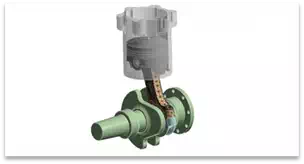
Transient dynamics analysis methods are used to predict the response of structures to dynamic loads. The outputs can include stresses and strains, velocities and accelerations, along with connection and constraint forces, for example. Furthermore, nonlinear transient dynamics can account for large rotations, contact, and material nonlinearities. While these analyses are very important, they often require long run times and considerable CPU resources, primarily because many time steps are required to capture the dynamic response. Time steps need to be small to account for critical response frequencies, abrupt changes in loading or contact status, and wave propagation effects (if applicable). These types of analyses can sometimes take days to run for real structures.
So, there is a strong need to speed up these types of analyses, especially when faced with tight deadlines on an FEA consulting project. One method is to use faster computers, more processors, and parallel solvers. However, this is not always practical and still may not yield the run time reductions needed for rapid turnaround. Another method is to incorporate rigid bodies. Some finite element software codes, including ANSYS, LS-Dyna, and AUTODYN, allow for parts to be designated as rigid. These parts are effectively reduced to bodies with six degrees of freedom with the appropriate masses and moments of inertia. Rigid bodies can be used in parts of a model where stress and strain results aren’t needed and where part flexibility is not critical to the response of the overall structure.
One type of transient dynamics analysis which is limited to only rigid bodies is known as a rigid-body or multi-body dynamics analysis. This type of analysis is typically used to model mechanisms because it can rapidly solve for the nonlinear response of multi-part structures using a type of explicit solver that is highly efficient for these types of analyses. Typically, a variety of joint types are used to simulate the connections between parts. However, some codes, including ANSYS, allow for more general contact types to be included with this solver. Output from these analyses includes useful information such the following:
● Range of motion in a mechanism
● Part accelerations and velocities
● Loads in each joint or contact interface
● Effects of springs and dampers
A hybrid solution option combines rigid and flexible bodies in the same analysis, yielding huge time savings because only the necessary components are modeled as flexible, with all other bodies considered rigid. Stresses and strains are computed only where required, producing solution fidelity in critical regions while minimizing overall computer time and resources. This is a powerful combination, providing the best of both worlds, and is recommend for your FEA consulting projects.
To demonstrate the advantages of using rigid bodies in a complex transient dynamics analysis of a mechanism, a model of an engine piston assembly was evaluated using the following methods:
1. All parts rigid – using the ANSYS rigid body dynamics solver
2. One part flexible – using the ANSYS implicit solve
3. All parts flexible – using the ANSYS implicit solver
The model was solved for a 0.2 second transient with a distributed vertical load applied to the top of the piston. The model with one flexible part is shown below in Figure 1. As you can see from Table 1, there is a huge run-time advantage to running with the rigid body dynamics solver. However, if stresses and strains are required, some flexible parts are necessary. In such cases, select bodies can be switched to flexible, offering a much faster and robust solution than a comparable model containing only flexible bodies.
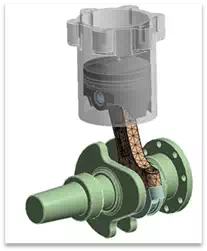
Figure 1: Engine Piston Assembly Model – Flexible Connection Rod Part