL
Jute batching oil (JBO) is a straight run product obtained from the atmospheric crude distillation unit. This has a boiling fraction slightly different from that of diesel cut and it is 340°C–365°C. There are two grades of this oil—JBO(p) and JBO(c). Both of these oils are used in the jute industry for processing and bailing jute fi bres. Jute packaging for food products and drugs are commonly employed and precautions must be taken to avoid any type of contamination. Hence, oils used for jute processing must conform to the specifi cations laid down by the Food and Drug Administration (FDA). The BIS specifi cation of JBO is listed below.
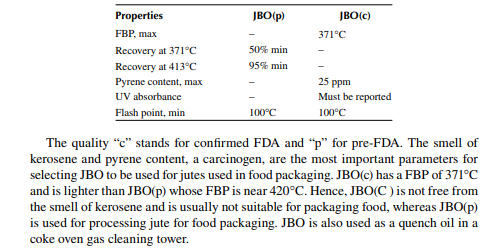
2.7.2 MINERAL TURPENTINE OIL
Mineral turpentine oil (MTO) has a boiling fraction similar to kerosene cut in the boiling range of 125°C–240°C. This cut may be obtained directly from the crude distillation unit as a straight run product or by splitting kerosene cut. It is mainly used in the paint industry as a solvent or thinner and hence desirable property are guided by the requirements of the paint industries. Typical properties are given in Table 2.2
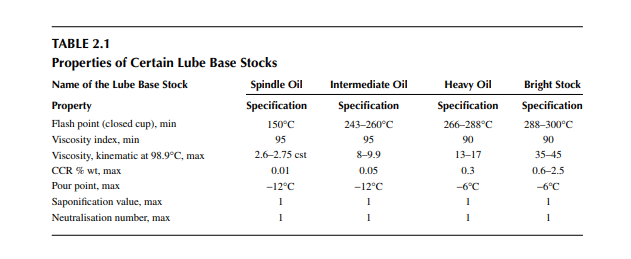
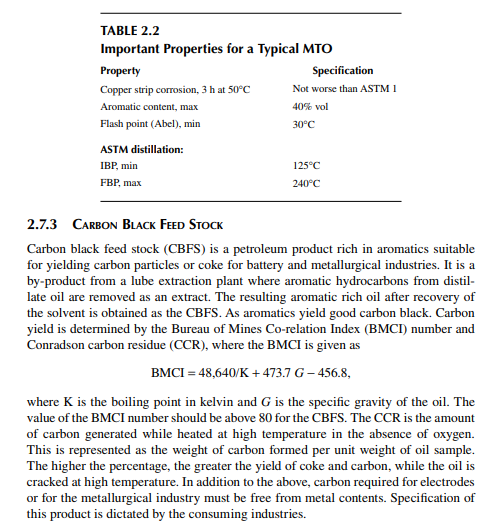
2.7.4 BITUMEN
Asphalt or bitumen is obtained from short residue (residual mass from the bottom of the vacuum distillation unit) after extraction of valuable oil (known as bright stock) by propane. Asphalt is a very sticky, semi-solid, viscous petroleum, containing various hetero-atomic compounds of hydrocarbons enriched with metallic, sulfurous, nitrogenous, and oxygenated compounds. At a temperature above 90°C, it fl ows like liquid and solidifi es at room temperature. It is mainly used as paving material, paint, water-proofi ng agent, etc. As a paving grade material, it should have a desirable penetration index, which is defi ned as the depth of submergence or penetration of a standard weight through a needle penetrator. The greater the penetration, the greater the softness of the asphalt. Typical paving grade bitumen has a penetration of 60/70 or 80/100 using a 100-g cone (1/100 cm)
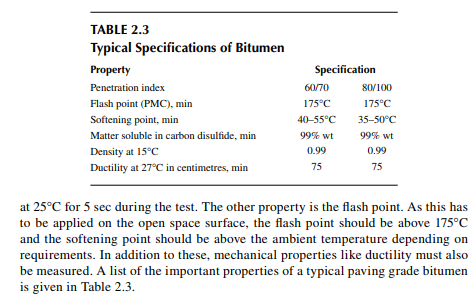
2.7.5 PETROLEUM COKE
Petroleum residue contains heavy hydrocarbons that crack at high temperature in the absence of air yielding gases, light hydrocarbon liquids, and black solid carbon rich residue or coke. The greater the amount of heavy aromatic hydrocarbons in the feed stock, the greater the yield of coke. Thermal cracking of petroleum involves various reactions, like decomposition, dehydrogenation, isomerisation, polymerisation, etc. Decomposition reaction takes the lead in the reactions and the yield of coke increases with the increase in time to cracking. In the old processes, cracking was carried out in a coking vessel (drum) until the drum was fi lled with coke. The modern method involves cracking in a tube-still heater followed by quenching of the product mass to avoid choking of the furnace tubes. By-products like gases, hydrocarbon liquids known as coker gasoline, and gas oil are also formed. The yield and quality of coke depend on the temperature, pressure, and reaction time. Petroleum coke is available in various forms, such as graphitic soft coke, needle coke, and fl uid coke. The quality of coke is determined by the highest content of carbon (usually from 88% to 95% by weight) and with minimum impurities, such as metallic components, moisture, volatile matters (hydrocarbons), and low sulfur, to make them amenable to manufacturing electrodes, for use in metallurgical furnaces as a carbon-reducing element and a clean fuel as well. There are a variety of uses for coke in the paint and petrochemical industries. Residues from most of the Indian crude oil are rich with heavy aromatic hydrocarbons and low sulfur and metallic components and, therefore, are suitable for making good quality coke. However, residues from Middle East crudes are not suitable for making coke due to their high content of sulfur and metallic contents and are converted to paving grade asphalts or bitumen or used as a feed for catalytic cracking or as a fuel.
2.7.6 WAX
Wax is obtained from the refi nery as a by-product from a de-waxing unit. It is roughly defi ned as petroleum hydrocarbons that solidify at a temperature above −20°C. High molecular weight normal paraffi nic hydrocarbons are the major constituent of wax, which freeze even at atmospheric temperature. Vacuum distillates usually contain much wax and are removed by freezing at low temperature. Paraffi nic wax is usually available as a slack wax, whereas naphthenic wax is available as microcrystalline wax. Slack wax is soft and has a low melting point suitable for candle making, paper coating, etc. Microcrystalline wax is hard with a high melting point and has a variety of applications, such as cosmetics, paints, and as an additive in rubber and plastics. Raw wax is obtained as a milky white to brown-coloured solid product and coloured wax is made out of this by adding additives. The quality of wax is guided by the user industries.
QUESTIONS
1. What is a TBP analysis of crude oil? What is meant by refl ux and theoretical plates in such an apparatus?
2. What are the parameters used to identify the quality of crude oil?
3. What are the various fuel products available from crude oil?
4. How does the ASTM distillation test method differ from TBP distillation?
5. Why and when is it necessary to carry out distillation in vacuum?
6. What are the various non-fuel products available from crude oil?
7. What is a “weathering test” and for which product is it applicable?
8. Defi ne octane and cetane numbers.
9. Distinguish between petroleum coke and bitumen with respect to their chemical properties.
10. Defi ne viscosity and the viscosity index.
11. What are the various methods of measurements of the viscosity of a liquid?
12. Defi ne cloud and pour points and their importance.