Combustion Air and Turbine Exhaust Gas
Temperature and Composition
Oxygen used for supplementary firing in HRSG co-generation applications is provided by the residual in the turbine exhaust gas instead of from an external source of air. Because this flue gas is already at an elevated temperature, duct burner thermal efficiency can approach 100%, as relatively little heat is required to raise the combustion product temperature to the final fired temperature entering the boiler. TEG, however, contains less oxygen than fresh air, typically between 11 and 16% by volume, which in conjunction with the TEG temperature significantly affects the combustion process. As the oxygen concentration and TEG temperature decrease, products of incomplete combustion (CO and unburned hydrocarbons) occur more readily, eventually progressing to combustion instability.
The effect of low oxygen concentrations can be partially offset by higher temperature; and, conversely, higher oxygen concentrations will partially offset the detrimental effects of low TEG temperatures. This general relationship is shown in this figure.
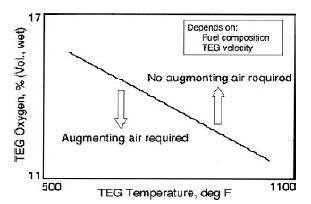
The burner can then be designed to create a local high temperature condition for stable combustion, while not allowing premature quenching by the remaining excess TEG. Flame speed is another measure of combustibility and can be calculated for unusual fuel constituents. The oxygen remaining from the turbine combustion is usually many times greater than required for supplemental firing. The final concentration of O2 after supplemental firing is frequently still above 10%. In the extreme, a fully fired boiler is possible, with the residual O2 as low as 2%. Fully fired HRSGs can produce large amounts of steam but are rare because the economics favor the power-to-heat ratio of unfired or supplemental fired HRSG.