Flask:
A wooden frame or metal without static top or bottom, a mould is formed. The moulding structure depends on the location of the flask. It is known with various names they are DRAG, COPE, and CHEEK.
Drag: Is for lower moulding flask
Cope: Is for upper moulding flask
Cheek– In the three piece moulding intermediate moulding flask is used.
For temporary applications wood is used by the manufacturer and general applications process is uses metals for long term use.
Pattern:
With some alterations to the replica of the end product is made. With the help of the pattern mould cavity is made.
Parting Line:
Parting line is a dividing line among the two moulding flasks that creates the sand mould. Dividing the line between the two halves of the pattern is known as split pattern.
Bottom Board:
The bottom board is normally made up of wood. It is used in the initial stage of the mould making.
Initially, the pattern is kept on the bottom board and then sand is sprinkled on it, and finally the ramming is performed in the drag.
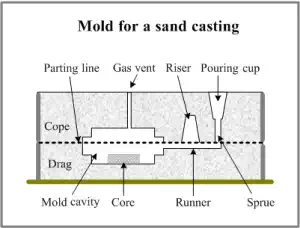
Facing Sand:
To give a better external surface to the casting a lesser quantity of carbonaceous material is scattered on the internal surface of the mould cavity.
Moulding Sand:
Moulding sand is the newly prepared refractory material used for manufacturing the mould cavity. It is a mixture of clay, silica and moisture in appropriate proportion to get the preferred result, and it surrounds the pattern while making the mould.
Core:
In casting process core is used for making the hollow cavities.
Pouring Basin:
At the top of the mould there is a minor funnel designed cavity in which the liquid metal is poured, which is known as pouring basin
Sprue:
Sprue is a passageway over which the liquid metal starts from the pouring basin and then it touches the mould cavity. The mould it is used to control the flow of the metal.
Runner:
Runner is a channel through which the liquid metal is carried from the sprue to the gate.
Gate:
Gate is the way to which the molten metallic enters the mould cavity
Chaplet:
Chaplets are used in the mould cavity for support, and they take care of its individual weight plus control the metallostatic forces.
Chill:
Chills are metal objects which are located in the mould to raise the cooling rate of castings and provides even or desired cooling rate.
Riser:
It is a reservoir of molten metal delivered into the casting so that hot metal can run back into the mould cavity when there is a drop in the volume of metal due to the solidification.
Vent:
In the mold there is a small opening to simplify escape of gases and air, which is known as vent.
Metals used in casting:
Alloy:
It is a metallic solid produced by joining two or more metals or by accumulating a non – metal to a metal for the purpose of improving its properties for end use.
Ferrous Alloys:
Alloys with iron and its constituents
Non – Ferrous Alloys:
There is no iron base metal
Cast Iron:
A brittle and hard alloy of carbon and iron that can be willingly casted in a mold, as it contains a higher amount of carbon than steel is known as cast iron. It is firm and unchanged.
Ductile Iron:
A cast iron is been treated with a molten element, such as cerium and magnesium to induce the creation of free graphite such as spherulites or nodules. This informs an assessable degree of ductility to the cast metal. The ductile iron is dealt by the project engineer, involving a single combination of fatigue resistance, strength, toughness and wear resistance as well as outstanding ductility characteristics.
Aluminium Casting:
Aluminium is a silvery white ductile metallic element. Aluminium is the best abundant metal in the landscape, and it is extensively used for the casting plus foundry patterns. Aluminium is also utilized as deoxidizers in steel and iron making.
Steel Casting:
Steel casting is a specific form of casting and it involves several types of alloy steels and carbon steels.
Steel Alloys:
Steel that has existed alloyed with added metals from 1.0 % – 50% by weight to increase mechanical properties of the steel.
Alloy steels are divided in to two types they are
- Low alloy steel
- High alloy steels
Carbon steel casting:
Low cast carbon steel covers mostly carbon as the principle alloying component. Other elements are exists in lesser quantities, including those extra added for de-oxidation. They are shaped to a great variety of properties because arrangement and heat treatment can be selected to attain specific mixtures of properties that include hardness, ductility, fatigue resistance toughness and strength.
Stainless steel casting:
Mainly the casting is made from the stainless steel. Stainless steel is a steel alloy with a minimum of 10.5 – 11 % chromium content by mass. Stainless steel does not corrode, stain or rust as easily as the other ordinary steel. According to the condition of the environment the surface finish and grades of the materials are varied.