Multiple frequency eddy current techniques simply involve collecting data at several different frequencies and then comparing the data or mixing the data in some way.
Why the need for multiple frequencies? – Some background information
The impedance of an eddy current probe may be affected by the following factors:
● variations in operating frequency
● variations in electrical conductivity and the magnetic permeability of a object or structure, caused by structural changes such as grain structure, work hardening, heat treatment, etc.
● changes in liftoff or fill factor resulting from probe wobble, uneven surfaces, and eccentricity of tubes caused by faulty manufacture or damage
● the presence of surface defects such as cracks, and subsurface defects such as voids and nonmetallic inclusions
● dimensional changes, for example, thinning of tube walls due to corrosion, deposition of metal deposits or sludge, and the effects of denting
● the presence of supports, walls, and brackets
● the presence of discontinuities such as edges
Several of these factors are often present simultaneously. In the simple case where interest is confined to detecting defects or other abrupt changes in geometry, a differential probe can be used to eliminate unwanted factors, providing they vary in a gradual manner. For example, variations in electrical conductivity and tube thinning affect both coils of a differential probe simultaneously. However, if unwanted parameters that occur abruptly are affecting the measurements, they can sometimes be negated by mixing signals collected at several frequencies.
An example of where a multi-frequency eddy current inspection is used is in heat exchanger tube inspections. Heat exchanger assemblies are often a collection of tubing that have support brackets on the outside. When attempting to inspect the full wall thickness of the tubing, the signal from the mounting bracket is often troublesome. By collecting a signal at the frequency necessary to inspect the full thickness of the tube and subtracting a second signal collected at a lower frequency (which will be more sensitive to the bracket but less sensitive to features in the tubing), the effects of the bracket can be reduced.
There are a number of commercially available multi-frequency eddy current instruments. Most operate at only two frequencies at a time but some units can collect data at up to four frequencies simultaneously. Multi-frequency measurements can also be made using an impedance analyzer but this equipment is generally not suitable for field measurements. A typical impedance analyzer system is shown below. The interest in pulsed eddy current instruments is largely due to their ability to, in essence, perform multi-frequency measurements very quickly and easily.
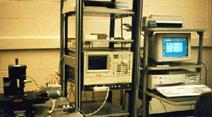