Manufacturing facilities use industrial presses to create, form or assemble a product
· 5 main types of presses are typically used in an industrial setting
· Each type creates force in a different way that impacts the application, purchase price, operational cost, precision, and safety
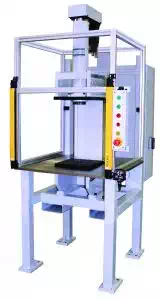
Photo Courtesy of Promess
Industrial presses apply a controlled force to a material or part to complete a process step. They can be powered by many different energy sources and range greatly in size. Many manufacturing facilities use an industrial pressing operation in their process to create, form or assemble a product.
Entire books are written on the topic of industrial presses, so this article will narrow its focus and concentrate on the relatively low-force, precision press machines used to assemble component parts. Most assembly presses are made up of a frame, ram and platen. Custom press frame configurations give engineers endless options; however, most standard assembly presses utilize a “C” frame, “H” frame or 2-post configuration. Regardless of the frame’s shape and orientation, the ram is the moving element that applies the press force, and the frame is a secure mount for the platen that holds the workpiece.
Below, we’ve outlined the five main types of presses used in industrial settings, their typical usage, and methods that can be utilized to verify the assembly process. Each type of press creates force in a different manner and this impacts the application, purchase price, operational cost, precision, safety, and process feedback capabilities.
- Manual Presses
As the name implies, these industrial press machines are powered by a human operator. They are simple, basic tools and therefore the purchase price and operational cost of this type of press is low. Manual presses utilize different methods to produce force and linear motion of the ram. A common press for very low volume assembly work utilizes a self-contained hydraulic system. Pumped via a lever, a hydraulic cylinder slowly extends with high force to press self-guided assemblies together. This system is very slow and takes a lot of effort, so it is typically used only for one-off, high-force processes.
Arbor presses utilize a lever arm or large wheel with a mechanical linkage to move the press ram up and down. The force is amplified by the linkage, which is typically either a rack & pinion or toggle mechanism. Rack & pinion presses amplify the applied force equally throughout the entire ram stroke. Toggle mechanisms start out with a lower force and increase the amplification toward the end of the stroke. In all of these variants, the assembly process and speed is controlled entirely by the operator. Press monitoring options are limited but include stroke verification switches, force displays and also locking mechanisms, which prevent the ram from being raised unless the stroke has been fully completed. Like any hand tool, safe operation of the press is the responsibility of the operator.
- Pneumatic Presses
These assembly processing machines utilize compressed air as their power source. A standard air cylinder and “two-hand, anti-tie down” control valves are used to initiate the press cycle and move the ram up and down in a safe manner. The maximum force is relatively low and is determined by the cylinder bore size and the pressure of the regulated air source. The press force is consistent throughout the entire ram stroke and cannot be adjusted mid-stroke by the operator.
Advantages of the pneumatic press type are its higher speed, relatively low total cost and reduced operator fatigue. However, the operator cannot “feel” the assembly process as there is no tactile feedback. With additional control devices and cost, the assembly process can be monitored using stroke position switches, linear transducers, load cells, and part sensing devices. Since air is compressible, unless an additional oil-dampening circuit is employed, the working press stroke may be choppy and vary from part to part. This inconsistency limits the resolution of the process monitoring system; therefore, pneumatic presses are generally not a good choice if precise force/distance signature analysis is a quality requirement.
If the operator has additional tasks, and two-hand controls limit throughput, a light curtain can be utilized as a component of the machine’s safety system. A machine safety assessment, by qualified professionals, is extremely important and should not be overlooked. Not only is compressed air stored energy, if the air source fails, the press ram could fall, which could also cause injury. To prevent a falling load, air-piloted check valves or shaft-locking devices may also be necessary.
- Pneumatic Intensified (Air/Oil) Press
These machines are similar to pneumatic presses and many of the characteristics, advantages, disadvantages, and safety concerns mentioned above hold true. They are powered by compressed air; however, the addition of hydraulic oil into the control circuit enhances the capabilities of this press type. Since oil is not compressible, it can be safely intensified to high pressures. The high-pressure oil is smaller in volume than the air that produced it, so the total displacement of the high force stroke is relatively short.
This “power stroke” can, however, be controlled with flow-restricting valves resulting in a smooth, uniform ram motion. Packaged air/oil cylinders often advance the majority of their stroke with low force, and, after contacting the workpiece, they utilize internal fluid passages to automatically shift over to their full-force power stroke.
If the process requires force/distance monitoring or high force over a short distance, an air/oil press may be the best solution. These presses can consume a lot of compressed air, which is a costly form of energy; however, they can be a good, lower-cost solution in many applications.
- Hydraulic Assembly Presses
This type of industrial machine utilizes plant electricity, a hydraulic power unit and a hydraulic cylinder to move the press ram. These presses can be purchased in a variety of pressures and a range of sizes as “stand alone” pre-engineered units. They are ready for use as soon as part-specific tooling is mounted to the ram and platen.
Like the pneumatic press, maximum force is determined by the machine’s cylinder bore size and regulated operating pressures. Unlike an air/oil press, the press force is consistent throughout the entire stroke range. Ram speed is limited by the flow and oil volume restrictions of the hydraulic power package and circuit. Operator safety is again a serious concern, and one must be sure to engineer the system utilizing applicable safety-rated switches and sensing devices.
With additional control devices and cost, the assembly process can be monitored using stroke position switches, linear transducers, load cells, and part sensing devices. Since hydraulic oil is not compressible, the entire press stroke will be a smooth motion, which enhances the resolution of the process monitoring system. There are many advantages to this type of press and many are used in factories around the world. The main disadvantages are the inevitable leaks, noise, smell and significant heat generated by the hydraulic power unit. In addition to the higher initial cost, maintenance costs can also be higher due to the system complexity.
- Servo Electric Presses
These industrial processing machines have been around for decades and are continuing to grow in popularity. They are increasingly selected over the other press types in many factories as the cost of servo motors and control electronics has come down significantly in recent years. The initial higher investment is also offset by lower operational and maintenance costs of an all electro-mechanical system.
This type of press utilizes plant electricity, a servo motor/drive unit, and an integrated ball screw actuator to impart linear motion to the press ram. These presses can also be purchased as pre-engineered packages with a wide variety of options. It’s very common to have integrated load cells, linear transducers, external part sensing, and other quality monitoring devices controlling the process, thereby lowering scrap rates and improving quality significantly.
The press software generally offers options to assist with the controls integration of safety devices, HMI display screens and statistical quality control packages. Another capability, offered by some servo press manufacturers, allows the addition of controlled rotational motion integrated with the linear motion. This is beneficial when the assembly procedure requires the components to be rotated relative to one another during the press stroke to prevent damage