What is a Worm Gear?
For transmitting power between two non-parallel and non-intersecting shafts worm gear is used. A typical worm gear looks like below:
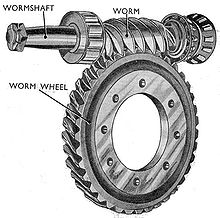
When you need very high reduction ratio and you have space constraints or donβt have the provision of using many gears, then you can think of using a worm gear for your design. You can design a worm gear box
for a reduction ratio as high as 200:1. The only problem with this type of gear box is the heat generated during power transmission. So you have to have provisions for a sufficient numbers of fins and/or fans for the gear box.
Another problem with this gearbox is that there is very less contact area between the worm thread and the gear teeth and more backlash. Backlash is the amount of rotational clearance available between the gear teeth and the worm thread. You can check the backlash of a pair of gears by changing the direction of rotation of the worm; the more freely you can rotate the worm, the more backlash is present. Backlash makes an ordinary worm gear inappropriate for the precision applications like robotics and medical applications. In order to avoid this problems, enveloping worm gear design concepts arose.
What is a Enveloping Worm Gear?
In the enveloping worm gear design, either the contour of the gear teeth or the contour of the worm threads or the contour of the both is modified in such a way that the amount of the contact surfaces increases. Thus, you will get increased accuracy from the worm gear.
When only the contour of the gear teeth is modified like below to get the increased amount of contact surface then the arrangement is called single enveloping worm gear.
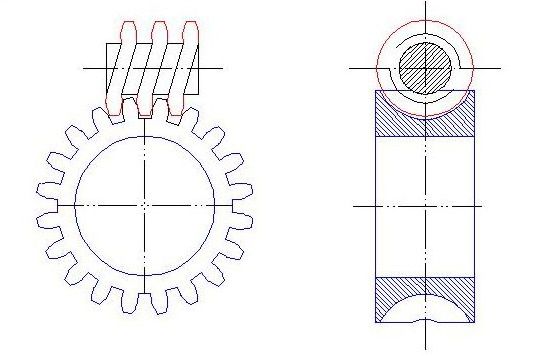
If you observe the right hand side view, you can see that the profiles of the gear teeth are curved to match the circular profile of the worm thread. But still you can see from the left hand side view that, hundred percent engagements is there only for one thread (the middle one) and the two of the side threads have partial engagement and this is not desired. This problem can be solved by using double enveloping worm gear design.
In double enveloping worm gear, the teeth profile of the gear as well as the shape of the worm threads are modified to achieve better engagement.
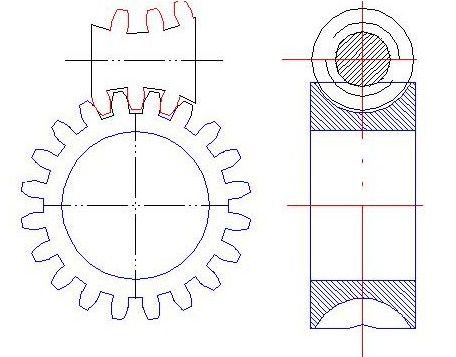
From the right-hand side view of the picture you can see how the shapes of the worm threads have modified in line with the circular shape of the gear teeth. Now, you can see the complete engagement throughout the length and width of the worm gear and thatβs what we want.
Conclusion
The worm gear is most suitable for higher reduction ratio. But the problem with the ordinary worm gear is less contact area between the worm threads and gear teeth. This problem can be solved using an enveloping worm gear. However, major challenge for the enveloping worm gear is itsmanufacturing process. Finding a supplier for the enveloping worm gears is not as easy as that of ordinary worm gear.