This article explains what forging is and its uses and applications. The content also focuses on the different methods of forging like open or closed die forging, hammer forging, etc.
What is Forging?
The manufacturing stages which involve processing of metal objects through a planned heating/cooling treatments along with intermediate compression procedures is called forging.
Forged parts vary in size ranging from a few pounds up to 300 tons, and can be called small, medium, and heavy forgings. Small parts include tools such as chisels and tools used in cutting and carving wood. Medium forgings include car axles, small crankshafts, connecting rods, levers, and hooks. Heavier forgings are shafts of power plant generators, ship crankshafts, turbines, and columns of presses and rolls for rolling mills.
Methods Of Hot Forging
Open Die Forging
Heated metal parts are shaped between a top die attached to a ram and a base die connected to a hammer anvil or press bed. Metal parts are
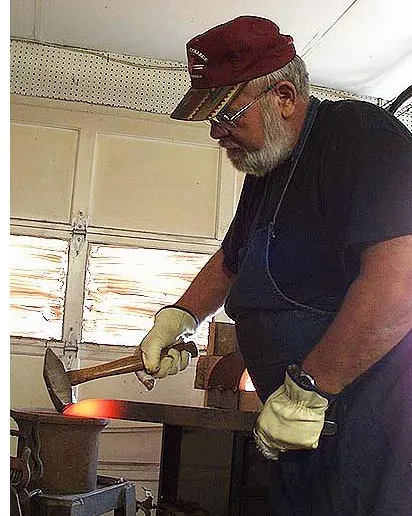
heated above their recrystallization temperatures and steadily shaped into the selected configuration through the hammering or pressing of the work piece. The metal is never wholly confined or restricted in the dies. The majority of open die forgings are formed on flat dies. However, round swaging dies, mandrels, pins, V-dies, and free tools are also utilized, depending upon the configuration of the size and part. Although the open die forging method is often related with the use of larger, simply shaped parts such as bars, blanks, rings, hollows or spindles, it can be considered the final option in the intended customization of special metal components. Long life and high intensity parts, optimized in terms of both structural integrity and mechanical properties, are produced in different sizes, ranging from a few pounds to hundreds of tons in weight.
Closed Die or Impression Forging
In this process the hot metal is trapped in recessed impressions, and is hydraulically or mechanically pressed to a desired shape. Often two or more progressive impressions are used, normally in conjunction with one or more preforming operations. A negative image of the component to be made is sunk into a block or pair of blocks. The die set is keyed or clamped into a press or hammer, which supplies the energy for the deformation. This method is used to make cutlery, automotive parts, and parts for aircraft engines.
A forging method in which the part is distorted by recurrent blows using a forging hammer, between impression or flat dies. This procedure is also called drop forging.
The following forging equipment is normally found in industrial settings.
Hydraulic Forging Press
A forging machine includes an anvil mass and a ram block, to be released and struck against, between which forging is carried out. The machine comprises a damping mass, which experiences the blow and moves in a large amplitude of motion in comparison with the amplitude of motion of the anvil mass, to damp the blows conducted from the anvil mass to the stationary foundation of the machine.
It consists of the press, the hydraulic intensifier, and the auxiliary water tank. A piece of work is compressed between the dies. Numerous shapes of dies may be used. The press head is forced down by hydraulic pressure on the ram in the cylinder, and is lifted by steam pressure under the two pistons in the cylinders. The vertical motion of the press head is directed by the four columns which hold the press firmly against distortion. Water pressure is exerted through the pipe from the steam intensifier. Steam admitted under the piston imparts the pressure to the water.