Although Inventor allows you to import .stl mesh files, it doesn’t let you change or modify them as a normal modeling file. This means there is no way to add features or change shapes on .stl models that you may perhaps find at an online marketplace. This format, .stl, in fact, has been designed specifically to transfer data to 3d printing machines, and not for sharing modeling projects (check all the formats we accept on Sculpteo).
So if .stl is the format you have to modify, and you don’t have access to a better file format, then to bypass this limitation, you need to convert your .stl into a .dxf file, that Inventor is able to read as a modeling source.
To do so, you can use an online free tool, thanks to the great work of the guys of ‘CadForum’. You can go to CadForum’s converter and simply select your file, and choose .dxf as target format, it will be automatically converted.
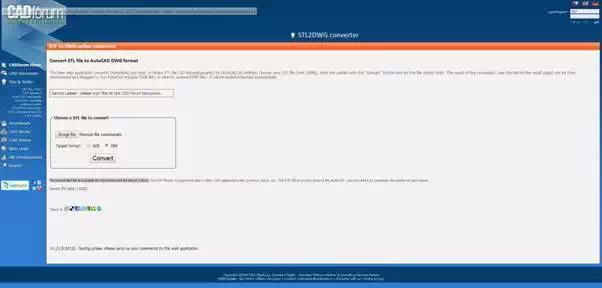
Once you are in possession of your .dxf converted .stl file, you can import it into Inventor and translate it into a modifiable 3d modeling file. Open a new file and select .dxf from the ‘File Type’ menu.
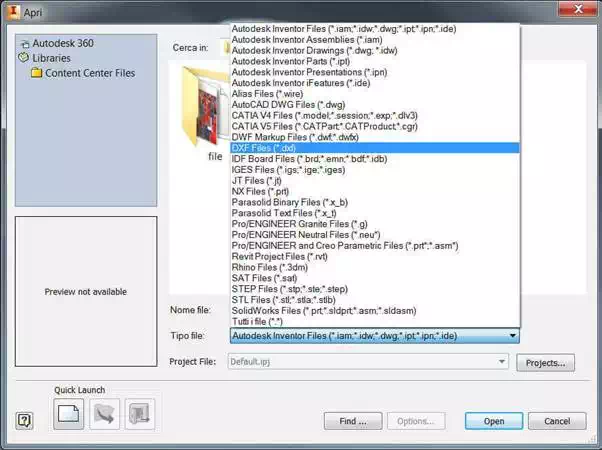
Select your file and press ‘Open’, and a .dxf import wizard, which allows you to choose its configuration options, will start. The default settings are normally fine, just remember to check the ‘3D solid’ box in the last panel.
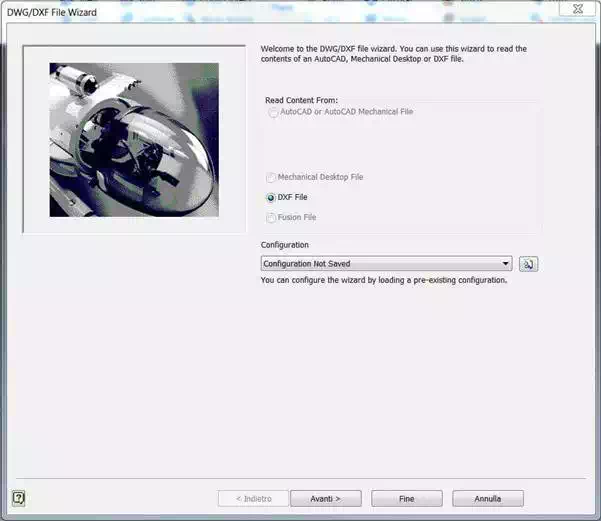
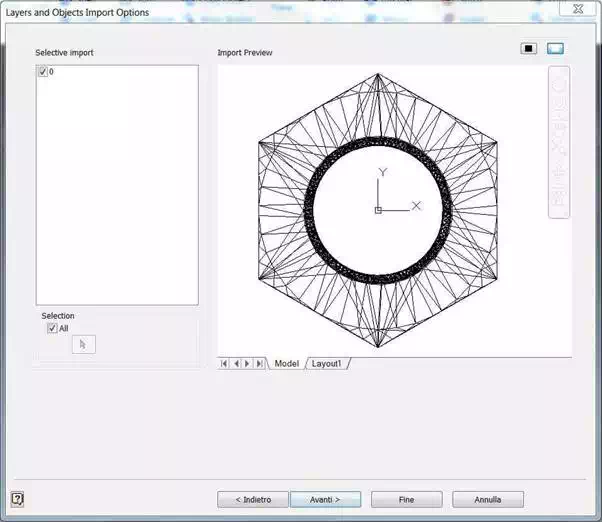
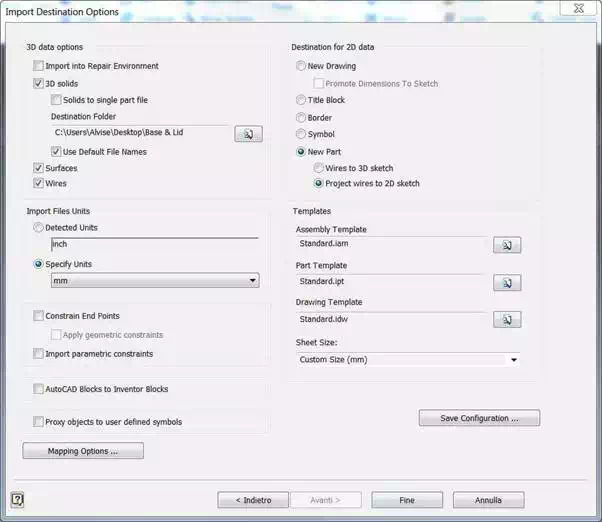
Press ‘End’ to close the wizard, you will see your model is being converted into a surface modeling file, this operation may take a while, depending on the number of polygons in your model.
