Nowadays customers are demanding a wide variety of products. To satisfy this demand, the manufacturers’ “production” concept has moved away from “mass” to small “batch” type of production. Batch production offers more flexibility in product manufacturing. To cater this need,Flexible Manufacturing Systems (FMS) have been evolved.
As per Rao, P. N. [3], FMS combines microelectronics and mechanical engineering to bring the economies of the scale to batch work. A central online computer controls the machine tools, other work stations, and the transfer of components and tooling. The computer also providesmonitoring and information control. This combination of flexibility and overall control makes possible the production of a wide range of products in small numbers.
FMS is a manufacturing cell or system consisting of one or more CNC machines, connected by automated material handling system, pick-and-place robots and all operated under the control of a central computer. It also has auxiliary sub-systems like component load/unload station,automatic tool handling system, tool pre-setter, component measuring station, wash station etc. Figure 1.2.4 shows a typical arrangement of FMS system and its constituents. Each of these will have further elements depending upon the requirement as given below,
A. Workstations
– CNC machine tools
– Assembly equipment
– Measuring Equipment
– Washing stations
B. Material handling Equipment
– Load unload stations (Palletizing)
– Robotics
– Automated Guided Vehicles (AGVs)
– Automated Storage and retrieval Systems (AS/RS)
C. Tool systems
– Tool setting stations
– Tool transport systems
D. Control system
– Monitoring equipment’s
– Networks
It can be noticed that the FMS is shown with two machining centers viz. milling center and turning center. Besides it has the load/unload stations, AS/RS for part and raw material storage, and a wire guided AGV for transporting the parts between various elements of the FMS. Thissystem is fully automatic means it has automatic tool changing (ATC) and automatic pallet changing (APC) facilities. The central computer controls the overall operation and coordination amongst the various constituents of the FMS system.
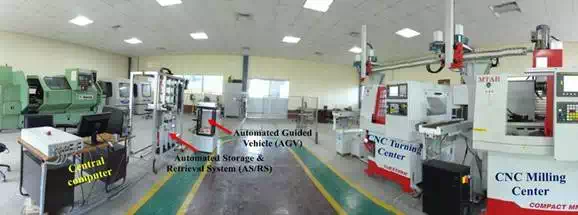
Figure 1.2.4 A FMS Setup
The characteristic features of an FMS system are as follows,
1. FMS solves the mid-variety and mid-volume production problems for which neither the high production rate transfer lines nor the highly flexible stand- alone CNC machines are suitable.
2. Several types of a defined mix can be processed simultaneously.
3. Tool change-over time is negligible.
4. Part handling from machine to machine is easier and faster due to employment of computer controlled material handling system.
Benefits of an FMS
• Flexibility to change part variety
• Higher productivity
• Higher machine utilization
• Less rejections
• High product quality
• Reduced work-in-process and inventory
• Better control over production
• Just-in-time manufacturing
• Minimally manned operation
• Easier to expand