Material Requirement Planning (MRP) is a computer based inventory management technique used for determining the quantity and timing for the acquisition of dependent demand items needed to satisfy master schedule requirements.
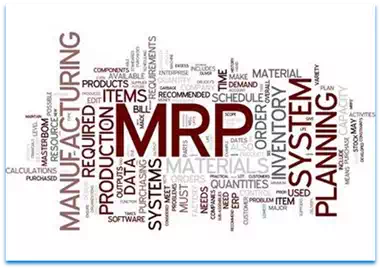
The Terminology used in MRP are:
Dependent Demand: Demand for components that is derived from the demand of other items.
Parent and component items: A parent is an assembly made up of basic parts or components. The parent of one subgroup may be a component of higher-level parent.
Lot Size: The quantity of items required for an order. The order may be either purchased from a vendor or produced in house. Lot sizing is the process of specifying the order size.
Time Phasing: Scheduling to produce or receive an appropriate amount (log) of material so it will be available in the time periods.
Time Bucket: Time bucket is the time period used for planning purposes in Material Requirement Planning (MRP) usually 7 days (week).
Requirements: Projected needs for raw materials, components, sub-assemblies or finished goods. Gross requirements are total needs from all sources, whereas net requirements are βnetβ after allowing for available inventory.
Requirement explosion: The breaking down (exploding) of parent items into components parts that can be individually planned and scheduled.
Bill of Materials: A list of all components (sub-assemblies and materials) that go into assembled items. It frequently includes the part numbers and quantity required per assembly.
Scheduled Receipt: Materials already ordered from vendor or in-house shop. The MRP shows both the quantity and project time of receipt.
Lead-time Offset: The supply time or number of time buckets between releasing an order and receiving the materials.
Planned Order Release: The plan to initiate the manufacture of materials or purchase of materials so that they will be received on schedule after the lead-time offset.
Different Lot Sizing Techniques in MRP are:
1. Lot for Lot (LFL): Order the exact amount of the net requirement each period.
2. Single Lot: Order quantity is equal to the total requirement and only one order is to be placed.
3. Economic Order Quantity (EOQ): Order an EOQ or ERL amount.
4. Least Unit Cost (LUC): Order the net requirement for the current period or current plus next or current plus next two and so on, depending upon which gives the lowest unit cost.
5. Minimum Cost Period (MCP): Order quantity is selected in such a way the cost period must be minimum.
6. Part-Period Algorithm (PPA): Use the ratio of ordering and carrying costs to derive a part-period number and use the number as a criterion for cumulating requirements.
7. Period Order Quantity (POQ):
Divide the Economic Order Quantity (EOQ) into the annual demand and order that many times per year.