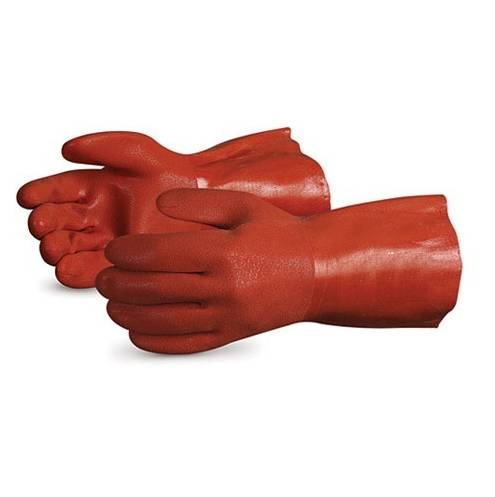
Selecting the right chemical protective gloves for your employees can be a challenging exercise. According to the Chemical Abstracts Service (CAS) registry, there are more than 60 million registered chemicals and even in in a typical production process or production facility, many different chemicals and mixes are used, and every unique set of chemicals requires specific chemical protection.
As we’ve discussed in previous blogs, because gloves come in a wide variety of barrier materials, thicknesses and designs, selecting the right materials for a chemical protective glove for your application is not an easy task and is deserving of special attention.
MATERIALS
The most common materials used as coatings for chemical protective gloves are:
§ Nitrile rubber
§ Polychloroprene (neoprene)
§ Butyl
§ Viton
§ Natural rubber or vinyl (PVC)
Because no one material can protect against every chemical and chemical mix, the perfect all-purpose barrier material mix is virtually non-existent. As such, a compromise will have to be made each time, with the goal of coming up with the best solution for the unique set of chemicals used in your application.
PERMEATION BREAKTHROUGH TIME
One of the key factors in finding the right gloves for chemical protection is the permeation breakthrough time. The permeation breakthrough time is a theoretical indication of how long it would take a certain chemical to permeate through the glove.
While there is data about breakthrough times that have been developed in standardized laboratory conditions, the problem is, those conditions don’t always reflect the real workplace circumstances. While the results can serve as a good guideline and permeation breakthrough times can be used to make a distinction between different materials, they usually can’t be interpreted as total usage times.
TAKING STEPS FOR CHEMICAL GLOVE SAFETY
Therefore, to select the best possible glove(s) for your specific needs, follow these 5 steps:
· Make an inventory of all chemicals used in your application. Select out of these the most commonly used chemicals on site and add those that pose specific health hazards. Remember, your analysis should factor for individual chemicals and the possible chemical mixtures that can occur.
· Consult your glove provider to help you with the visualization of permeation breakthrough times for your unique set of chemicals.
· Look at the application specific requirements and pick the best suited glove that utilizes the best possible glove material.
· Perform a practice test alongside an assessment of the usage time in your application.
· Follow-up on correct usage and care of the product to make sure the selected glove continues to be the best match. Ideally, your expert chemical glove assessment should provide a simplified set of choices, based on your needs, so you can make informed decisions with assurance and confidence.
Another concern is that your application might pose other specific comfort or mechanical needs beyond basic chemical protection. For example, based on application or task, workers may need a tactile glove, a glove with enhanced grip features or protection from heat.
While selecting the correct glove will often be a compromise, by using this methodology you can make the right compromise that protects your employees and serves the needs of your business.