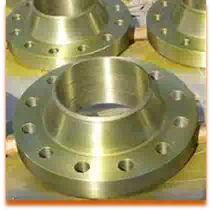
An alloy steel may be defined as a steel to which elements other than carbon are added in sufficient amount to produce an improvement in properties. The chief alloying elements used in steel are as follows:
I. Nickel. The steels containing 2 to 5% nickel improves tensile strength, raises elastic limit, imparts hardness, toughness and reduces rust formation. It is largely used for boiler plates, automobile engine parts, large forgings, crankshafts, connecting rods etc. When 25% nickel is added to steel, it results in higher strength steels with improved shock and fatigue resistance. A nickel steel alloy containing about 36% nickel is known as lnvar. It has nearly zero coefficient of expansion. So it is widely used for making pendulums of clocks, precision measuring instruments etc.
2. Chromium. The addition of chromium to steel increases strength, hardness and corrosion resistance. A chrome steel containing 0.5 to 2% chromium is used for balls, rollers and races for bearings, dies, permanent magnets etc. A steel containing 3.25% nickel, 1.5% chromium and 0.25% carbon is known as nickel-chrome steel. The combination of toughening effect of nickel and the hardening effect of chromium produces a steel of high tensile strength with great resistance to shock. It is extensively used for armour plates, motor car crankshafts, axles and gears etc.
3. Vanadium. It is added in low and medium carbon steels in order to increase their yield and tensile strength properties. In combination with chromium, it produces a marked effect on the properties of steel and makes the steel extremely tough and strong. These steels are largely used for making spring steels, high speed tool steels, crankshafts etc.
4. Tungsten. The addition of tungsten raises the critical temperature of steel and hence it is used in increasing the strength of the alloyed steels at high temperature. It imparts cutting hardness and abrasion resistance properties to steel. When added to the extent of 5 to 6%, it gives the steel good magnetic properties and as such it is commonly used for magnets, in electrical instruments etc.
It is usually used in conjunction with other elements. Steel containing 18% tungsten, 4% chromium, 1% vanadium and 0.7% carbon is called as tool steel or high speed steel. Since the tools made with this steel have the ability to maintain its sharp cutting edge even at elevated temperature, therefore, it is used for making high speed cutting tools such as cutters, drills, dies, broaches, reamers etc.
5. Manganese. It is added to steel in order to reduce the formation of iron sulphide by combining with sulphur. It is usually added in the form of ferro-manganese or silico-mangenese. It makes the steel hard, tough and wear resisting.
Steel containing manganese varying from 10 to 14% and carbon from 1 to 1.3% form an alloy steel which is extensively hard and tough and a high resistance to abrasion. It is largely used for mining, rock crushing and railway equipment.
6. Silicon. It increases the strength and hardness of steel without lowering its ductility. Silicon steels containing from I to 2% silicon and 0.1 to 0.4% carbon have good magnetic permeability and high electrical resistance. It can withstand impact and fatigue even at elevated temperature. These steels are principally used for generators and transformers in the form of laminated cores.
7. Cobalt. It is added to high speed steel from 1 to 12%, to give red hardness by retention of hard carbides at high temperatures. It tends to decarburise steel during heat treatment. It increases hardness and strength but too much of it decreases impact resistance of steel. It also increases residual magnetism and coercive magnetic force in steel for magnets.
8. Molybdenum. A very small quantity (0.15 to 0.30%) of molybdenum is generally used with chromium and manganese (0.5 to 0.8%) to make molybdenum steel. These steels possess extra tensile strength and is used for air plane fuselage and automobile parts. It can replace tungsten in high speed steels.