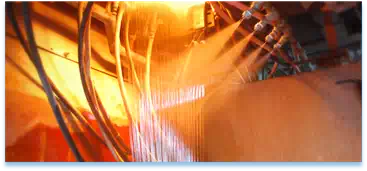
The most commonly used fibers are glass fibers. It consists of large number of enormously fine fibers of glasses. Glass fibers are divided into two types they are:
- Continuous fibers
- Discontinuous fibers
The glass is made up of silicon dioxide. Mainly the glass fibers are used for the structural applications. They come into two types they are E-glass and S-glass. We can observe that E-glass is produced in larger volume face to face to the E-glass
Advantages:
The main advantage are high strength and low cost.
Limitations of glass fiber are:
- Poor adhesion to specific polymer matrix materials
- Poor abrasion resistance causing reduced usable strength.
- Poor adhesion in humid environments.
To enhance their adhesion properties glass fibers are coated with chemicals. So chemicals are known as coupling agents. Many of those coupling agents are silane compounds.
Manufacturing of glass fibers:
By using partially similar method staple form and continuous form of glass are manufactured.
Stable form of fibers is manufactured by using the high pressure punishing air jets across the fibers. At the time of drawing process it originate holes.
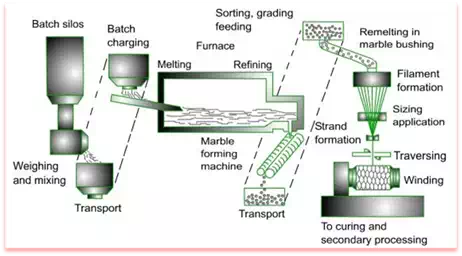
The fibers are collected and sprayed with the binder and they are collected into bundles and are known as slivers. And the silvers are subsequently twisted and drawn into the yarn.
Continuous form of fiber is manufactured by using the raw materials like alumina, sand and lime stone. All of them are mixed and then melted with the help of furnace at 1260 centigrade.
Melting:
Initially the glass fiber is manufactured by using either marble re-melt process or direct melt process. The process must starts with it is in raw material in solid state. In a furnace all the metals are mixed and then melted. In case of marbles process the molten substance should be sheared and then chilled into marbles which are cooled next for packing.
The marbles are occupied into the fiber manufacturing facility where they are injected into a container and then go for re-melting. To form a fiber, the molten metal must be extruded to the bushing. For formation the molten glass enters directly into the busing through the furnace.
Many of the glass are formed by using this method and in another case they use the marble method for formation. In next stage the marbles are drawn into the fibers. For the formation of fibers the molten glass material is passed into the multiple holes. The fibers are quenched through a light spray of water. And they are coated with lubricating agents and protective.
Glass fiber surface treatment:
During the time of production the glass fibers are treated with the chemicals. The process is known as sizes.
Those two types are
- Temporary
- Compatible
The temporary are process are used to reduce the degradation of the fiber power attributable to abrasion of fibers due to friction present in side during the drawing process.
For easy handling they are used to bind the fibers. Mainly they are made of starch oils like gelatin, polyvinyl alcohol, and starch. These sizes are constrained by good resin fiber adhesion. They are also act as a promote moisture absorption. At the time of fabrication these temporary and compatible are removed by applying the heat at 340 centigrade for 15 to 20 hours. The fibers are coated with the coupling agent promotes resin fiber adhesion. Agents also obstruct deteriorating things of moisture on the fiber resin bond. Most of the agents are organo practical silanes.