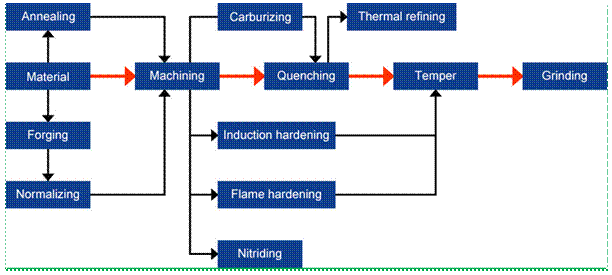
Summarizes and definitions of the some common heat treatment processes like annealed, normalized, quench hardened and tempered are given below.
Annealed is the condition of a metal that has been heated above a specific temperature, depending upon its composition and then cooled down in the furnace itself or by burying it in ashes or lime. This annealing process makes the metal very soft and ductile. Annealing usually precedes flow-forming operations such as sheet metal pressing and wire tube drawing.
Normalizing is the condition of a metal that has been heated above a specific temperature, depending upon its composition and then cooled down in free air. Although the cooling is slow, it is not as for annealing so the metal is less soft and ductile. This condition is not suitable for flow forming but more suitable machining. Normalizing is often used to stress relieve castings and forgings after rough machining.
Quench hardened is the condition of a metal that has been heated above a specific temperature, depending upon its composition and then cooled down very rapidly by immersing it in cold water or cold oil. Rapid cooling is called quenching and the water or oil is called the quenching bath. This rapid cooling from elevated temperatures makes the metal very hard. Only medium-carbon steels and high-carbon steels can be hardened in this way.
Quench-hardened steels are brittle as well as hard. To make them suitable for cutting tools they have to be reheated to a specified temperature below 200 to 300°C and again quenched. This makes them slightly less hard but very much tougher. Metals in this condition are said to be tempered.