Background
8640 alloy steel is a special alloy of steel which was developed during World War II. 8640 steel was developed in part due to a shortage of chromium at the time. About half of the typical chromium content of 4630 steel was replaced with nickel. Scientists discovered that the combination of nickel and chromium resulted in a steel with great toughness and resistance to wear. Accordingly, 8640 alloy steel was widely used at the time in aircraft parts and other products for the war effort.
The composition of 8640 alloy steel is chromium (1.44 wt. %), manganese (.87 wt. %) nickel (0.56 wt. %), carbon (0.37 wt. %), silicon (0.25 wt. %), and molybdenum (0.18 wt. %). The primary alloying metals in 8640 steel are chromium, nickel, and molybdenum. 8640 steel is known for its toughness and the degree to which it can be hardened. It is also a very durable steel, which makes it ideal for use in forged hand tools.
The yield strength for oil-quenched and tempered 8640 steel is 1669 Megapascals; the elongation percentage is 10%, which is a relatively large value of ductility. Reduction of area is 40%.
Production and Uses of 8640 Steel
Due to its toughness and wear resistance, 8640 steel is commonly used as a tool steel. 8640 is a moderately hard steel, with a 505 rating on the Brinnell Hardness scale before hardening. In order to increase hardness and durability, 8640 steel is usually heat treated.
Heat treatment of 8640 steel is a multi-step process which involves “normalizing, annealing, hardening, tempering, and spheroidizing”1. All of these treatments may not necessarily be used in each sample, however. After heat treatment, the steel is typically given an oil quench. Upon the application of the previously mentioned treatments, 8640 steel develops a good balance of ductility to strength, enabling engineers to use it in a wide array of designs.
After heat treatment and quenching, 8640 steel is cast into a number of products. The most common products are bars, rods, billets, castings, and forgings. In addition, 8640 steel is a common element in aircraft parts such as landing gear and airframes. Other common uses include gears, crankshafts, screws, axles, pistons, and forged hand tools. Prior to forging, 8640 steel must be annealed.
Hand tools made from 8640 steel are fairly common. The properties of 8640 steel make tools manufactured from this alloy particularly strong and durable; in fact, NASA scientists considered using the material in spacecraft designs (unfortunately, they found that it cracked when they attempted to harden it to the desired levels). The 8640 steel used in tools is hardened, which has the effect of increasing the wear resistance of the tool. The method most typically used is oil quenching.
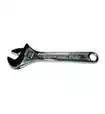