As a rule of thumb, a product should be replaced when it is not as useful as it is supposed to be. This may happen at any time during the product life cycle due to different causes. At the early stages of product launch and/or usage, this might be the result of the product’s failure to meet users expected specifications. At later stages, the cause might be change of users’ needs due to, for example, product obsolescence because of new technological innovations or economic and social factors such as more intense competition and regulatory and statutory obligations. And at the latest stages, the cause might be lack of proper effectiveness and efficiency due to the product being worn out, which will lead to disposal of the product.
Product Replacement in Product Lifecycle
Lifecycle of a new product initiates with spark of an idea in the mind of designer, most of the time in response to satisfying a recognized need or finding a solution for identified problems, and proceeds with product design, process design, production launch, utilization and maintenance, and disposal. Companies based on their marketing strategy divide utilization and maintenance stage into more stages according to the way they intend to support their products with after sale services and supplies. For instance, a company may divide the utilization and maintenance stage into the following stages:

– A first stage at which guarantee and/or warranty is active. In this stage product replacement may take place due to dissatisfaction from the customer, sometimes even without any reason declaration and extra payments by the customer. Sometimes a company may establish a lifetime guarantee policy that enables cost-free product replacement during the entire lifecycle of the product.
– A second stage at which volume production is finished and guarantee and/or warranty time is over but the product is still in use. In this stage the company supports maintenance services and supplies, but customer may pay for product replacement if the product malfunctions in such a way that it is not possible or feasible to repair it, or the product is no more needed due to technological innovations, economic and competitive changes, or the latest social restrictions. In the latter case, product upgrade and retrofit is more likely to take place.
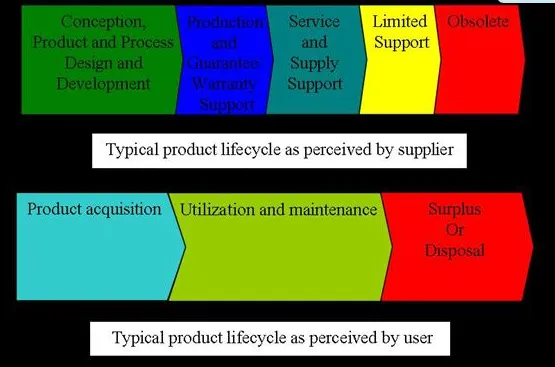
· A third stage at which the product is more or less in use and company limits product support to maintenance supplies as long as materials and parts are available.
– A fourth stage at which product is obsolete because the company is not supporting the product by any means and it is not feasible for the company to do so. This is the stage at which product disposal should take place and, if the product’s function is still needed, it may be replaced with an upgraded product.
· Next: Product Replacement Policy, Product Lifecycle Monitoring and Tracing Tools, and the Replacement Process
· Configuration management method sand product lifecycle management (PLM) software applications are methods and tools used to trace and monitor a product throughout its lifecycle. The general stages of the lifecycle replacement process are discussed, as well as the two different points of view- the manufacturer or provider, which is more concerned with the early stages of the product lifecycle, and the consumer of the product, which is more concerned with obtaining, using, and maintaining the product, and, when the time comes, disposing of it.
Product Replacement Policy
The product replacement policy is a part of the product lifecycle management policy. This policy should be considered from two different points of view: first from the product manufacturer, supplier, or provider point of view, and second from the user point of view.
The first point of view takes a wider span of product lifecycle into consideration in comparison to the second point of view because it is more concerned with the earlier and initiative stages of the product lifecycle, although the last stages are as well considered. An example of this policy was presented in the previous section of this article.
The second point of view is more concerned with product acquisition, utilization, maintenance, surplus, and disposal. Polices driven from this point of view determine that products reaching the end of their lifecycle are candidates for disposal. With these policies products are ranked according to extend of usage and change of business needs which may lead to early disposal or surplus and replacing them by newer and upgraded products.
Products Lifecycles Tracing and Monitoring Methods and Tools
There are certain methods and tools to trace and monitor a product in its lifecycle; among these are configuration management method and product lifecycle management (PLM) software.
Configuration management is a method to trace and control functional and physical characteristics of a product within its entire lifecycle. Configuration management process includes configuration management planning, configuration identification, change control, configuration status accounting, and configuration auditing. For detailed description of these activities ISO 10007 might be consulted.
Product Lifecycle Management (PLM) manages the entire lifecycle of a product. PLM is concentrated management of all product data and applied technology to access this information and knowledge. PLM is a business strategy to integrate CAD/CAM and PDM, with methods, people, and the processes through all stages of a product’s lifecycle. Configuration management might be a module within PLM software package.
By configuration management as a traditional manual method or within a PLM software package, it is possible to trace certain components of a system, so called configuration items, and replace them at predetermined times of utilization of that system. For instance, certain components of an aeroplane shall be replaced after certain flight hours, these components are determined as configuration items and their information is traced and recorded and they are replaced when the time comes. These components might themselves be products, and this way a system traces them to the end of their lifecycle.
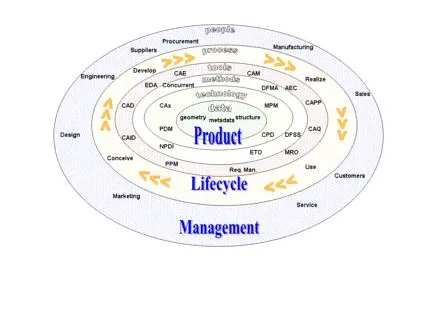
Replacement Process
From the above discussion, general stages of the lifecycle replacement process can be summarized as:
· Define lifecycle management policy for the supposed product. This policy should determine consecutive stages of product lifecycle, conditions for transferring from each stage to the next one, and rules for product replacement, surplus, or disposal.
· Define factors, elements, parameters, etc. to be traced, monitored, and measured based on stage to stage transferring conditions. Use proper methods and tools like PLM and configuration management as appropriate.
· Trace, monitor, and measure defined items periodically based on defined policy.
· Replace, surplus, or dispose product as they reach the change point according to defined policy.
As mentioned before and as a general rule, the time to replace a product is when utilization/operating and maintenance costs of product exceed its benefits.