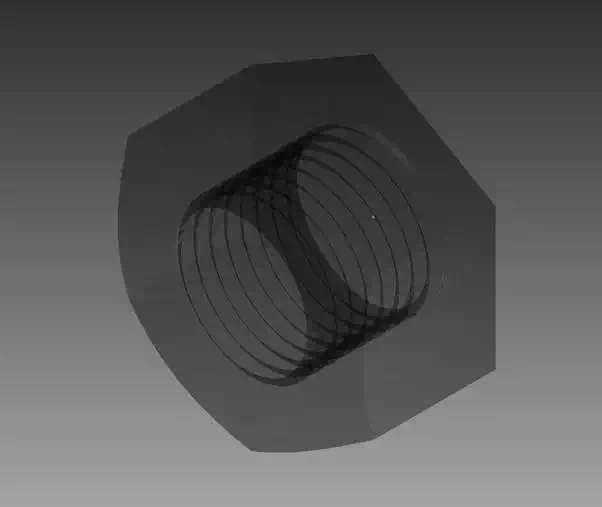
The last step in order to obtain a solid model from your .stl mesh is to stitch the surfaces you’ve created (Derived from the polygon faces of the mesh). To do so, choose ‘Stitch’ ( ), select the model and press ‘Apply’ on the ‘Stitch’ window. After some seconds, you will see it changing color and becoming a solid, that can be modified like a native file.
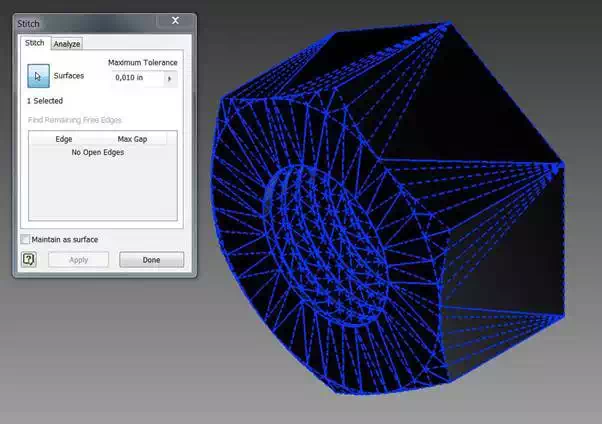
The defects of this process derive from the fact that what Inventor is doing is translating all the mesh’s polygons into surfaces to be stitched together, so it would be quite a different file compared to the one that would come out modeling it by ourselves, and the quality of the non-flat surfaces will depend on the quality of the mesh from which they derive. But on the other hand, a high definition mesh would take quite a long time to be calculated by the software. A good compromise needs to be found. Generally, we recommend you avoid translating meshes bigger than 100.000 polygons.
Take a look at what we mean by ‘the quality of the non-flat surfaces will depend on the quality of the mesh from which they derive’ on this cutaway view.
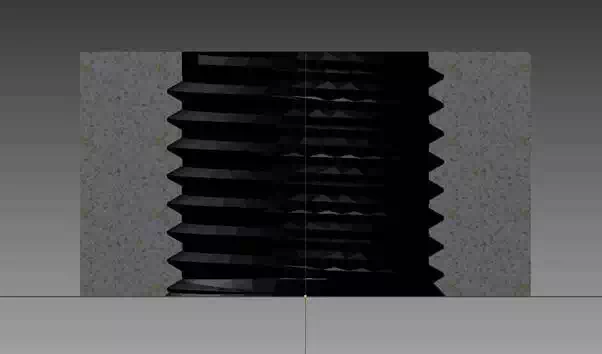